In modern industries, material purity plays a critical role in ensuring product quality and performance. One of the most effective technologies for refining materials and removing impurities is the ultrasonic vibrating screen. This advanced sieving system is particularly beneficial in the classification and purification of microspheres, which are widely used in pharmaceuticals, chemicals, coatings, and various high-tech applications.
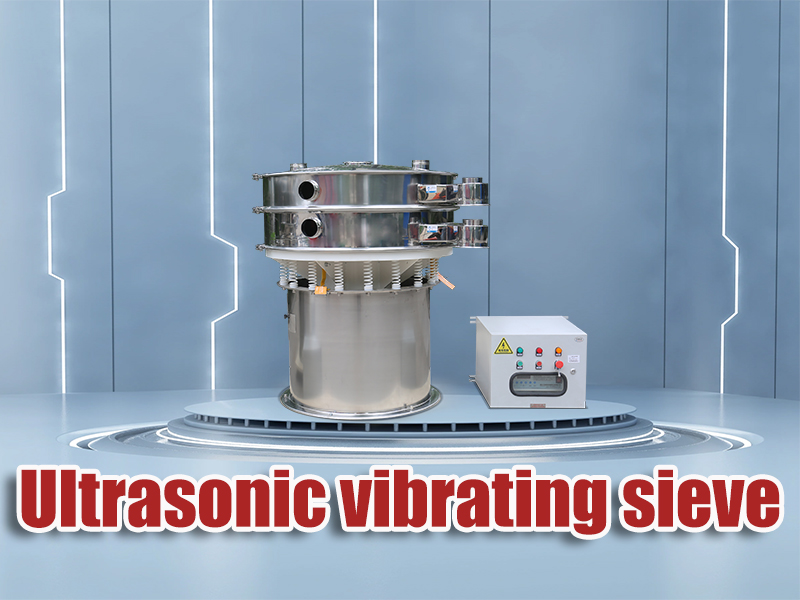
The Role of Ultrasonic Vibrating Screens in Microsphere Sieving
Ultrasonic vibrating screens utilize high-frequency ultrasonic vibrations to enhance the screening process. Traditional mechanical sieving methods often encounter challenges such as mesh clogging, insufficient precision, and low efficiency when dealing with fine and ultra-fine particles. By integrating ultrasonic energy into the sieving process, these issues are significantly mitigated, leading to superior performance in microsphere classification.
The ultrasonic vibrations create a high-frequency oscillation on the mesh surface, preventing the adhesion of fine particles and ensuring continuous and efficient screening. This technology enables the separation of microspheres based on size, shape, and density, ultimately improving material uniformity and purity.
Key Advantages of Ultrasonic Vibrating Screens
- Enhanced Sieving Accuracy – The application of ultrasonic energy allows for precise separation of microspheres, ensuring that only particles of the desired size pass through the screen while effectively removing contaminants and oversized particles.
- Prevention of Mesh Clogging – One of the primary issues with conventional sieving methods is the blockage of screen openings, reducing efficiency. The ultrasonic vibrations continuously clean the mesh, preventing particle adhesion and maintaining optimal performance.
- Increased Sieving Efficiency – Compared to traditional sieving techniques, ultrasonic screens significantly improve throughput, allowing for faster processing and higher yields without compromising accuracy.
- Improved Material Purity – By effectively eliminating unwanted impurities, dust, and foreign particles, ultrasonic sieving enhances the overall purity of microspheres, which is crucial for industries that require high-quality materials.
- Minimal Material Wastage – The gentle yet effective screening process minimizes material loss, ensuring maximum utilization of raw materials and reducing production costs.
Applications in Various Industries
Ultrasonic vibrating screens have found widespread applications in industries that demand high precision and purity, including:
- Pharmaceuticals: Ensuring the purity of drug formulations by removing unwanted particles and contaminants from active pharmaceutical ingredients (APIs).
- Chemicals: Improving the quality of chemical powders and ensuring uniform particle size distribution.
- Coatings and Paints: Enhancing the consistency of pigments and fillers by eliminating unwanted debris.
- Food Processing: Screening food additives and ingredients to ensure product safety and compliance with regulatory standards.
- Advanced Materials: Purifying high-tech materials used in electronics, aerospace, and nanotechnology applications.