In the mining and metallurgical industries, the efficient screening of fine materials such as tungsten powder is a critical step in ensuring product quality and operational efficiency. Tungsten powder, known for its high density and fine particle size, presents unique challenges during the screening process. Traditional screening methods often struggle with issues such as clogging, low throughput, and inconsistent particle separation. However, the advent of linear vibrating screens has revolutionized the screening process, offering a reliable and efficient solution for tungsten powder screening.
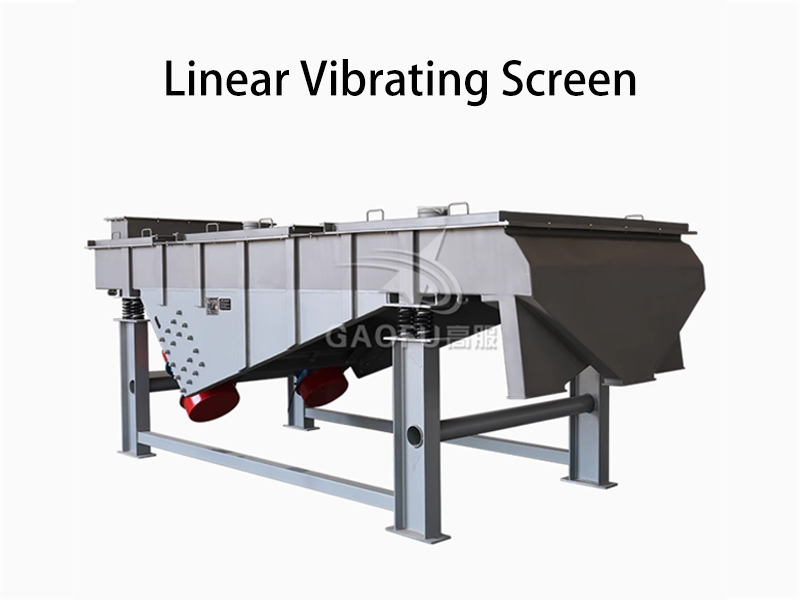
Challenges in Tungsten Powder Screening
Tungsten powder is widely used in various industries, including aerospace, electronics, and manufacturing, due to its exceptional hardness, high melting point, and durability. However, its fine particle size and tendency to agglomerate make it difficult to screen using conventional methods. Common issues include:
- Clogging and Blinding: The fine particles of tungsten powder can easily clog the screen mesh, reducing screening efficiency and requiring frequent maintenance.
- Low Throughput: Traditional screens often struggle to handle large volumes of tungsten powder, leading to bottlenecks in production.
- Inconsistent Particle Separation: Achieving precise particle size distribution is crucial for many applications, but traditional screens may fail to deliver consistent results.
The Role of Linear Vibrating Screens
Linear vibrating screens have emerged as a game-changer in the screening of tungsten powder. These screens utilize a linear motion to propel materials across the screen surface, ensuring efficient separation and minimal clogging. Here’s how they address the challenges associated with tungsten powder screening:
- High Screening Efficiency: The linear motion of the screen ensures that particles are evenly distributed across the mesh, reducing the likelihood of clogging and blinding. This results in higher screening efficiency and longer operational life.
- Large Throughput Capacity: Linear vibrating screens are designed to handle large volumes of material, making them ideal for high-capacity operations. This is particularly beneficial in industries where tungsten powder is produced in bulk.
- Precise Particle Separation: The adjustable amplitude and frequency of the linear vibrating screen allow for precise control over the screening process. This ensures that tungsten powder is separated according to the desired particle size distribution, meeting the stringent requirements of various applications.
- Low Maintenance: The robust design of linear vibrating screens minimizes wear and tear, reducing the need for frequent maintenance. This translates to lower operational costs and increased productivity.
Key Features of Linear Vibrating Screens
- Durable Construction: Made from high-quality materials, linear vibrating screens are built to withstand the harsh conditions of mining and metallurgical operations.
- Adjustable Parameters: Operators can easily adjust the amplitude, frequency, and angle of the screen to optimize performance for different materials and screening requirements.
- Modular Design: The modular design of linear vibrating screens allows for easy replacement of screen meshes and other components, further enhancing their versatility and longevity.
Applications in the Tungsten Industry
Linear vibrating screens are widely used in the tungsten industry for various applications, including:
- Ore Processing: Screening tungsten ore to separate valuable minerals from waste material.
- Powder Classification: Ensuring that tungsten powder meets the required particle size specifications for specific applications.
- Quality Control: Maintaining consistent product quality by removing oversized or undersized particles.