Fluorite, also known as fluorspar, is a critical mineral used in metallurgy, hydrofluoric acid production, ceramics, and optical components. Its processing involves crushing, grinding, and classification stages, where efficient pre-screening can significantly improve recovery rates and equipment protection. For coarse separation of lump fluorite ore, the bar vibrating screen offers an ideal solution, delivering robust performance in high-load and dusty environments.
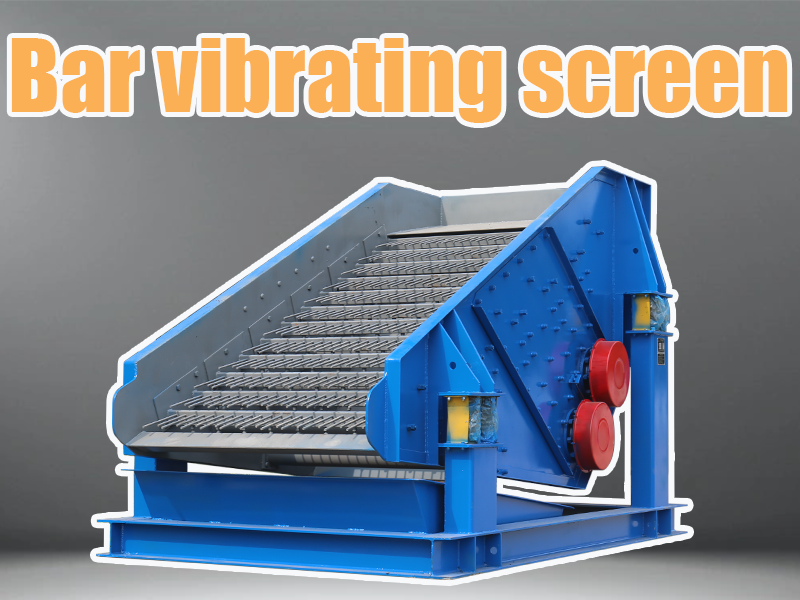
- Screening Requirements in Fluorite Processing
Fluorite ore typically contains impurities like clay, gangue minerals, and fines that must be removed before flotation or smelting. Screening plays a key role in:
- Removing sub-ore fines and debris
- Classifying raw material into desired size fractions
- Reducing wear on crushers and mills
Lump fluorite (20–300 mm) is particularly well-suited for coarse screening on bar vibrating screens due to its density and brittleness.
- Working Principle and Design of the Bar Vibrating Screen
The bar vibrating screen consists of:
- Inclined steel deck with replaceable grizzly bars
- Dual eccentric motors or exciters generating linear motion
- Screen slope optimized for gravity-assisted movement
- Adjustable bar spacing for specific screening targets
- Advantages for Fluorite Screening
A. Rugged Design for Harsh Environments
Fluorite mining often occurs in abrasive, wet, and dusty conditions. The bar vibrating screen’s heavy-duty steel construction withstands such challenges, operating reliably without mesh blinding or frame deformation.
B. Efficient Removal of Undersized Material
Bar spacing between 50–100 mm enables separation of clay or fractured ore particles early in the process, enhancing flotation efficiency and reducing reagent consumption.
C. Large Handling Capacity
In high-output mining operations, a 2000 mm × 6000 mm bar screen can process 600–900 tons/hour of fluorite lump ore, significantly improving crushing circuit throughput.
D. Low Maintenance
Screens operate with minimal maintenance: vibration motors require periodic lubrication, and worn grizzly bars are replaced individually. Downtime is minimal compared to mesh-type screens.
E. Environmental and Operational Control
- Reduced airborne dust due to open structure and optional water sprays
- Low noise operation (<75 dB)
- Easy integration with feeder hoppers or belt conveyors
- Case Example: Fluorite Mine in Hunan Province
A mine producing metallurgical-grade fluorite integrated a double-deck bar vibrating screen ahead of its cone crusher. Key results:
- Processed up to 720 tons/hour of raw ore
- Eliminated crusher blockages from clay-rich feed
- Improved concentrate grade by 14% due to cleaner feed
- Extended crusher liner life by 30%
- Future Potential and Upgrades
As fluorite prices rise and processing plants aim for greener operations, the bar vibrating screen continues to evolve. Current developments include:
- Hydraulic screen deck lifting for maintenance
- Modular grizzly bar replacement
- Smart vibration sensors for predictive maintenance
- Conclusion
In fluorite processing, pre-screening is more than a preparatory step—it is a critical factor that shapes overall efficiency and profitability. The bar vibrating screen meets the unique challenges of fluorite mining with strength, adaptability, and consistent output.
With high capacity, long service life, and the ability to withstand harsh mining conditions, the bar vibrating screen is an indispensable solution for screening fluorite and other hard, blocky ores.