In modern industrial manufacturing, particularly in plastics, chemicals, and advanced materials, the precise handling and separation of fine powders is critical to ensuring product quality and operational efficiency. Resin powder, widely used in injection molding, coatings, and composite materials, demands a screening solution that can meet high standards of purity, particle size consistency, and operational reliability. The rotary vibrating screen is engineered precisely for this challenge, offering unmatched performance in fine screening, impurity removal, and continuous production.
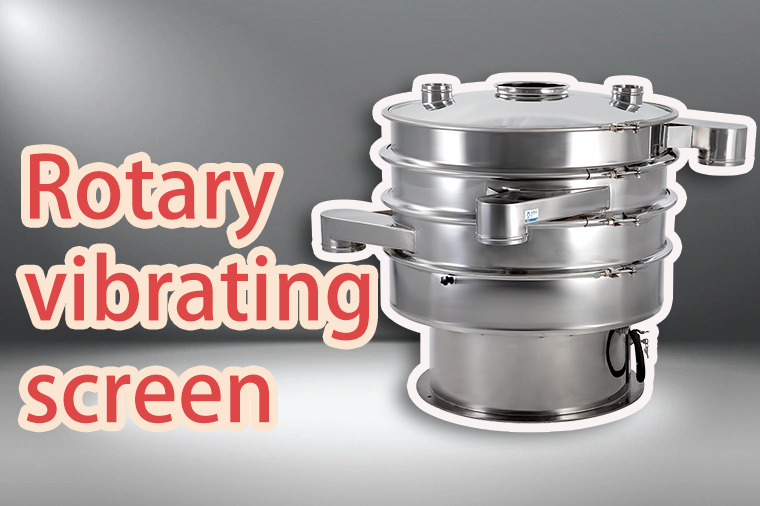
Exceptional Screening Precision for Fine Resin Powder
Resin powders often have fine particle sizes and low bulk density, making them difficult to screen using conventional equipment. The rotary vibrating screen, however, is capable of delivering high-precision screening down to 600 mesh (approximately 0.02 mm). This allows for the accurate classification of resin powders by size, ensuring that only particles within the desired range pass through while oversized or undersized particles are efficiently removed.
Whether for thermosetting resins, epoxy powders, or other high-grade plastics, this level of screening precision is essential for achieving uniform flow characteristics and consistent product performance in downstream processing.
High-Standard Impurity Removal
In industries that demand high material purity, such as electronics, automotive, and aerospace, even trace contaminants can compromise product integrity. The rotary vibrating screen excels at removing impurities from resin powder with high precision, thanks to its multi-layer screening design and high-frequency vibration. Foreign matter such as fibers, lumps, or dust is effectively separated from the main product stream, helping manufacturers meet stringent quality control standards.
Micro-Filtration Down to 5 Microns
Beyond traditional screening, the rotary vibrating screen also functions as a fine filtration system. It can filter particles as small as 5 microns, making it ideal for applications requiring ultra-fine separation. This capability ensures the highest levels of material purity, reducing the risk of contamination and improving the performance of high-end resin applications.
Designed for Continuous Operation
Industrial-scale production environments require equipment that can operate continuously without frequent stoppages. The rotary vibrating screen is built for 24/7 operation, with durable construction, optimized vibration mechanics, and automated material discharge. This ensures a steady throughput of resin powder, maximizing production efficiency while minimizing downtime.
Quick and Easy Screen Replacement
In addition to its operational capabilities, the rotary vibrating screen is designed with user convenience in mind. One of its standout features is its quick screen replacement mechanism, which allows operators to change the mesh screen in as little as 3 to 5 minutes. This reduces maintenance time significantly and enables fast adaptation to different screening requirements, improving flexibility in multi-batch or multi-product processing lines.