Modern fine powder processing faces increasing demands for precision, consistency, and efficiency—especially when working with complex materials like zinc powder. Traditional sieving methods often prove inadequate due to the challenging nature of such powders, which typically exhibit strong adsorption, high cohesiveness, stickiness, static electricity, high density, and extremely fine particle sizes. These characteristics complicate the screening process, leading to issues such as clogging, low throughput, and compromised product quality.
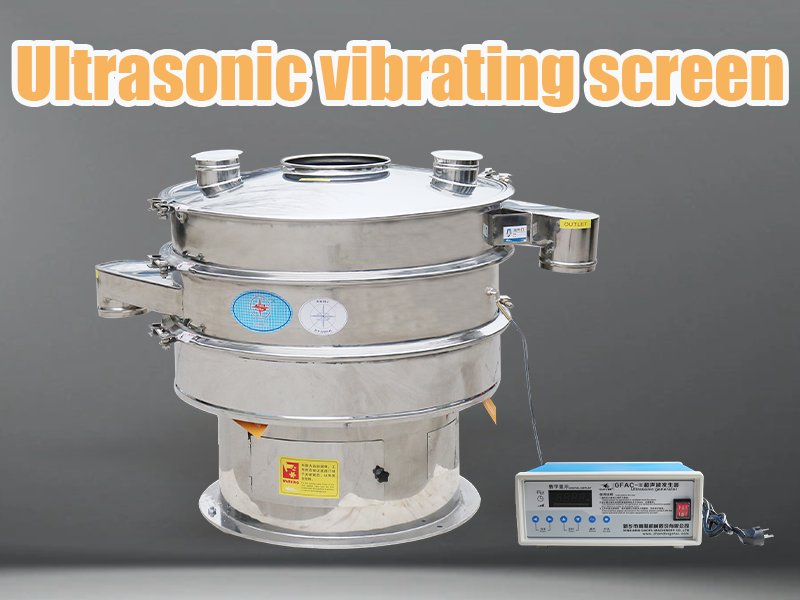
To overcome these obstacles, the ultrasonic vibrating screen has emerged as an advanced and highly effective solution, offering notable improvements in both screening performance and final material quality.
Ultrasonic vibrating screens utilize advanced ultrasonic technology to revolutionize the way fine powders are screened. By converting standard 220V, 50Hz electrical energy into high-frequency 36KHz mechanical vibrations, the system introduces an ultrasonic wave directly onto the screen mesh. This technology effectively reduces friction, prevents clogging, and facilitates the smooth passage of ultrafine particles through the mesh, even those that would typically adhere due to electrostatic forces or moisture content.
One of the most remarkable advantages of the ultrasonic vibrating screen is its ability to handle powders that are traditionally considered difficult to screen. Materials like zinc powder often exhibit strong intermolecular forces, leading to agglomeration and inconsistent particle separation. The ultrasonic system addresses this by disrupting these forces, allowing for cleaner separation and a more uniform particle distribution. As a result, the quality of the sieved zinc powder is significantly enhanced, making it more suitable for industrial applications such as coatings, metallurgy, battery production, and chemical processes.
Furthermore, the system improves operational efficiency by preventing screen blinding—a common issue where particles block mesh apertures, leading to frequent cleaning interruptions. The self-cleaning function of the ultrasonic vibration reduces downtime, minimizes labor costs, and extends the service life of the mesh. This ensures a continuous and stable production process with higher throughput and greater yield.
From a technical standpoint, the integration of ultrasonic waves into the vibratory screening process does not interfere with the physical or chemical properties of the zinc powder. It is a non-destructive, clean technology that enhances the screening process without introducing contaminants or altering the powder's composition. This makes it ideal for industries that require strict quality standards and consistency.