Sugar powder is a widely used ingredient in the food industry, requiring precise screening to achieve uniform particle size and eliminate impurities. Traditional vibrating screens often struggle with issues like mesh clogging, material agglomeration, and inefficient separation. The ultrasonic vibrating screen offers a superior solution by incorporating ultrasonic technology to enhance screening efficiency. This article explores how ultrasonic vibrating screens work, their advantages, and their applications in sugar powder screening and impurity removal.
How the Ultrasonic Vibrating Screen Works
The ultrasonic vibrating screen combines traditional vibration with high-frequency ultrasonic waves, which creates a more effective and precise screening process. The working mechanism consists of the following steps:
- High-Frequency Vibrations – The base vibrating screen generates regular vibrations to move sugar powder across the mesh surface.
- Ultrasonic Frequency Activation – A built-in ultrasonic transducer produces high-frequency sound waves (typically around 36,000 times per second), which break up agglomerated particles and prevent clogging.
- Efficient Separation – The combination of vibration and ultrasonic energy ensures that fine sugar powder passes through the mesh while impurities and oversized particles are efficiently removed.
- Continuous Operation – The screen maintains a self-cleaning function, preventing mesh blinding and ensuring a stable screening process.
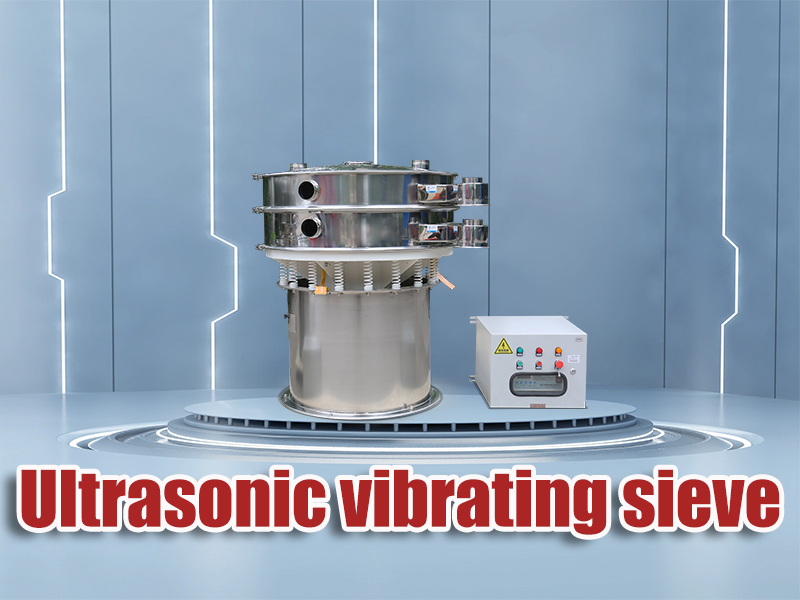
Key Advantages of the Ultrasonic Vibrating Screen for Sugar Powder
1. Superior Anti-Clogging Performance
One of the biggest challenges in sugar powder screening is mesh clogging due to fine particle adhesion. The ultrasonic waves keep the mesh screen clear, ensuring a consistent flow of material.
2. High Precision Screening
The ultrasonic vibrating screen enables ultra-fine separation, allowing only correctly sized sugar powder particles to pass through while removing oversized granules and contaminants.
3. Efficient Impurity Removal
During sugar processing, impurities such as lumps, fiber residues, and foreign particles must be eliminated. The ultrasonic vibration technology enhances impurity removal, improving the purity of the final product.
4. Increased Screening Capacity
By reducing mesh blockage and improving material fluidity, ultrasonic vibrating screens can handle higher throughput compared to conventional screens, making them ideal for large-scale sugar processing plants.
5. Gentle Screening for Heat-Sensitive Materials
Sugar powder is sensitive to heat and can melt or degrade if subjected to excessive friction. The ultrasonic vibrating screen reduces frictional resistance, ensuring gentle material handling and preserving product quality.
6. Energy Efficiency and Low Maintenance
Compared to traditional screening methods, ultrasonic vibrating screens require less energy while providing superior results. The self-cleaning function of the mesh reduces downtime and maintenance costs.
Applications of Ultrasonic Vibrating Screens in Sugar Powder Processing
Ultrasonic vibrating screens are widely used in the food and pharmaceutical industries, where fine powders must be processed with high precision and hygiene standards. Specific applications include:
- Powdered Sugar Production – Achieving uniform sugar particle size for baking and confectionery applications.
- Food Additives Processing – Ensuring that sugar-based additives are free of impurities before mixing with other ingredients.
- Pharmaceutical and Nutraceutical Industries – Screening sugar powder used in medicines and dietary supplements.
- Industrial Sugar Refining – Removing unwanted particles from bulk sugar powder production.