In modern industrial processing, the sieving of fine powders like citric acid presents unique challenges that demand specialized equipment. The tumbler vibrating screen has emerged as a revolutionary solution, combining high-efficiency separation with gentle material handling. This advanced screening technology is particularly valuable in food, pharmaceutical, and chemical industries where product purity and particle integrity are paramount.
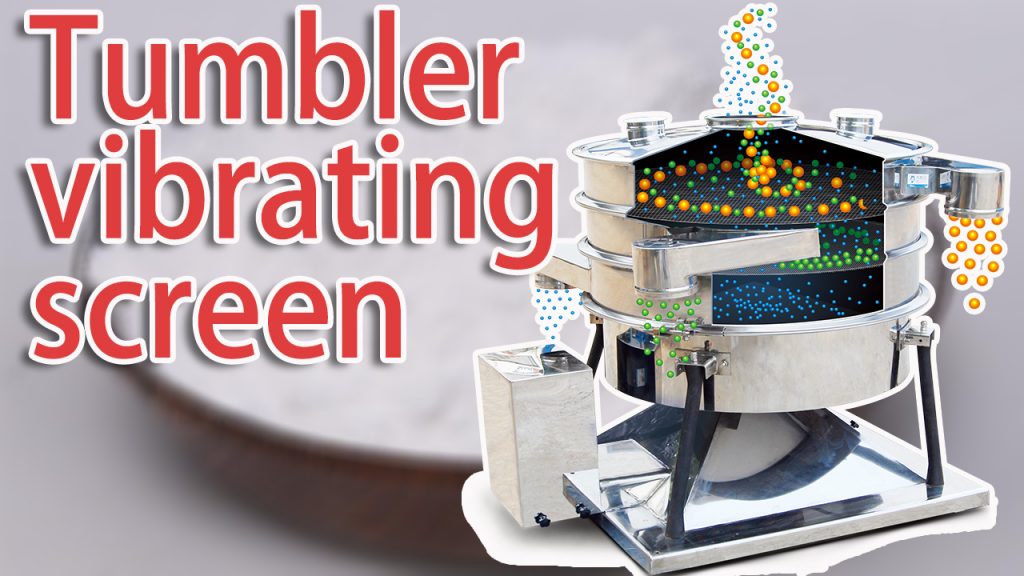
The Challenge of Citric Acid Powder Processing
Citric acid powder, with its delicate crystalline structure and tendency to generate static charges, requires careful handling during sieving operations. Traditional vibrating screens often struggle with several critical issues:
- Material degradation: Aggressive vibration patterns can fracture delicate crystals
- Screen blinding: Fine particles tend to clog mesh openings
- Inconsistent grading: Improper motion leads to uneven particle distribution
- Low throughput: Conventional designs limit processing capacity
These challenges directly impact production efficiency, product quality, and operational costs, making the selection of proper sieving equipment crucial.
Tumbler Vibrating Screen: Technological Advantages
The tumbler vibrating screen addresses these challenges through its unique three-dimensional elliptical motion that simulates natural manual sieving action. This innovative design offers multiple advantages for citric acid powder processing:
- Gentle yet Effective Motion Principle
The screen's low-frequency (typically 50-300 RPM), high-precision tumbling action creates an optimal balance between sieving efficiency and material protection. This motion:
- Minimizes mechanical stress on fragile crystals
- Reduces particle-to-particle friction
- Prevents excessive impact that could damage product integrity
- Flexible Multi-Layer Configuration
Unlike conventional single-layer screens, the tumbler vibrating screen supports:
- Simultaneous multi-grade separation (up to 5 layers)
- Customizable screen deck arrangements
- Independent control of each screening level
This flexibility allows processors to achieve precise particle classification in a single operation.
- Superior Impurity Removal Capability
The screen's unique motion pattern enhances separation efficiency by:
- Promoting better material stratification
- Preventing particle agglomeration
- Maintaining consistent mesh openness
- Facilitating continuous self-cleaning of screen surfaces
Performance Benefits for Citric Acid Processing
When applied to citric acid powder sieving, the tumbler vibrating screen delivers measurable improvements:
- Product Quality Enhancement
- 98.5%+ purity levels achievable
- Less than 0.3% product degradation
- Consistent particle size distribution (PSD)
- Operational Efficiency Gains
- 40-60% higher throughput than conventional screens
- 30% reduction in energy consumption
- Up to 80% reduction in screen blinding incidents
- Economic Advantages
- Lower maintenance requirements
- Extended screen mesh lifespan
- Reduced product loss
- Higher overall equipment effectiveness (OEE)
Advanced Design Features
Modern tumbler vibrating screens incorporate several technological innovations:
- Precision Motion Control System
- Variable frequency drives for optimal speed adjustment
- Computer-balanced eccentric weights
- Vibration isolation mounts for stable operation
- Specialized Screen Frame Design
- Modular construction for easy maintenance
- Quick-release screen tensioning system
- Anti-static treatment for powder applications
- Smart Monitoring Capabilities
- Real-time vibration analysis
- Automatic imbalance detection
- Predictive maintenance alerts
Application Versatility
While exceptionally effective for citric acid powder, the tumbler vibrating screen demonstrates excellent performance with various challenging materials:
- Food Industry Applications
- Sugar and sweetener powders
- Baking ingredients
- Nutritional supplements
- Pharmaceutical Uses
- Active pharmaceutical ingredients (APIs)
- Excipient materials
- Vitamin powders
- Chemical Processing
- Specialty chemicals
- Catalysts
- Polymer powders