Lithium manganese oxide (LiMn₂O₄), commonly known as lithium manganate, is a critical material in the battery industry. It is widely used as a cathode material in lithium-ion batteries due to its high thermal stability, low cost, and environmental friendliness. However, the quality and performance of lithium manganate directly affect the efficiency and lifespan of the batteries in which it is used. Therefore, ensuring the purity and consistency of lithium manganate powder is essential for producing high-performance batteries. One of the most effective methods for sieving and removing impurities from lithium manganate is through the use of an Ultrasonic Vibrating Sieve.
Introduction to Lithium Manganate and Its Role in the Battery Industry
Lithium manganate (LiMn₂O₄) is a widely used cathode material in lithium-ion batteries, especially in electric vehicles (EVs), portable electronics, and energy storage systems (ESS). Its advantages include:
- High Safety and Thermal Stability – Compared to other cathode materials, lithium manganate is less prone to overheating and thermal runaway, making it safer for high-power applications.
- Cost-Effectiveness – The raw materials used for producing lithium manganate are more abundant and affordable compared to cobalt-based materials.
- Environmental Friendliness – Lithium manganate is considered more environmentally sustainable than other cathode materials due to its reduced reliance on rare and toxic metals.
However, the production of lithium manganate comes with challenges related to particle size distribution and impurity content. Impurities such as metal particles, dust, and agglomerates can compromise the electrochemical performance of the battery, reducing capacity, efficiency, and cycle life. Therefore, precise sieving and impurity removal during lithium manganate production are essential for maintaining the quality of the final product.
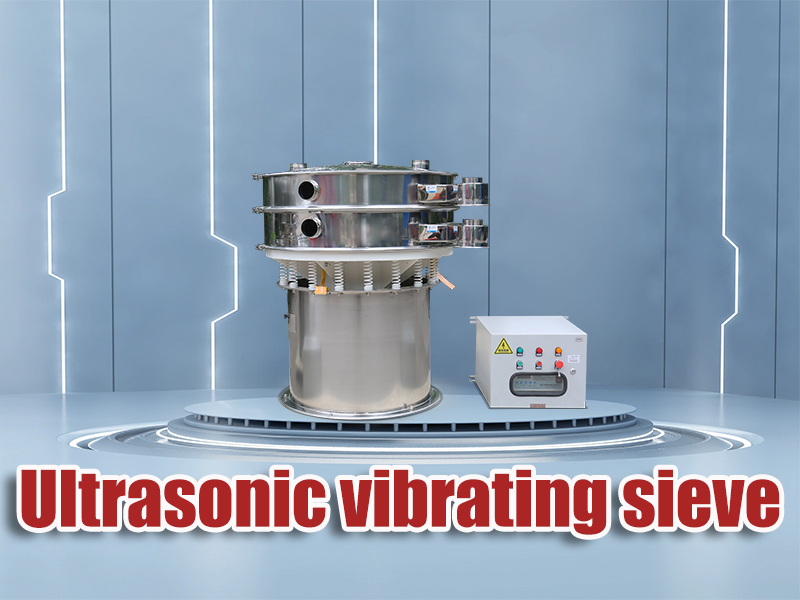
Challenges in Lithium Manganate Sieving and Purification
Lithium manganate is typically processed in powder form, where maintaining consistent particle size and purity is crucial for battery performance. The key challenges involved in lithium manganate processing include:
- Presence of Impurities
Metal contaminants, dust, and agglomerates can negatively affect the conductivity and electrochemical stability of the battery. - Agglomeration of Particles
Lithium manganate particles tend to clump together during production, making it difficult to achieve a uniform particle size distribution. - Mesh Blockage and Clogging
Traditional vibrating screens often suffer from mesh clogging due to the fine and adhesive nature of lithium manganate powder, leading to reduced sieving efficiency and increased downtime.
To overcome these challenges, an ultrasonic vibrating sieve provides an ideal solution by combining mechanical vibration with high-frequency ultrasonic energy to enhance the sieving process.
How the Ultrasonic Vibrating Sieve Works
An ultrasonic vibrating sieve integrates conventional vibrating screen technology with ultrasonic wave technology to create a more efficient and precise sieving process. Its working process includes the following steps:
- Basic Vibrating Motion
The vibrating sieve generates a mechanical vibration at a fixed frequency, causing the lithium manganate powder to spread evenly across the screen surface. - Application of Ultrasonic Energy
An ultrasonic transducer converts electrical energy into high-frequency sound waves (usually around 36–40 kHz). These sound waves create micro-vibrations on the screen mesh. - Improved Separation Efficiency
The combination of mechanical and ultrasonic vibrations breaks down agglomerates, reduces friction between particles, and prevents adhesion to the screen. This allows even fine lithium manganate particles to pass through the mesh easily. - Impurity Removal and Size Classification
Particles that meet the required size pass through the mesh, while larger particles, impurities, and agglomerates are separated and removed from the process.
Advantages of Using Ultrasonic Vibrating Sieve for Lithium Manganate
The ultrasonic vibrating sieve offers several key benefits when processing lithium manganate:
1. High Sieving Precision
The ultrasonic vibration increases the efficiency of the screening process, ensuring that only particles of the desired size are collected. This results in a more uniform particle size distribution, which is critical for consistent battery performance.
2. Effective Impurity Removal
Metal fragments, dust, and other contaminants are efficiently separated from the lithium manganate powder, improving the purity of the final product.
3. Prevention of Mesh Clogging
The ultrasonic waves prevent particles from sticking to the mesh surface, reducing downtime and maintaining a steady production flow. Traditional screens often face clogging issues, but ultrasonic sieves minimize this problem by breaking down particle adhesion at a micro level.
4. Enhanced Production Efficiency
By increasing the screening speed and precision, the ultrasonic vibrating sieve boosts overall production capacity while maintaining consistent quality.
5. Handling of Fine and Lightweight Particles
Ultrasonic energy allows the separation of even the finest lithium manganate particles without loss, which is challenging for conventional sieving methods.
Application of Ultrasonic Vibrating Sieve in Battery Production
The ultrasonic vibrating sieve is widely used in the battery industry for the processing of lithium manganate and other cathode materials. Its applications include:
- Cathode Material Production – Ensures consistent particle size and purity of lithium manganate used in high-performance batteries.
- Battery Recycling – Facilitates the recovery of lithium manganate from spent batteries by separating impurities and unwanted particles.
- Research and Development – Provides precise control over particle size and purity during the formulation of new battery materials.
- Battery Manufacturing Lines – Integrated into automated production lines to enhance the efficiency and accuracy of material processing.
Why High-Quality Sieving Matters for Battery Performance
The electrochemical performance of a lithium-ion battery is directly influenced by the quality of its cathode material. Impurities or inconsistent particle sizes in lithium manganate can lead to:
- Reduced Battery Capacity – Contaminants can interfere with the charge and discharge cycle, reducing overall capacity.
- Shorter Cycle Life – Inconsistent particle size distribution leads to uneven lithium-ion flow, accelerating degradation.
- Lower Efficiency – Impurities increase internal resistance, reducing the efficiency of energy transfer.
- Safety Risks – Metal particles and agglomerates can cause internal short circuits, increasing the risk of overheating and thermal runaway.
By using an ultrasonic vibrating sieve to ensure high purity and consistent particle size distribution, manufacturers can produce more reliable and longer-lasting batteries.