In the evolving field of battery manufacturing, precision and material purity are critical to ensuring optimal performance and safety. One of the most effective tools for improving the screening process of battery materials is the ultrasonic vibrating screen. This advanced screening technology is gaining widespread adoption due to its ability to significantly enhance the precision and efficiency of material separation, while effectively removing impurities.
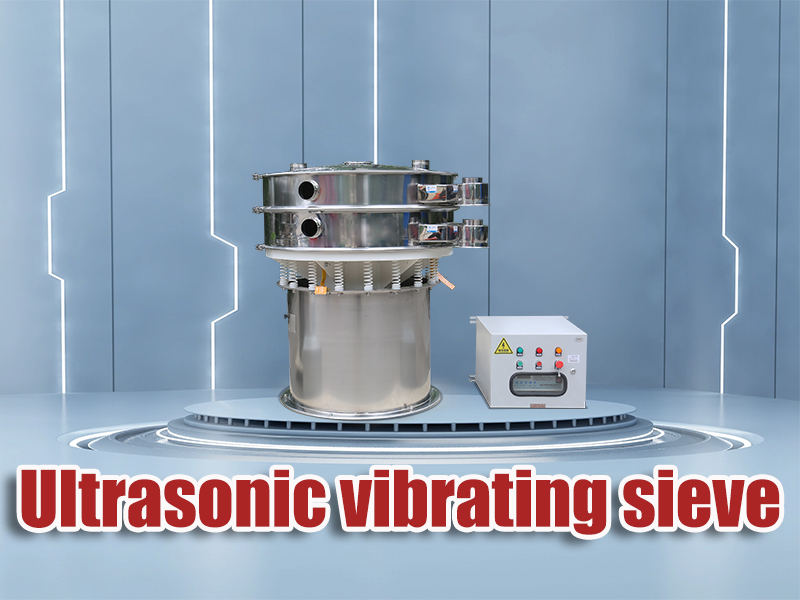
The ultrasonic vibrating screen integrates traditional vibratory screening with high-frequency ultrasonic waves. These ultrasonic vibrations are superimposed onto the screen mesh, creating micro-vibrations that prevent mesh clogging and improve the passage of fine particles. This is particularly important when screening fine powders commonly used in battery production, such as lithium carbonate, lithium iron phosphate (LFP), nickel, cobalt, graphite, and other conductive or active materials.
One of the standout benefits of ultrasonic screening technology is its ability to increase screening accuracy by over 80% compared to conventional methods. The incorporation of ultrasonic energy allows for more precise separation of particles by size, ensuring consistent granularity and better product uniformity. This is essential in battery manufacturing, where even slight variations in material size or composition can impact battery life, energy density, and thermal stability.
In addition to its precision, the ultrasonic vibrating screen excels in impurity removal. The fine, high-frequency vibrations efficiently dislodge contaminants and oversized particles, resulting in cleaner and purer output materials. This leads to a higher quality end product and helps manufacturers meet increasingly stringent industry standards.
Moreover, the system is adaptable to a wide range of material properties and screening requirements. Whether processing nano-scale powders or coarser bulk materials, the ultrasonic screen can be adjusted to match specific needs, including moisture content, bulk density, and particle hardness. This flexibility makes it an ideal choice for battery producers handling multiple materials with different specifications.
From reducing material waste to increasing throughput and improving product consistency, the ultrasonic vibrating screen is an indispensable asset in modern battery material processing. Its ability to deliver exceptional screening precision and impurity removal efficiency positions it as a vital component in achieving high-quality, high-performance battery materials.
As the demand for high-capacity, long-lasting, and safe energy storage systems continues to grow, investing in technologies that enhance material processing at the granular level—such as the ultrasonic vibrating screen—will be a decisive factor for manufacturers seeking to maintain a competitive edge.