Pearl powder, a highly valued material in the cosmetics, health supplement, and pharmaceutical industries, is known for its fine texture and purity. However, achieving the desired level of purity in pearl powder can be challenging due to the presence of impurities such as shell fragments, dust, and other contaminants. Gaofu airflow vibrating sieve can improving the impurity removal rate of pearl powder, ensuring a high-quality end product.
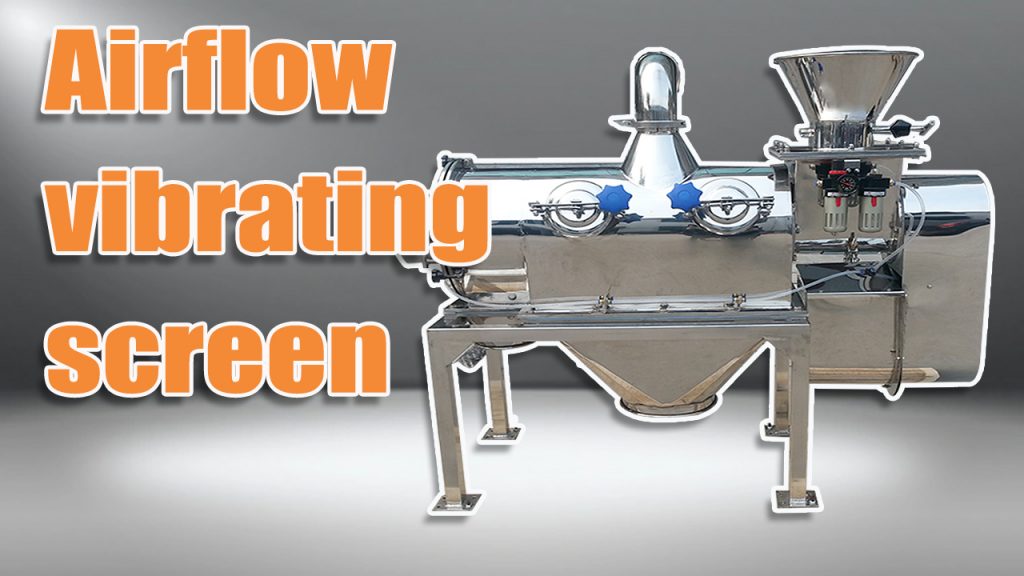
Challenges in Pearl Powder Processing
Pearl powder is derived from grinding pearls into a fine powder, but the process often introduces impurities such as:
- Shell fragments from the grinding process.
- Dust and foreign particles from the environment.
- Agglomerates or unevenly ground particles.
Traditional screening methods, such as mechanical vibrating screens, may struggle to remove these impurities effectively, especially when dealing with fine powders. This is where the airflow vibrating sieve excels, offering a more efficient and precise solution.
How the Airflow Vibrating Sieve Works
The airflow vibrating sieve combines mechanical vibration and airflow separation to achieve superior screening performance. Here’s how it improves the impurity removal rate of pearl powder:
- Mechanical Vibration for Even Distribution
- The sieve is equipped with a vibrating motor that generates a three-dimensional motion, ensuring that the pearl powder is evenly distributed across the screen surface.
- This vibration helps to break up agglomerates and ensures that all particles come into contact with the screen mesh, improving the chances of impurity removal.
- Airflow Separation for Fine Particle Handling
- A built-in fan or blower generates controlled airflow that passes through the screen mesh from below.
- The airflow lifts and separates fine particles of pearl powder, allowing them to pass through the mesh while carrying away lightweight impurities such as dust and shell fragments.
- The airflow also helps to dry the powder, reducing moisture content and preventing clumping.
- Precision Screening for Impurity Removal
- The combination of vibration and airflow ensures that particles are screened according to their size and weight.
- Larger impurities, such as shell fragments, are retained on the screen, while fine pearl powder passes through.
- Lightweight impurities are carried away by the airflow, resulting in a cleaner and purer product.
- Self-Cleaning Mechanism
- The airflow prevents the screen mesh from clogging, ensuring continuous operation and maintaining screening efficiency.
- This self-cleaning feature reduces downtime and minimizes the need for manual intervention.
Advantages of the Airflow Vibrating Sieve for Pearl Powder
- Higher Impurity Removal Rate
The airflow vibrating sieve effectively removes impurities such as shell fragments, dust, and agglomerates, resulting in a purer pearl powder.
2. Improved Screening Efficiency
The dual mechanism of vibration and airflow ensures that even the finest particles are screened accurately, improving overall efficiency.
3. Gentle Handling of Pearl Powder
The airflow vibrating sieve gently handles the delicate pearl powder, preventing damage or degradation of the material.
4. Hygienic and Easy to Clean
The sieve is constructed from food-grade stainless steel, making it easy to clean and suitable for use in industries with strict hygiene requirements.
5. Energy Efficiency
The machine is designed to consume minimal energy while delivering high performance, making it a cost-effective solution.
Applications in Pearl Powder Processing
The airflow vibrating sieve is particularly well-suited for processing pearl powder in the following industries:
- Cosmetics: Ensuring the purity of pearl powder used in skincare products.
- Health Supplements: Removing impurities to meet quality standards for dietary supplements.
- Pharmaceuticals: Refining pearl powder for use in medicinal formulations.
Case Study: Improving Pearl Powder Quality
A cosmetics manufacturer was struggling to achieve the desired purity level in their pearl powder using traditional screening methods. After switching to an airflow vibrating sieve, they observed:
- A 30% increase in impurity removal rate.
- A significant reduction in production downtime due to the self-cleaning mechanism.
- Improved consistency and quality of the final product.