In industries that rely on ultra-fine materials—such as electronics, glass manufacturing, semiconductors, pharmaceuticals, and precision ceramics—the purity and consistency of silicon dioxide (SiO₂) powder, commonly referred to as silica powder, are essential. However, due to its ultra-fine particle size and often cohesive nature, silica powder poses significant challenges during the screening and classification process. Conventional vibrating screens frequently suffer from mesh clogging and reduced efficiency when handling such fine materials. To overcome these limitations, more and more manufacturers are turning to ultrasonic vibrating screen, which offer a highly effective solution for precise, clog-free, high-throughput screening of silica powder.
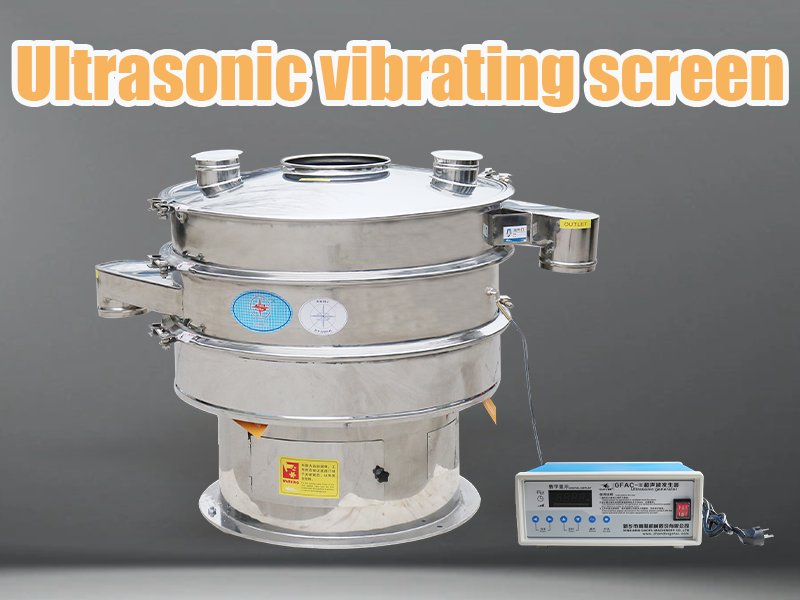
Superior Screening for Ultra-Fine Powders
Ultrasonic vibrating screens are specially designed to screen ultra-fine, light, or sticky powders by applying high-frequency ultrasonic vibrations to the screen mesh. These micro-vibrations prevent particles from sticking or clogging the mesh, ensuring continuous and efficient separation.
When applied to silica powder, ultrasonic vibrating screens provide several significant benefits:
- Increased Purity Through Effective Deblinding and Impurity Removal
The ultrasonic system enables efficient separation of unwanted particles and contaminants, which helps improve the overall purity of silica powder. This is especially critical in high-tech applications where even trace impurities can compromise product performance. - No Mesh Clogging
One of the standout features of ultrasonic screens is their ability to eliminate mesh blinding, a common problem with traditional screening methods when handling very fine powders. This not only ensures smoother operation but also significantly reduces downtime and maintenance costs. - Double the Throughput
Thanks to the uninterrupted flow of material and more efficient screen usage, ultrasonic vibrating screens can increase production capacity by up to 2 times compared to standard vibrating screens. This improved efficiency directly benefits operational productivity and profitability. - Ideal for Ultra-Fine Powder Applications
Silica powder often exists in micrometer or even sub-micron ranges, making it difficult to screen using traditional equipment. The ultrasonic system excels in handling ultra-fine materials, making it the ideal solution for companies seeking precision and consistency at microscopic scales. - Stable Performance and Low Noise
Despite the high-frequency vibrations involved, the equipment operates with minimal noise, creating a safer and more comfortable working environment. The robust design also ensures long service life and consistent performance.
Tailored for Precision Manufacturing
Ultrasonic vibrating screens can be customized with various mesh sizes and screen layers, depending on the particle size requirements and production volume. Whether used in a single-layer system for basic impurity removal or a multi-layer setup for fine particle classification, the machine can be adapted to meet a wide range of processing needs in silica powder production.