The battery industry, particularly in the production of advanced energy storage systems, relies heavily on the precise processing of battery materials. Materials like lithium, cobalt, and nickel are often used in battery manufacturing, and these materials, in powder form, must undergo a careful screening process to meet high-quality standards. However, the fine powders used in the battery industry can present significant challenges during screening, including clumping, adhesion to mesh, and high static charge.
To overcome these challenges, the use of ultrasonic vibrating screens has gained increasing attention. By integrating ultrasonic technology with traditional vibrating screens, it provides a superior solution for screening battery material powders, ensuring higher precision, efficiency, and quality.
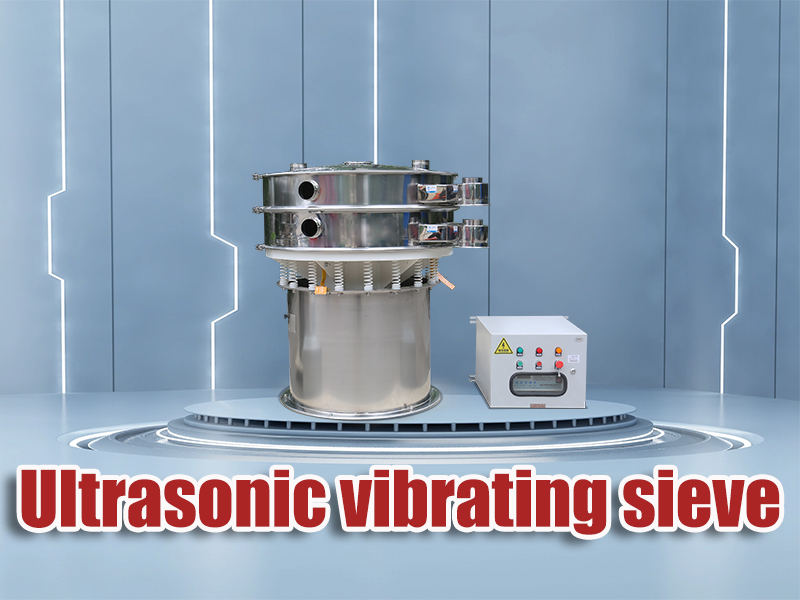
Challenges in Screening Battery Material Powders
Battery materials in powder form present several unique challenges during the screening process:
- Clumping and Agglomeration: Fine powders tend to form clumps due to their cohesive nature, especially when dealing with high-density materials like those used in batteries.
- Adhesion to Screen Mesh: Fine powders, particularly those with high static charges, can easily adhere to the screen mesh, obstructing proper material flow and reducing throughput.
- Mesh Blockages: Due to the small size of the particles, traditional vibrating screens can become easily clogged, leading to inefficiency and production delays.
Given these challenges, there is a strong demand for more efficient and effective screening solutions.
The Ultrasonic Vibrating Screen Solution
An ultrasonic vibrating screen solves these issues by combining traditional vibration with ultrasonic waves that help to break down agglomerates and prevent clumping. These high-frequency ultrasonic vibrations enhance the overall performance of the screening process for fine battery material powders.
1. Preventing Clogging and Agglomeration
Ultrasonic vibrations prevent clogging and agglomeration, which are common issues when screening fine powder materials. The ultrasonic energy helps to break down clumps of battery powder, ensuring the material passes through the screen mesh smoothly.
- Improved Material Flow: Ultrasonic technology helps to reduce friction between particles, promoting smoother flow and preventing material buildup on the screen.
- No Material Blockage: Fine materials, such as battery powders, that tend to adhere to screens are easily separated without any blockages.
2. Enhanced Screening Precision
Battery materials, especially those used in high-performance batteries, require precise screening to ensure quality control. Ultrasonic vibrating screens enhance the screening precision for even the smallest particles, ensuring only the required particle sizes are separated.
- Improved Separation: The ultrasonic vibrations create a more efficient particle separation process, allowing for higher precision in separating different grades of battery material powder.
- Finer Mesh Size: Ultrasonic vibrating screens are capable of screening powders down to 5 microns, ensuring that only the most accurately sized particles are selected.
3. Increased Output and Efficiency
Ultrasonic vibrating screens increase the output and efficiency of the screening process by reducing material buildup and increasing throughput.
- Higher Throughput: With ultrasonic waves assisting in the breakdown of clumps and preventing mesh blockages, the screen operates more smoothly and can handle 2-5 times more material per unit of time compared to traditional screens.
- Continuous Operation: The reduced frequency of downtime for cleaning and maintenance increases overall production efficiency.
4. Reduced Contamination and Wear
Conventional screening processes can sometimes lead to contamination of the material due to friction and excessive wear on the screen mesh. Ultrasonic vibrating screens minimize these issues by reducing the mechanical wear and preventing material contamination.
- Cleaner Product: The reduction in mesh blockages and contamination helps to maintain the purity of the battery material powder, which is essential for the production of high-performance batteries.
- Longer Equipment Lifespan: The ultrasonic vibrations reduce the wear and tear on the screen mesh, increasing the lifespan of the equipment and reducing maintenance costs.
5. Energy-Efficient Operation
The ultrasonic vibrating screen is highly energy-efficient, converting 220V electrical energy into 36 kHz mechanical vibrations with low power consumption, making it an environmentally friendly and cost-effective solution.
- Low Energy Consumption: Ultrasonic screens use less power compared to conventional vibrating screens, reducing operational costs.
- Efficient Use of Energy: The conversion of electrical energy into high-frequency mechanical vibrations ensures efficient material separation without unnecessary energy waste.
Applications of Ultrasonic Vibrating Screens in Battery Manufacturing
In the production of battery materials, precision and efficiency are paramount. Ultrasonic vibrating screens have proven to be particularly beneficial for the following applications:
- Lithium Battery Manufacturing: Lithium powder is widely used in battery production. The ultrasonic vibrating screen helps ensure that only the finest lithium particles are used, optimizing battery performance.
- Nickel and Cobalt Screening: Nickel and cobalt, essential in the production of high-capacity batteries, can be difficult to screen. Ultrasonic vibrating screens ensure consistent separation of these materials.
- Graphite Powder Screening: Graphite is used in the anodes of lithium-ion batteries. The ultrasonic vibrating screen ensures high precision in screening graphite powder, ensuring only the correct particle sizes are used in manufacturing.
- Powdered Electrodes: In the production of battery electrodes, precise powder separation is crucial. Ultrasonic vibrating screens ensure that only the correct size powders are used for electrode manufacturing.