Sodium feldspar is a crucial industrial mineral widely used in ceramics, glass manufacturing, and chemical applications. To ensure its optimal performance in these industries, precise particle size classification is essential. Traditional screening methods often face challenges such as mesh clogging, low efficiency, and inconsistent particle separation. However, the ultrasonic vibrating screen has emerged as an advanced solution for accurately classifying sodium feldspar, improving efficiency, and ensuring high product quality.
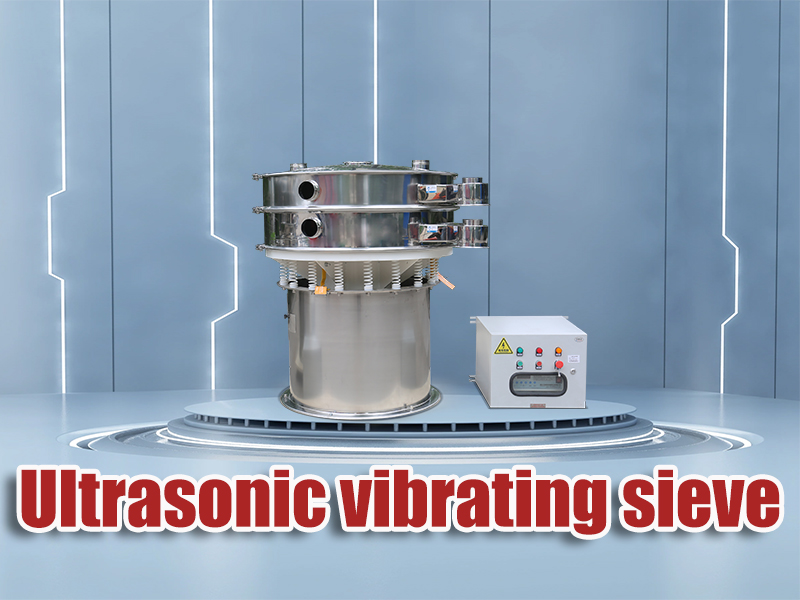
Why Accurate Classification of Sodium Feldspar Matters?
The particle size distribution of sodium feldspar directly affects its performance in various industrial applications:
- Ceramics & Glass Production: Uniform particle size improves melting behavior, leading to stronger and more durable products.
- Chemical Industry: Consistent granularity enhances reactivity and processing efficiency.
- Abrasives & Fillers: Fine and precisely classified feldspar ensures better dispersion and performance in composite materials.
To achieve these benefits, an advanced screening solution like the ultrasonic vibrating screen is essential for efficient and precise classification.
How the Ultrasonic Vibrating Screen Enhances Sodium Feldspar Classification?
The ultrasonic vibrating screen integrates high-frequency ultrasonic technology with conventional vibrating screen mechanisms, providing superior separation efficiency and reducing common screening issues. Here’s how it enhances sodium feldspar classification:
1. High-Precision Sieving
Ultrasonic vibrations create micro-vibrations on the screen surface, enabling more accurate and refined particle classification. This ensures that sodium feldspar particles meet the required size distribution with minimal deviation.
2. Prevents Mesh Clogging
One of the biggest challenges in fine particle screening is mesh blockage, which reduces efficiency and increases downtime. The ultrasonic system continuously clears the mesh openings, preventing material accumulation and allowing for uninterrupted screening.
3. Increased Screening Efficiency
Compared to traditional vibrating screens, the ultrasonic vibrating screen can process finer materials at higher throughput rates. This is crucial for industries requiring large-scale feldspar processing without compromising accuracy.
4. Gentle Screening for Delicate Particles
Unlike aggressive mechanical screening methods, the ultrasonic vibrations provide a gentle, non-destructive screening process, maintaining the structural integrity of sodium feldspar particles. This results in a more consistent and high-quality final product.
5. Energy-Efficient and Cost-Effective
By reducing material waste, minimizing downtime due to clogging, and improving screening accuracy, the ultrasonic vibrating screen lowers overall operational costs while maintaining high productivity.