Silica powder is widely used in various industries, including electronics, construction, and pharmaceuticals, due to its unique physical and chemical properties. However, the presence of impurities in silica powder can significantly affect the quality and performance of the final product. To ensure high purity and consistent particle size distribution, an ultrasonic vibrating screen has become an essential tool for the sieving and impurity removal of silica powder.
Introduction to Silica Powder and Its Processing Challenges
Silica powder (SiO₂) is a finely ground material derived from quartz or other silica-rich sources. It is highly valued for its high hardness, thermal stability, and chemical resistance. These properties make it an important raw material in industries such as:
- Semiconductors and Electronics – Used as a key component in the production of microchips and circuit boards.
- Construction – Incorporated into concrete and other building materials to enhance strength and durability.
- Pharmaceuticals and Cosmetics – Used as an excipient and a texture-enhancing agent.
Despite its many applications, the production of high-quality silica powder comes with significant challenges. One of the major issues is the presence of impurities and irregular particle sizes. Contaminants such as dust, metal particles, and organic matter can compromise the purity and consistency of the silica powder, leading to defects in the final product. Therefore, effective sieving and impurity removal are critical to maintaining the quality of silica powder during production.
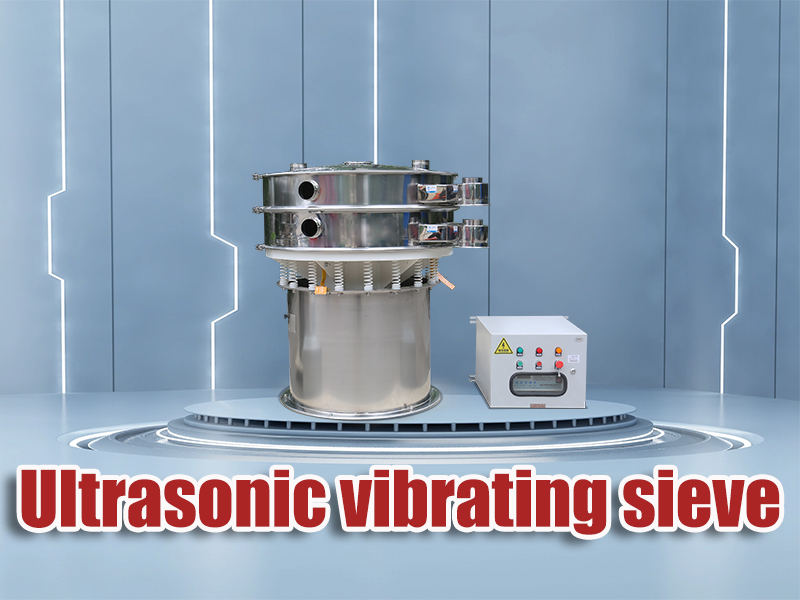
How Ultrasonic Vibrating Screens Work
An ultrasonic vibrating screen is an advanced screening solution that combines traditional vibrating screen technology with high-frequency ultrasonic waves. It consists of a standard vibrating screen frame equipped with an ultrasonic transducer. The working process involves the following steps:
- High-Frequency Vibration – The vibrating screen generates a mechanical vibration at a certain frequency, which causes the silica powder to move across the screen surface.
- Ultrasonic Wave Application – The ultrasonic transducer converts electrical energy into high-frequency sound waves (typically 20–40 kHz). These ultrasonic vibrations are superimposed on the base mechanical vibration, creating a micro-vibration effect on the surface of the screen mesh.
- Enhanced Sieving Efficiency – The ultrasonic waves prevent the silica particles from sticking to the mesh or clogging the screen holes by reducing friction and static electricity.
- Precision Separation – The combination of mechanical and ultrasonic vibrations allows even the finest silica particles to pass through the mesh while impurities and oversized particles are separated and discharged.
Advantages of Using Ultrasonic Vibrating Screens for Silica Powder
Ultrasonic vibrating screens offer several key advantages when it comes to processing silica powder:
1. High Precision and Efficiency
The ultrasonic vibration reduces screen clogging and increases the throughput rate, enabling finer particles to pass through the mesh while maintaining accuracy in particle size distribution.
2. Effective Impurity Removal
Impurities such as metal particles, dust, and organic contaminants are effectively separated from the silica powder due to the combined action of mechanical and ultrasonic vibrations.
3. Prevention of Mesh Blinding
Traditional vibrating screens often face issues with mesh blinding, where fine particles clog the screen holes, reducing efficiency. The ultrasonic vibration prevents blinding by breaking up agglomerates and reducing adhesion between particles.
4. Increased Production Yield
By enhancing the sieving process, the ultrasonic vibrating screen increases the recovery rate of usable silica powder, reducing material waste and improving overall production efficiency.
5. Versatility in Application
Ultrasonic vibrating screens can be adapted for different mesh sizes and materials, making them suitable for handling a wide range of silica powder grades and production requirements.
Application of Ultrasonic Vibrating Screens in Silica Powder Processing
Ultrasonic vibrating screens have found widespread use in industries where silica powder quality is critical:
- Semiconductor Manufacturing – Ensures that silica powder used in chip production meets strict purity and size requirements.
- Glass and Ceramics – Provides consistent particle size distribution for improved material performance.
- Chemical Industry – Used for the precise separation of silica powder in the production of high-purity chemicals.
- Pharmaceutical and Cosmetic Industry – Ensures that silica powder used as an excipient meets stringent quality and purity standards.