In industries such as electronics, photovoltaics, and high-performance ceramics, silicon-based materials are essential components. These materials—ranging from silicon carbide to silicon dioxide—require strict particle control to achieve desired performance in end applications. However, silicon powders are notoriously difficult to screen due to their fine particle size, tendency to agglomerate, and sensitivity to static electricity. The ultrasonic vibrating screen, integrating high-frequency ultrasonic energy with conventional vibratory motion, has emerged as a transformative solution for such challenges.
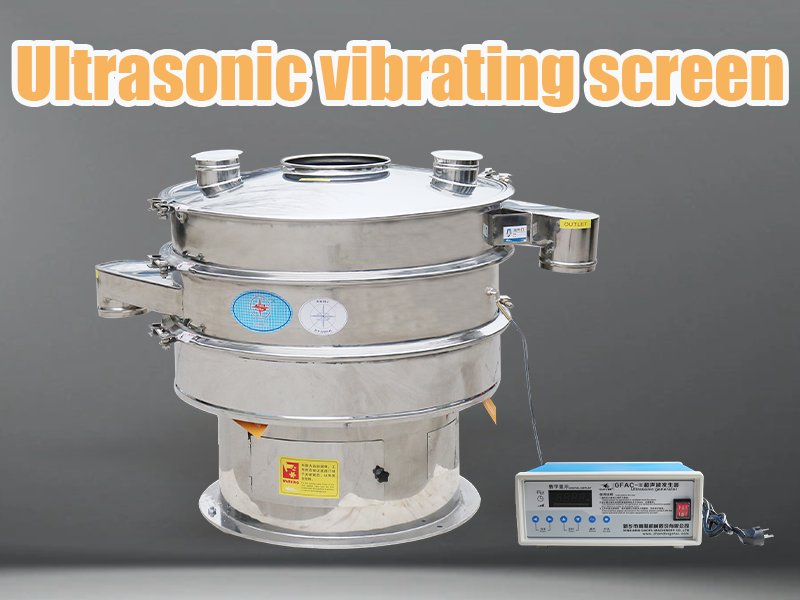
Unlike traditional vibratory screens, ultrasonic vibrating screens utilize a 36–40 kHz ultrasonic frequency generator that transmits vibration directly to the screen mesh via a converter. This added frequency breaks up surface tension, disperses agglomerated particles, and significantly improves the efficiency of ultra-fine powder screening. For silicon materials with particle sizes below 100 microns, the ultrasonic function ensures precise separation without blinding or clogging the mesh.
One of the most valuable features of the ultrasonic vibrating screen is its ability to process ultra-fine materials on mesh sizes as small as 500 mesh (25 microns) while maintaining high throughput. Conventional vibrating screens struggle with materials below 200 mesh due to clogging and poor flowability, but ultrasonic waves prevent these issues by enhancing powder fluidity and reducing static charges.
Silicon powders are typically used in high-purity applications where product consistency is paramount. Ultrasonic vibrating screens are particularly effective in classifying materials such as:
- Silicon dioxide (SiO2) for semiconductor manufacturing
- Silicon carbide (SiC) for abrasives and high-temperature ceramics
- Silicon nitride (Si3N4) for engineering components
For these materials, the ultrasonic vibrating screen provides separation accuracy of up to 95%, helping manufacturers achieve product quality that meets or exceeds industry standards.
In terms of output, the ultrasonic vibrating screen offers flexible throughput depending on mesh size, material properties, and machine diameter. A typical 1000mm diameter screen with a 200–325 mesh silicon dioxide powder can process 300 to 800 kg/h. For finer materials like 400 mesh silicon nitride, the output may range from 200 to 500 kg/h. Despite the reduced volume at finer mesh sizes, the improved separation quality and reduced waste result in overall cost savings and product consistency.
Additional advantages of the ultrasonic vibrating screen include:
- Minimal mesh wear due to reduced mechanical stress
- Long service life of screen components
- Fully enclosed structure preventing contamination and dust emission
- Easy integration with dust collection and automated material handling systems
From an operational standpoint, the system is user-friendly and low maintenance. Most models feature touch-screen controls and adjustable amplitude settings, allowing operators to tailor vibration intensity according to material characteristics. Moreover, the ultrasonic transducer and generator are modular, enabling quick replacement in case of malfunction.
To conclude, the ultrasonic vibrating screen is an essential tool for sieving silicon-based materials. It provides high screening precision, eliminates mesh blinding, and delivers consistent throughput, all while preserving the physical integrity of ultra-fine powders. As industries continue to demand finer and purer materials, the ultrasonic vibrating screen will play a central role in quality control and process optimization.