Ultrasonic vibrating screens are advanced screening machines that combine mechanical vibration with ultrasonic technology to achieve high precision and efficiency in particle separation. To ensure their optimal performance and longevity, proper care and maintenance are essential. This guide provides a comprehensive overview of the steps and best practices for maintaining ultrasonic vibrating screens, helping operators minimize downtime, reduce repair costs, and extend the lifespan of their equipment.
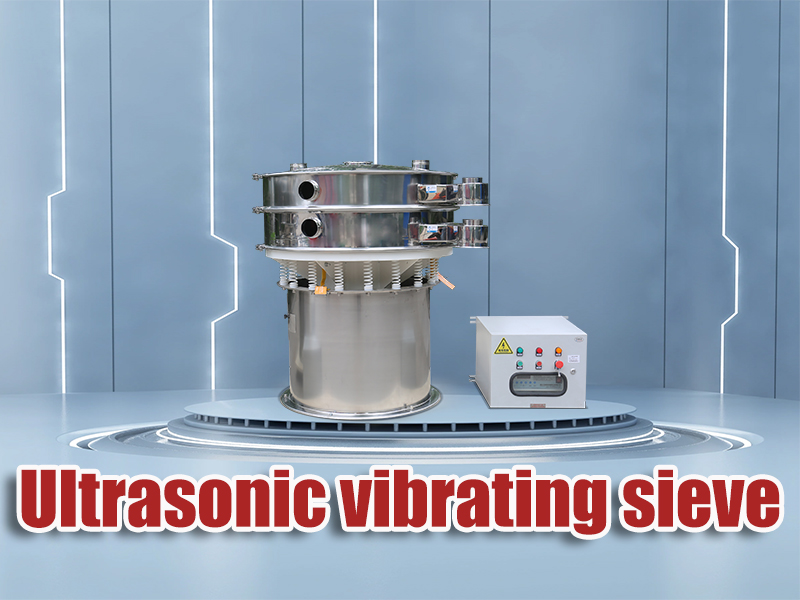
Importance of Regular Maintenance
Regular maintenance of ultrasonic vibrating screens is crucial for several reasons:
- Preventing Downtime: Proper maintenance reduces the risk of unexpected breakdowns, ensuring continuous operation.
- Maintaining Screening Efficiency: Well-maintained screens deliver consistent performance and accurate particle separation.
- Extending Equipment Life: Routine care helps prevent wear and tear, prolonging the lifespan of the machine.
- Ensuring Safety: Regular inspections and maintenance help identify potential safety hazards, protecting operators and equipment.
Daily Care and Maintenance
- Inspect the Screen Mesh
- Check the screen mesh for signs of wear, tears, or clogging.
- Clean the mesh using a soft brush or compressed air to remove any trapped particles.
- Ensure the mesh is properly tensioned to avoid sagging or damage.
2. Check the Ultrasonic System
- Inspect the ultrasonic transducer and generator for any signs of damage or malfunction.
- Ensure all connections are secure and free from dust or debris.
- Verify that the ultrasonic system is operating at the correct frequency and amplitude.
3. Clean the Machine
- Wipe down the screen frame, housing, and other components with a clean, damp cloth.
- Use food-grade cleaning agents for machines used in the food or pharmaceutical industries.
- Avoid using abrasive materials or harsh chemicals that could damage the equipment.
4. Lubricate Moving Parts
- Apply lubricant to bearings, motors, and other moving parts as recommended by the manufacturer.
- Avoid over-lubrication, as excess lubricant can attract dust and debris.
Weekly Maintenance
- Inspect Vibrating Motors
- Check the vibrating motors for unusual noises, vibrations, or overheating.
- Tighten any loose bolts or screws on the motor mounts.
- Ensure the motor is properly aligned and functioning smoothly.
2. Examine Electrical Components
- Inspect wiring, connectors, and switches for signs of wear or damage.
- Test the ultrasonic generator to ensure it is functioning correctly.
- Replace any damaged or worn electrical components immediately.
3. Test Screen Performance
- Run a test screening to ensure the machine is operating at peak efficiency.
- Monitor the screening process for any irregularities, such as uneven particle distribution or clogging.
Monthly Maintenance
- Deep Clean the Machine
- Disassemble the screen frame and mesh for a thorough cleaning.
- Remove any buildup of material from hard-to-reach areas.
- Inspect and clean the ultrasonic transducer and generator.
2. Check for Wear and Tear
- Inspect the screen mesh, frame, and other components for signs of wear or damage.
- Replace worn or damaged parts, such as the mesh, gaskets, or seals.
- Ensure all bolts, nuts, and fasteners are securely tightened.
3. Calibrate the Ultrasonic System
- Verify that the ultrasonic system is operating at the correct frequency and amplitude.
- Adjust the settings as needed to optimize screening performance.
- Consult the manufacturer’s guidelines for calibration procedures.
Annual Maintenance
- Comprehensive Inspection
- Conduct a thorough inspection of the entire machine, including mechanical, electrical, and ultrasonic components.
- Replace any worn or damaged parts, such as bearings, motors, or screens.
- Check the structural integrity of the machine frame and supports.
2. Professional Servicing
- Schedule a professional servicing by a qualified technician.
- Have the technician inspect and tune the ultrasonic system, motors, and other critical components.
- Ensure the machine is calibrated to factory specifications.
Troubleshooting Common Issues
- Screen Clogging
- Ensure the ultrasonic system is functioning correctly.
- Clean the screen mesh thoroughly and check for proper tension.
- Adjust the vibration frequency or amplitude to improve material flow.
2. Reduced Screening Efficiency
- Inspect the screen mesh for wear or damage and replace if necessary.
- Check the ultrasonic system for proper operation.
- Verify that the material being screened is within the recommended size and moisture range.
3. Unusual Noises or Vibrations
- Inspect the vibrating motors and bearings for wear or damage.
- Tighten any loose bolts or screws.
- Ensure the machine is properly leveled and stable.
4. Ultrasonic System Failure
- Check the connections between the transducer, generator, and power supply.
- Inspect the transducer for damage or wear and replace if necessary.
- Consult the manufacturer’s troubleshooting guide or contact technical support.
Best Practices for Ultrasonic Vibrating Screen Care
- Follow the Manufacturer’s Guidelines: Always adhere to the maintenance schedule and recommendations provided by the manufacturer.
- Train Operators: Ensure operators are trained in proper machine operation and maintenance procedures.
- Keep Records: Maintain a log of maintenance activities, inspections, and repairs for future reference.
- Use Genuine Parts: Replace worn or damaged components with genuine parts from the manufacturer to ensure compatibility and performance.