Refractory materials play a crucial role in industries such as metallurgy, cement, glass, and ceramics, where high-temperature resistance is essential. The production of these materials involves several processes, including crushing, grinding, screening, and classification. One of the most effective ways to improve efficiency and increase output in refractory material production is by utilizing the SZF1020 linear vibrating screen. This advanced screening equipment provides precise separation, high throughput, and reliable performance, making it an ideal choice for refractory manufacturers looking to enhance production capacity.
Understanding the SZF1020 Linear Vibrating Screen
The SZF1020 linear vibrating screen is a high-performance screening machine designed for efficient material separation. It features a rectangular screening surface, dual vibration motors, and a multi-layer deck configuration. The screen operates by generating linear motion, which helps transport and classify materials according to particle size.
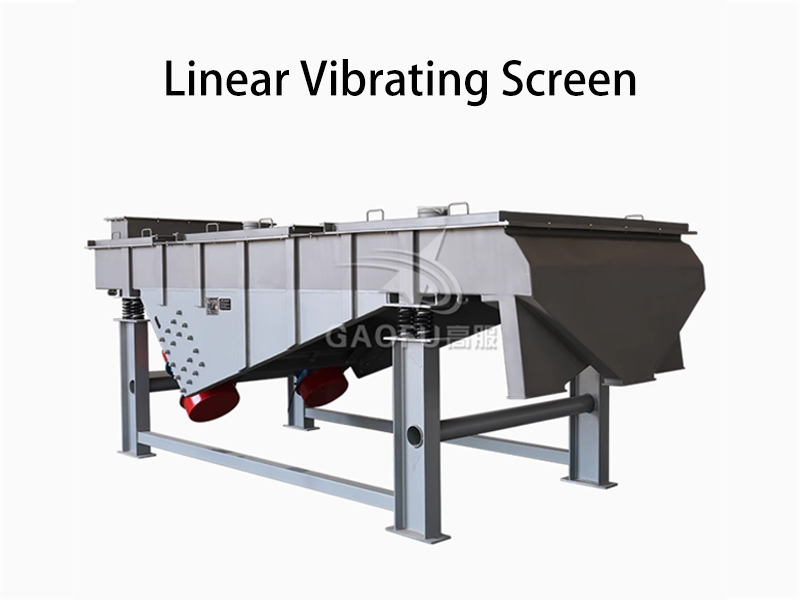
Understanding the SZF1020 Linear Vibrating Screen
The SZF1020 linear vibrating screen is a high-performance screening machine designed for efficient material separation. It features a rectangular screening surface, dual vibration motors, and a multi-layer deck configuration. The screen operates by generating linear motion, which helps transport and classify materials according to particle size.
Key Specifications of SZF1020 Linear Vibrating Screen
- Model: SZF1020
- Screen Surface Size: 1000mm × 2000mm
- Vibration Motors: Dual-motor drive for balanced and stable operation
- Screen Decks: Multi-layer configurations for efficient classification
- Screen Mesh Material: Stainless steel or polyurethane for durability
- Amplitude and Frequency: Adjustable for optimal performance based on material characteristics
How the SZF1020 Linear Vibrating Screen Enhances Refractory Material Production
Refractory materials consist of various raw materials such as alumina, silica, magnesia, and other heat-resistant compounds. The screening process is essential to ensure uniform particle size distribution, remove impurities, and optimize material quality. The SZF1020 linear vibrating screen offers several benefits that directly contribute to increased production efficiency.
- High Screening Efficiency for Better Material Quality
The SZF1020 linear vibrating screen uses a dual-vibration motor system, ensuring consistent and precise material movement across the screen surface. This uniform vibration improves material stratification and separation, leading to:
- Better particle size control, ensuring uniform refractory batches.
- Effective removal of impurities, such as dust, oversize particles, and foreign contaminants.
- Higher material purity, resulting in improved refractory performance.
- Increased Production Capacity with Multi-Deck Configuration
The SZF1020 model supports multiple screen layers, allowing manufacturers to classify materials into different sizes simultaneously. This significantly increases processing speed and output without requiring additional screening machines.
- Multiple deck options enable simultaneous sorting of fine, medium, and coarse refractory particles.
- Higher throughput due to an optimized material flow and reduced screening bottlenecks.
- Adjustable Vibration Settings for Different Refractory Materials
Refractory production involves processing materials of varying densities and hardness levels. The adjustable amplitude and frequency settings of the SZF1020 linear vibrating screen make it adaptable to different material characteristics.
- Higher vibration amplitude for coarse and heavy materials such as crushed magnesite.
- Lower amplitude and higher frequency for fine powders like alumina and silica.
This flexibility ensures optimal screening efficiency across different refractory materials, enhancing overall production performance.
4. Energy-Efficient and Low Maintenance Design
The SZF1020 linear vibrating screen is designed for low energy consumption while maintaining high productivity. Key design features that contribute to its efficiency include:
- Direct drive system with two synchronized motors, reducing energy wastage.
- Minimal moving parts, leading to reduced wear and tear.
- Easy screen replacement with modular screen panels for quick maintenance.
By lowering operational costs and downtime, the SZF1020 helps refractory manufacturers achieve higher profitability.
- Improved Material Handling with Controlled Discharge
Unlike traditional screening methods, which may lead to uneven discharge, the SZF1020 linear vibrating screen ensures a controlled and steady material outflow. This feature is particularly beneficial for:
- Batch processing in refractory brick manufacturing.
- Continuous production lines where consistent material feed is critical.
- Minimizing waste and over-processing, leading to better resource utilization.
- Durability and Resistance to Harsh Operating Conditions
Refractory production environments involve handling abrasive and high-density materials that can wear down standard screening equipment. The SZF1020 linear vibrating screen is built to withstand these harsh conditions with:
- High-strength materials, such as stainless steel and reinforced frames.
- Wear-resistant screen mesh, available in metal or polyurethane for extended lifespan.
- Dust-proof design, reducing material loss and improving workplace safety.
Applications of SZF1020 Linear Vibrating Screen in Refractory Industry
The versatility of the SZF1020 makes it suitable for various refractory production processes, including:
- Raw material classification: Screening of alumina, silica, magnesite, and zircon.
- Crushed refractory recycling: Separating reusable particles from waste materials.
- Final product quality control: Ensuring uniform size distribution for bricks, castables, and ceramic products.
- Pre-processing before mixing: Sorting fine powders for binder preparation.