Metal powders are widely used in industries such as additive manufacturing, metallurgy, and coatings, requiring precise classification to ensure product quality. Traditional vibration screening methods often struggle with issues such as mesh clogging, reduced throughput, and inconsistent particle separation. The introduction of ultrasonic vibration screens has revolutionized the screening process by addressing these challenges effectively.
Working Principle of Ultrasonic Vibration Screens
Ultrasonic vibration screens incorporate high-frequency ultrasonic waves into the traditional vibration screening process. These waves, typically in the range of 20–40 kHz, generate micro-vibrations on the screen mesh, preventing particles from adhering to the mesh surface. This mechanism enhances the efficiency of particle separation and significantly reduces mesh blinding.
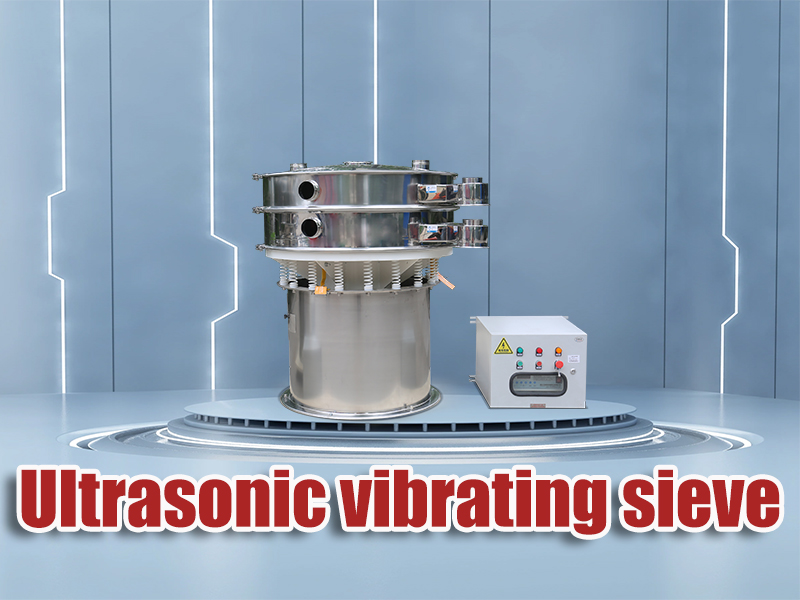
Advantages of Ultrasonic Vibration Screens
- Prevention of Mesh Clogging: The ultrasonic vibrations keep the screen mesh clear, allowing continuous operation without frequent cleaning interruptions.
2. Enhanced Screening Accuracy: Higher screening precision is achieved as fine metal particles are efficiently separated, leading to improved product quality.
3. Increased Throughput: The elimination of clogging and improved material flow contribute to higher productivity.
4. Extended Screen Life: Reduced mechanical stress on the mesh prolongs the lifespan of the screening equipment.
5. Compatibility with Various Metal Powders: Suitable for a wide range of metal powders, including aluminum, titanium, and stainless steel.
Applications of Ultrasonic Screening in Metal Powder Industry
- Additive Manufacturing: Ensures uniform particle size distribution for 3D printing applications.
- Metallurgy: Facilitates efficient classification of metal powders for sintering and alloy production.
- Coatings and Surface Treatment: Helps in the refinement of fine metal powders for high-quality coatings.
- Electronics: Assists in screening conductive metal powders for electronic components.
Challenges and Future Improvements
While ultrasonic vibration screens offer numerous benefits, certain challenges remain:
- Energy Consumption: High-frequency vibrations require additional power, impacting operational costs.
- Initial Investment: The cost of ultrasonic screening systems is higher compared to traditional methods.
- Material-Specific Limitations: Some metal powders with irregular shapes or high moisture content may still present screening difficulties.
Future advancements in ultrasonic screening technology may focus on optimizing energy efficiency, developing cost-effective designs, and integrating AI-driven automation for enhanced process control.