In the construction and aggregate industry, the efficient handling and classification of raw stone materials is crucial for ensuring product quality, reducing downtime, and optimizing plant throughput. One machine that has proven its value time and again in these heavy-duty operations is the bar vibrating screen, also known as the grizzly screen or grizzly feeder. Designed to screen bulky, blocky, or heavily contaminated materials, this equipment is built for ruggedness and high capacity.
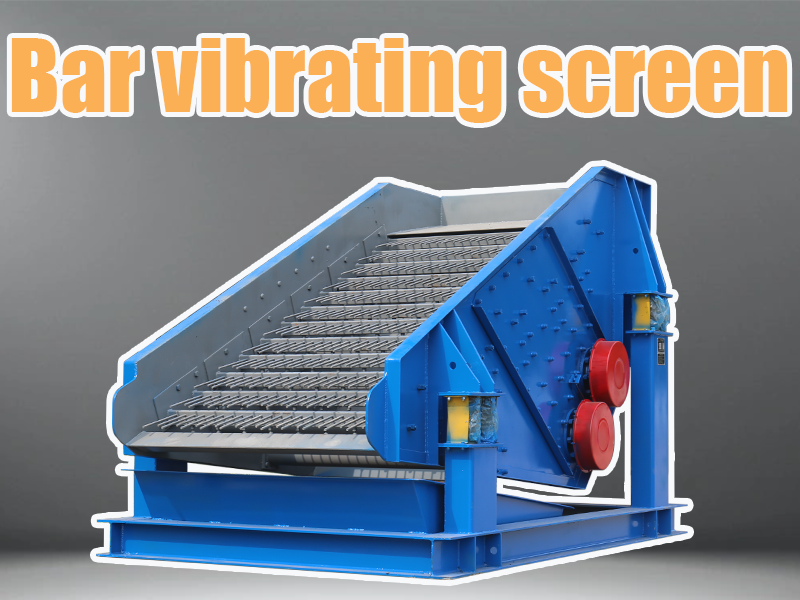
This article provides a comprehensive overview of the bar vibrating screen’s performance when screening construction stone, such as limestone, granite, basalt, and sandstone. We’ll explore the machine’s advantages, structural design, output capacity, and its unique role in primary screening applications.
- What is a Bar Vibrating Screen?
Unlike traditional wire mesh or perforated plate screens, the bar vibrating screen features parallel steel bars (grizzly bars) set at specific gaps. As material is fed onto the screen, finer particles fall between the bars while larger blocks remain on top and move down the incline via vibration.
Common design characteristics include:
- Robust steel bar decks, often manganese steel or wear-resistant alloy
- Adjustable gap between bars (typically 50–150 mm)
- Linear or elliptical vibration motion generated by a vibrating motor or exciter
- Inclined installation (15–25°) for gravity-assisted material movement
- Application of Bar Screens in Construction Stone Processing
In stone processing plants, especially those dealing with blasted rock from quarries, the bar vibrating screen is often installed at the very front of the production line, just after the feeder or dump hopper. Its main purposes are:
- To remove fine soil, clay, or undersized materials (typically <80 mm) from the raw feed
- To protect downstream crushers (such as jaw or cone crushers) from overloading
- To improve crusher efficiency and product shape by allowing only the right size of raw stone to enter
- Advantages of Bar Vibrating Screen for Stone Screening
A. Exceptional Durability and Wear Resistance
Built to handle heavy shock loads and abrasive materials, bar vibrating screens are made from hardened steel or high-manganese alloy. Unlike mesh screens, which often suffer from tearing or blockage, bar screens provide extended service life even under constant impact from large stones or wet clay-laden aggregates.
B. No Mesh Clogging
One of the standout benefits is its resistance to clogging. In environments where sticky or moist materials would clog traditional mesh screens, the wide spacing and self-cleaning motion of the bar screen ensures consistent performance. This makes it ideal for rainy conditions or for use in mobile crushing stations.
C. High Capacity for Coarse Separation
Bar screens can handle massive volumes of material. For example, a typical 1500 mm × 4000 mm unit can process up to 500–800 tons per hour, depending on the gap between bars and feed material properties. In large-scale quarry operations, double-deck or tandem systems may handle 1000+ tons/hour.
D. Simple Maintenance
The absence of fine mesh means less maintenance. Bar spacing is adjustable, and worn bars can be individually replaced without disassembling the entire deck. Additionally, the open design makes inspections and cleaning faster and easier.
E. Protection for Downstream Equipment
By removing fines early and ensuring only properly sized material reaches the crusher, the bar vibrating screen significantly reduces wear on secondary equipment. This extends the service life of expensive crushers and lowers maintenance costs.
- Output and Performance Metrics
Depending on size and configuration, production metrics of bar vibrating screens screening construction stone are as follows:
- Feed size capacity: Up to 1000 mm for large boulders
- Output rate: 300 to 1000 tons/hour
- Typical cut point: 50 mm to 120 mm
- Screening efficiency: ~85% for primary rough separation
- Energy consumption: 5.5–15 kW per motor, with dual motors in large machines
- Use Case: Granite Quarry in Fujian Province
A granite quarry in southern China installed a 2000 mm × 6000 mm bar vibrating screen upstream of a primary jaw crusher. Results after 6 months of operation included:
- Daily throughput: 5000–6000 tons
- Reduction in jaw crusher maintenance downtime by 35%
- Extended life of crusher jaws by 25%
- Improved gradation control of finished aggregates
- Reduced load on conveyor belts by 20% due to pre-screening
- Conclusion
The bar vibrating screen is an indispensable piece of equipment in the aggregate and quarrying industries. With its ability to resist clogging, handle oversized material, and ensure long-term durability, it plays a critical role in ensuring efficient plant operation. Whether used in fixed installations or mobile setups, its contribution to improved material flow and equipment longevity is undeniable.