In the rapidly evolving battery industry, the demand for high-performance materials has grown significantly. The quality and purity of battery materials play a critical role in determining the overall performance, efficiency, and lifespan of batteries. One of the most effective technologies used for the refinement and screening of battery materials is the ultrasonic vibrating screen. This advanced screening solution has become a key tool for removing impurities and ensuring that battery materials meet the stringent quality standards required for modern battery production.
The Importance of High-Purity Battery Materials
Battery performance is highly dependent on the purity and consistency of the materials used in production. Impurities, such as metal particles, dust, and other foreign substances, can significantly degrade the performance of the battery. They can cause internal short circuits, reduce conductivity, and lead to premature battery failure. In industries like electric vehicles (EVs), consumer electronics, and renewable energy storage, maintaining the highest level of material purity is essential for ensuring product reliability and safety.
To meet these demands, manufacturers are increasingly adopting ultrasonic vibrating screens to refine battery materials such as lithium, cobalt, nickel, manganese, and other critical components. These materials require precise particle size distribution and impurity-free consistency to maximize battery performance and longevity.
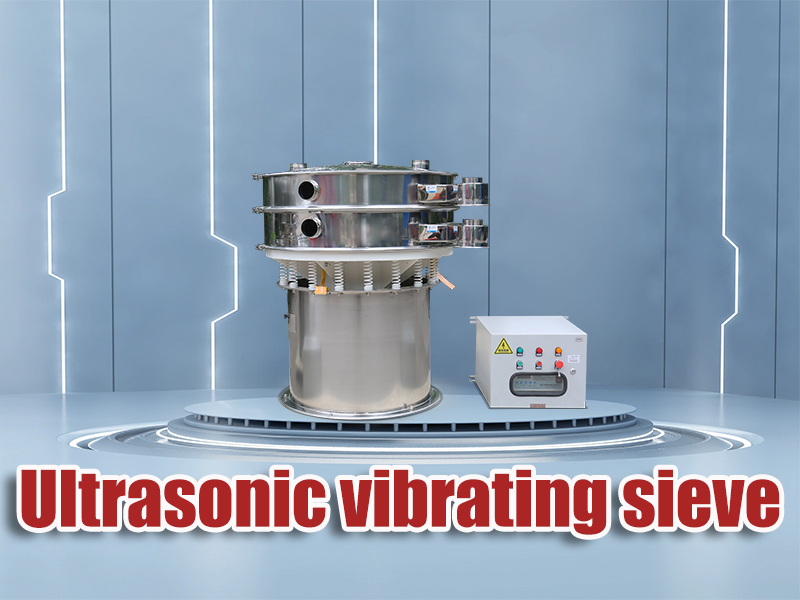
How Ultrasonic Vibrating Screens Work
Ultrasonic vibrating screens use a combination of traditional vibration and high-frequency ultrasonic waves to achieve more efficient and precise screening. The system typically consists of a vibrating base, a mesh screen, and an ultrasonic generator. The ultrasonic generator converts electrical energy into high-frequency mechanical vibrations that are transmitted to the mesh screen.
The high-frequency vibrations create a secondary ultrasonic oscillation on the screen surface, which has several key benefits:
- Prevention of Mesh Blinding – Traditional vibrating screens often suffer from clogging or blinding when fine particles accumulate and block the screen openings. The ultrasonic vibration helps to keep the screen surface clean by dislodging particles and preventing buildup.
- Enhanced Screening Accuracy – The ultrasonic energy allows even the finest particles to pass through the screen mesh, improving the precision of the particle size separation. This ensures that only materials of the correct size are retained, while impurities and oversized particles are effectively removed.
- Increased Screening Efficiency – The combination of mechanical vibration and ultrasonic energy increases the screening speed and efficiency, allowing for higher throughput without compromising accuracy.
Advantages of Ultrasonic Vibrating Screens in the Battery Industry
The use of ultrasonic vibrating screens for battery material processing provides several distinct advantages:
1. Higher Purity and Quality Control
By effectively removing impurities and ensuring consistent particle size, ultrasonic vibrating screens help battery manufacturers maintain strict quality control standards. This leads to better-performing batteries with improved charge capacity, longer lifespan, and greater safety.
2. Reduced Material Loss and Waste
Conventional screening methods can result in the loss of fine materials during the screening process. Ultrasonic screening minimizes material loss by improving the accuracy of the separation process and ensuring that valuable materials are retained.
3. Compatibility with a Wide Range of Materials
Ultrasonic vibrating screens are highly versatile and can be used to process a wide range of battery materials, including:
- Lithium iron phosphate (LFP)
- Lithium nickel manganese cobalt oxide (NMC)
- Lithium cobalt oxide (LCO)
- Graphite and carbon materials
- Metal oxides and other conductive materials
4. Improved Production Efficiency
The enhanced screening speed and accuracy reduce processing time, enabling manufacturers to increase production output while maintaining high standards of quality. This is particularly important in the competitive battery industry, where manufacturers are under pressure to meet increasing demand for electric vehicles and renewable energy storage systems.
5. Reduced Equipment Wear and Maintenance
The ultrasonic vibration reduces friction and material buildup on the screen mesh, resulting in less wear and tear on the equipment. This extends the lifespan of the screening machine and reduces maintenance costs over time.
Application Scenarios in the Battery Industry
Ultrasonic vibrating screens are widely used in various stages of battery production, including:
- Raw Material Processing – Screening raw materials to ensure uniform particle size and remove impurities before entering the production line.
- Cathode and Anode Material Screening – Separating fine particles to improve the consistency and conductivity of cathode and anode materials.
- Electrolyte Powder Screening – Ensuring that electrolyte powders meet precise particle size requirements to improve battery performance.
- Battery Recycling – Separating valuable materials from recycled batteries for reuse in the manufacturing process.