In the world of fine material processing, silica powder, particularly ultrafine silica powder, presents significant screening challenges. These challenges arise due to the powder’s high fineness, tendency to clump, and adhesive properties that make it difficult to process using conventional screening technologies. As industries demand more precision and efficiency in the separation of fine powders, ultrasonic vibrating screens have emerged as a powerful solution.
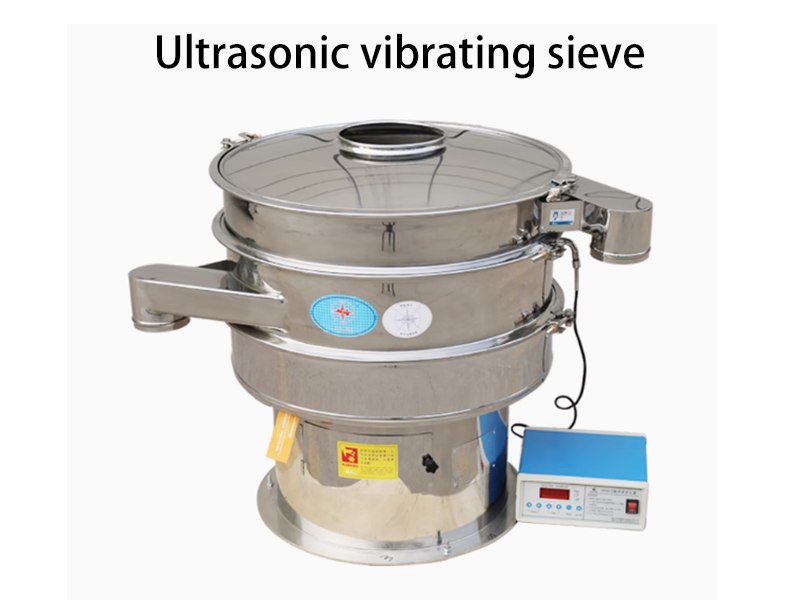
In this article, we will explore how ultrasonic vibrating screens can effectively screen ultrafine silica powder, overcoming traditional difficulties and enhancing production efficiency.
Challenges in Screening Ultrafine Silica Powder
Silica powder, especially the ultrafine variety, presents several problems during the screening process. These include:
- Clumping and Agglomeration: Fine silica particles tend to stick together due to their cohesive nature, which can block the screen mesh and reduce screening efficiency.
- High Static Charge: Ultrafine silica particles often carry static charges, causing them to attract to the screen mesh and each other, leading to material buildup and blockages.
- Mesh Clogging: The small particle size of silica powder can lead to clogging of the mesh, preventing accurate separation and reducing throughput.
These issues can hinder production, leading to downtime, maintenance costs, and compromised product quality.
The Ultrasonic Vibrating Screen Solution
The ultrasonic vibrating screen combines traditional screening technology with ultrasonic waves to enhance the efficiency of processing fine and difficult-to-handle materials like ultrafine silica powder. The ultrasonic waves are transmitted to the screen mesh, creating high-frequency vibrations that prevent clogging and ensure a smooth flow of material.
1. Effective Screening of Ultrafine Silica Powder
The primary benefit of using an ultrasonic vibrating screen for ultrafine silica powder is its ability to efficiently separate particles without causing blockages or agglomeration. The ultrasonic vibrations reduce the cohesive forces between the particles, ensuring that they pass through the mesh with minimal resistance.
- Prevents Clogging: Ultrasonic vibrations prevent the fine silica particles from sticking to the screen mesh, eliminating frequent downtime for cleaning.
- Enhances Material Flow: The high-frequency vibrations reduce friction between particles, ensuring smoother material flow and preventing agglomeration.
2. Improved Screening Precision
Ultrasonic vibrating screens significantly improve the screening precision for ultrafine silica powder. The ultrasonic waves help achieve a finer separation of particles, resulting in more accurate and consistent product quality.
- Higher Fineness: The screen can separate particles as fine as 5 microns, ensuring that even the smallest particles are accurately classified.
- Higher Yield: With enhanced separation precision, manufacturers can achieve higher yields and produce more products per unit of material.
3. Increased Efficiency and Productivity
By preventing the common issues of clogging and agglomeration, ultrasonic vibrating screens increase throughput and reduce the need for frequent maintenance. This translates into higher production efficiency and less downtime.
- 2-5x Higher Output: The ultrasonic vibrations increase the overall throughput of the screen, resulting in a production capacity that is 2 to 5 times greater than traditional screening methods.
- Reduced Maintenance Time: Less material buildup on the mesh means fewer interruptions and a smoother production process.
4. Enhanced Product Quality
Ultrasonic vibrating screens provide a cleaner and more precise separation of silica particles, which improves the quality of the final product. The reduced contamination and the ability to process ultra-fine particles ensures that the product meets industry standards.
- Cleaner Output: The enhanced separation leads to a purer final product with fewer impurities.
- Consistency: The machine ensures that each batch of silica powder maintains consistent particle sizes, improving overall product quality.
5. Noise Reduction and Improved Working Conditions
Another advantage of the ultrasonic vibrating screen is its ability to reduce noise levels during operation. The integration of ultrasonic technology helps minimize the vibration intensity, creating a quieter work environment.
- Lower Noise Levels: Compared to conventional vibrating screens, ultrasonic screens generate less noise, improving working conditions.
- Less Vibrational Wear: The ultrasonic waves reduce the vibrational impact on both the material and the equipment, leading to longer equipment lifespan and less wear.
Applications in Industries Using Ultrafine Silica Powder
Ultrafine silica powder is used across various industries, including:
- Electronics: Silica is used in the manufacturing of semiconductors and optical fibers. The precision screening of ultrafine silica powder ensures that the final product meets the highest standards for quality and consistency.
- Cosmetics: In the cosmetics industry, silica is used in formulations for powders and creams. The ultrasonic vibrating screen ensures the powder is free of contaminants and is perfectly sized for its intended use.
- Pharmaceuticals: Silica is also used in pharmaceutical formulations. The precise separation and impurity removal achieved by the ultrasonic vibrating screen ensure that the silica powder is suitable for use in sensitive applications like drug delivery systems.
- Paints and Coatings: Silica is used in the production of paints and coatings, where particle size uniformity and purity are crucial. The ultrasonic vibrating screen helps achieve the desired consistency and quality in these products.