In modern industrial processing, the need for precise material classification continues to grow across various sectors. Among them, the filtration and separation of granular substances such as activated carbon require high-performance screening equipment capable of delivering both accuracy and efficiency. The rotary vibrating screen, known for its precision and flexibility, stands out as an essential machine in the field of fine material separation. In particular, its role in the classification of activated carbon particles demonstrates its superiority.
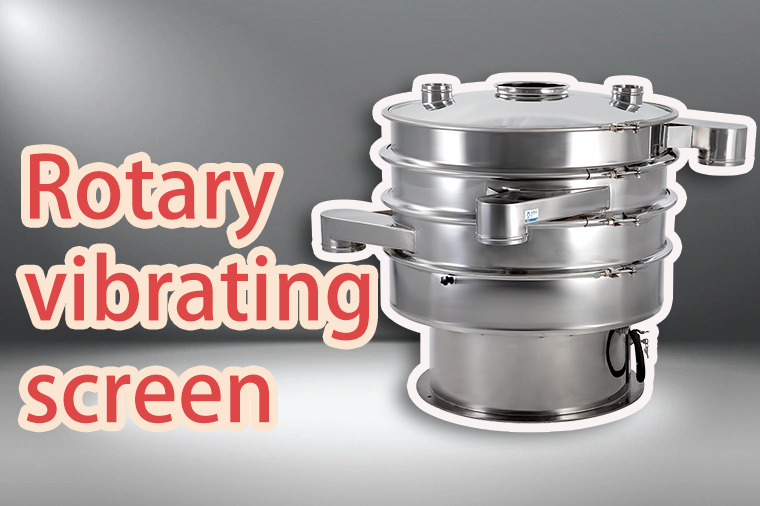
Rotary vibrating screens operate through high-frequency vibration generated by vertically mounted motor systems. These vibrations are transmitted in three dimensions, enabling the material to move in a spiral pattern over the screen surface. The result is a rapid and thorough separation of particles according to size. For activated carbon, which is widely used in water purification, air filtration, and chemical production, particle uniformity is critical to ensuring effective performance. The rotary vibrating screen allows for classification of carbon into specific mesh ranges such as 8x30, 12x40, and 20x50, helping manufacturers meet stringent product specifications.
One of the core advantages of the rotary vibrating screen is its customizable configuration. The machine can be equipped with 1 to 5 screen layers, allowing users to classify material into multiple grades simultaneously. The quick-release design makes it easy to change screen mesh, clean components, and reduce downtime—an essential factor for industries operating under high throughput demands.
Another significant benefit is its dust-tight operation. The fully enclosed structure of the rotary vibrating screen prevents contamination and dust leakage, making it ideal for environmentally sensitive applications. Combined with its quiet operation and low energy consumption, the screen meets the rigorous standards of modern industrial processing.
Regarding capacity, the rotary vibrating screen offers impressive production efficiency. Depending on the screen diameter (typically 600mm to 1500mm) and the number of layers used, the unit can process between 100 kg/h and 3,000 kg/h of material. For example, a 1200mm diameter screen operating with three mesh layers can process around 1 to 1.5 tons of activated carbon particles per hour. This level of productivity ensures continuous operation with minimal manual intervention.
Moreover, the screen's vibratory action prevents clogging and ensures consistent flow of material. Activated carbon is naturally porous and can generate dust that complicates the screening process. However, with adjustable vibration intensity and customizable mesh sizes, the rotary vibrating screen can maintain optimal separation even for fine or irregularly shaped particles.
The construction quality of the machine is another point worth highlighting. Made of food-grade stainless steel (304 or 316L), the screen is durable, rust-resistant, and suitable for use in high-hygiene environments. Its robust design ensures a long service life with minimal maintenance costs.
In summary, the rotary vibrating screen is the equipment of choice for screening activated carbon due to its efficiency, flexibility, and precision. Its ability to deliver consistent particle grading, ease of maintenance, and high output makes it indispensable in industries where material purity and throughput are crucial.