In the plastics manufacturing and recycling industries, achieving consistent particle size and quality is essential for producing high-performance products. Whether it’s raw plastic pellets, recycled materials, or finished plastic components, precise grading and screening are critical steps in the production process. The Rotary Vibrating Screen has emerged as a powerful and versatile tool for efficiently separating and classifying plastic particles, ensuring optimal quality and performance.
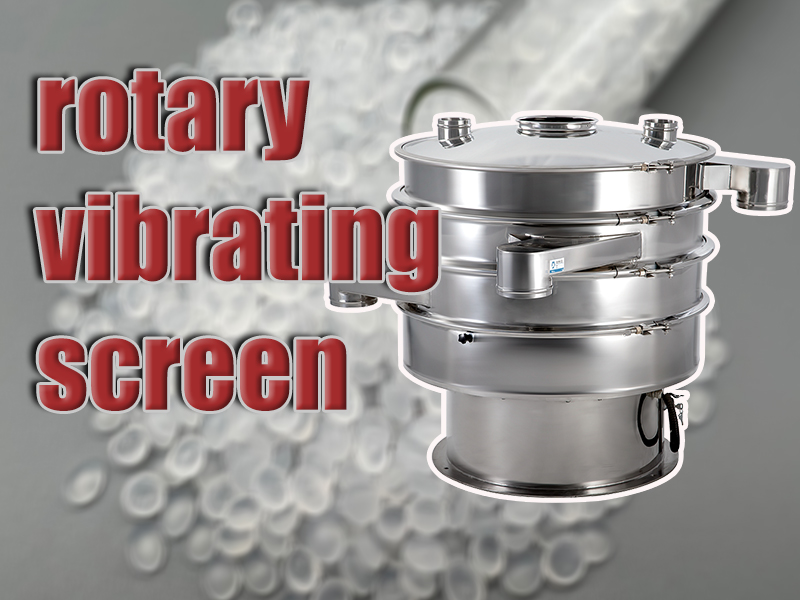
The Importance of Grading and Screening in the Plastics Industry
Plastic particles come in various shapes, sizes, and forms, depending on their application. Grading and screening are essential for:
Quality Control: Ensuring uniformity in particle size for consistent product performance.
Recycling Efficiency: Separating contaminants and oversized particles from recycled plastics.
Process Optimization: Improving flowability, melting, and molding characteristics of plastic materials.
Product Differentiation: Sorting plastic particles for specific applications, such as injection molding, extrusion, or 3D printing.
Traditional screening methods often struggle with challenges like low efficiency, mesh clogging, and difficulty handling fine or irregularly shaped particles. The Rotary Vibrating Screen addresses these issues with its advanced design and high-performance capabilities.
What is a Rotary Vibrating Screen?
A Rotary Vibrating Screen is a highly efficient screening machine that uses vibrational motion and rotational force to separate and classify particles based on size. It is particularly well-suited for handling plastic particles, offering a combination of precision, durability, and versatility.
Key Features and Benefits
High Screening Efficiency:
The Rotary Vibrating Screen uses a combination of vibration and rotation to ensure thorough and accurate particle separation. This results in higher throughput and better grading accuracy compared to traditional screens.
Anti-Clogging Design:
The screen’s unique motion helps prevent mesh clogging, even when processing sticky or fine plastic particles. This reduces downtime and maintenance requirements, improving overall productivity.
Gentle Handling of Materials:
The Rotary Vibrating Screen is designed to handle delicate or irregularly shaped plastic particles without causing damage. This makes it ideal for applications involving recycled plastics or heat-sensitive materials.
Versatility:
The screen can be customized with different mesh sizes and screen layers to accommodate a wide range of particle sizes and materials. This flexibility makes it suitable for various stages of plastic production, from raw material processing to final product quality control.
Durability and Low Maintenance:
Constructed with high-quality materials, the Rotary Vibrating Screen is built to withstand the rigors of industrial use. Its robust design ensures long-lasting performance with minimal maintenance.
Compact and Space-Saving:
The screen’s compact design makes it easy to integrate into existing production lines, saving valuable floor space in manufacturing facilities.
Applications in the Plastics Industry
The Rotary Vibrating Screen is widely used in the plastics industry for:
Raw Material Screening: Grading plastic pellets and powders to ensure uniformity before processing.
Recycling Operations: Separating contaminants, oversized particles, and fines from recycled plastics.
Powder Coating: Screening plastic powders used in coating applications to achieve consistent particle size.
Additive Manufacturing: Sorting plastic particles for 3D printing filaments to ensure smooth extrusion and printing.
Quality Control: Inspecting finished plastic products for size consistency and defects.
Why Choose a Rotary Vibrating Screen?
The Rotary Vibrating Screen is a proven solution for the plastics industry, offering unmatched efficiency, reliability, and versatility. Its ability to handle a wide range of materials, from fine powders to coarse pellets, makes it an indispensable tool for manufacturers and recyclers alike.