Graphite powder is a crucial material used in various industries, including electronics, battery manufacturing, and metallurgy. The screening of graphite powder can be particularly challenging due to its fine particle size, adhesive properties, and tendency to form agglomerates. Traditional screening methods often struggle to handle these challenges efficiently, leading to issues such as mesh clogging, reduced throughput, and poor separation accuracy.
To address these difficulties, ultrasonic vibrating screens have been developed, combining traditional vibration screening with ultrasonic technology. This innovation has greatly improved the screening process for graphite powder, offering enhanced precision, higher efficiency, and a more reliable production process.
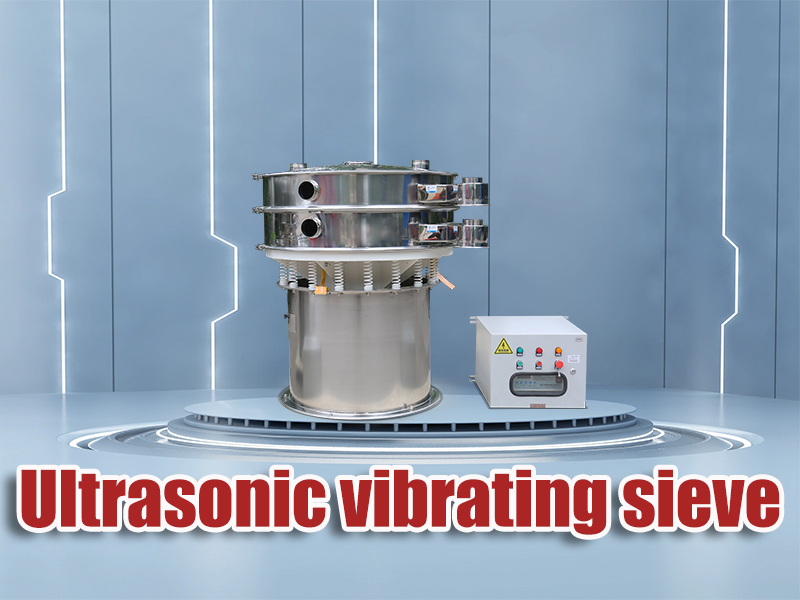
Challenges in Screening Graphite Powder
Graphite powder, particularly in its fine form, presents several unique challenges during the screening process:
- Clumping and Agglomeration: Due to its fine and cohesive nature, graphite powder tends to form clumps or agglomerates, which obstruct the flow of material through the screen mesh and can lead to blockages.
- Mesh Clogging: The fine particles of graphite have a tendency to clog the screen mesh, slowing down the process and reducing the efficiency of the operation.
- Electrostatic Properties: Graphite powder can develop a static charge, causing it to adhere to the mesh, which not only hinders the screening process but also increases maintenance requirements.
- Low Throughput: The accumulation of material on the screen surface can lead to a reduced throughput, causing longer processing times and potential product inconsistencies.
These issues necessitate the need for an advanced screening solution that ensures smooth operation and high-quality results.
The Ultrasonic Vibrating Screen Solution
The ultrasonic vibrating screen provides a highly effective solution for screening graphite powder, integrating ultrasonic waves with traditional vibrating screening mechanisms. The high-frequency ultrasonic vibrations improve the flow of material and prevent common issues such as clumping, adhesion, and clogging.
1. Preventing Clumping and Agglomeration
Ultrasonic vibrations play a critical role in preventing the formation of agglomerates and breaking up existing clumps. These vibrations reduce the cohesive forces between particles, ensuring smooth material flow and minimizing blockages.
- Improved Flowability: Ultrasonic energy disrupts the cohesive bonds between fine graphite particles, helping them to flow more freely through the screen mesh.
- Efficient Separation: The ultrasonic waves ensure that the graphite particles are separated more efficiently, achieving a finer particle classification.
2. Enhanced Screening Precision
One of the key benefits of using an ultrasonic vibrating screen is its ability to achieve higher screening precision for fine powders like graphite. The ultrasonic technology ensures that the desired particle sizes are separated with greater accuracy, improving the overall quality of the final product.
- Finer Separation: Ultrasonic vibrating screens can separate graphite powder down to 5 microns, ensuring precise particle size distribution.
- Consistent Results: The ultrasonic system delivers consistent and uniform separation, reducing the variation in the quality of the processed material.
3. Increased Throughput and Productivity
Ultrasonic vibrating screens improve throughput by reducing screen mesh clogging and increasing material flow. With less downtime for cleaning and fewer blockages, production efficiency is greatly enhanced.
- Higher Production Rates: The continuous operation of the screen with fewer interruptions allows for a 2-5x higher output compared to traditional vibrating screens.
- Reduced Maintenance Time: Ultrasonic technology minimizes the need for frequent maintenance and mesh cleaning, reducing downtime and increasing overall productivity.
4. Reduction in Contamination and Wear
Conventional screens can lead to contamination of the graphite powder due to excessive friction and wear. Ultrasonic vibrating screens reduce wear on the screen mesh and prevent contamination, ensuring the material is handled delicately and remains of high quality.
- Cleaner Material: The ultrasonic vibrations ensure that the graphite powder remains free from contaminants, preserving the purity of the final product.
- Longer Equipment Life: By minimizing mesh clogging and wear, ultrasonic vibrating screens extend the life of the equipment, reducing maintenance costs.
5. Energy-Efficient Operation
The ultrasonic vibrating screen is energy-efficient, using 220V electrical power to generate 36kHz ultrasonic mechanical vibrations. This results in low power consumption while delivering effective and fast screening.
- Low Power Consumption: The ultrasonic vibrating screen consumes less power than traditional vibrating screens, making it an environmentally friendly and cost-effective solution.
- Efficient Energy Use: The conversion of electrical energy into high-frequency mechanical vibrations enhances the material separation process without wasting energy.
Applications in Graphite Powder Processing
Ultrasonic vibrating screens are widely used in industries where graphite powder is a key material. Some of the notable applications include:
- Battery Manufacturing: Graphite is a vital material in the production of lithium-ion batteries, used in everything from electric vehicles to portable electronics. The ultrasonic vibrating screen ensures that graphite particles are the correct size and free from contaminants, improving battery performance and reliability.
- Electronics Industry: Graphite powder is used in the production of electronic components like electrodes and conductive materials. The precision offered by ultrasonic screening ensures that the particles meet strict quality standards required for high-tech applications.
- Lubricants and Coatings: Graphite powder is used in lubricants, coatings, and other formulations that require a fine and consistent particle size. The ultrasonic vibrating screen helps achieve the required consistency and purity.
- Refractories and Metallurgy: Graphite is also used in the production of refractories and other high-temperature applications. The ultrasonic screen ensures that the graphite powder is finely screened and free from impurities, resulting in high-quality materials for industrial processes.