al operation in many industries, including mining, metallurgy, chemicals, construction, and recycling. The process involves separating materials based on their size to ensure the efficient production of the desired product. One of the most effective and widely used machines for this purpose is the linear vibrating screen.
What is a Linear Vibrating Screen?
A linear vibrating screen is a type of mechanical screening device that moves materials across a surface in a linear motion. It typically consists of a screen deck, vibration motors, and a frame. The materials are fed onto the screen deck, where the vibration causes them to travel along the surface, sorting them according to size. Linear vibrating screens are used in applications that require precise separation of materials, from fine to coarse particles.
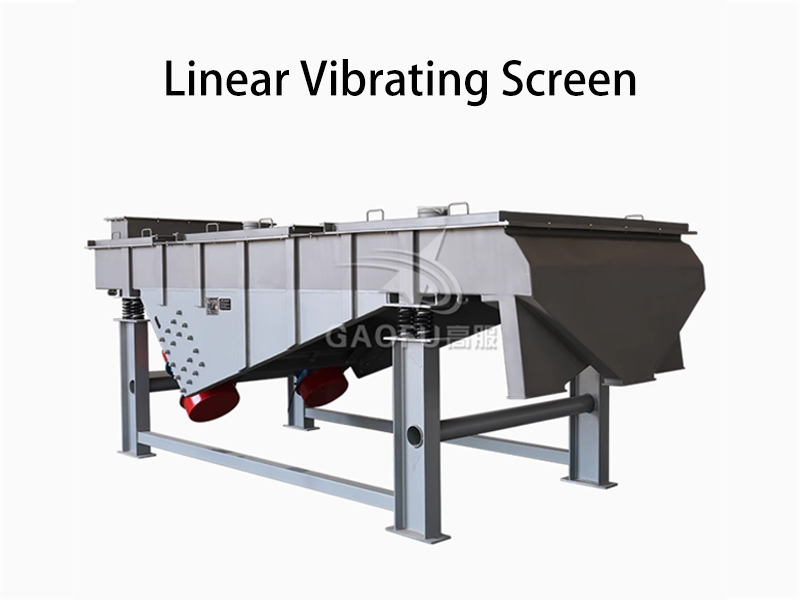
Key Advantages of Linear Vibrating Screens
Before diving into how to optimize material screening efficiency, let’s review the key advantages of linear vibrating screens:
- High Efficiency and Large Capacity: Linear vibrating screens can handle large quantities of material due to their high capacity and efficient operation. This makes them suitable for industries where large-scale screening is necessary.
2. Adjustable Vibration Parameters: The vibration amplitude and frequency of linear vibrating screens can be adjusted to suit different types of materials and the specific requirements of the screening process.
3. Durability and Low Maintenance: Linear vibrating screens are robust and built to withstand harsh conditions. Their durable design ensures long service life, minimizing downtime and maintenance costs.
4. Precise Material Separation: The linear motion ensures that materials are effectively separated based on particle size. The accuracy of separation improves the overall quality of the final product.
5. Energy Efficiency: Linear vibrating screens are energy-efficient compared to other types of screening equipment, reducing operational costs.
Methods to Improve Material Screening Efficiency with Linear Vibrating Screens)
- Optimize the Vibration Parameters(Frequency and Amplitude)
The vibration frequency and amplitude of a linear vibrating screen play a crucial role in material movement and screening efficiency. Adjusting these parameters can improve the screening performance for different types of materials.
- Frequency: Increasing the frequency of the vibration can help materials move faster across the screen, which is useful when screening fine particles or materials that are easily sieved. Conversely, a lower frequency might be more suitable for larger, heavier materials that need more time to pass through the screen.
- Amplitude: The amplitude refers to the height of the vibration. Increasing the amplitude is beneficial for improving the efficiency of screening heavy or wet materials, as it helps dislodge particles that may be stuck together or attached to larger pieces. On the other hand, a lower amplitude may improve the efficiency when dealing with fine or dry particles.
Optimization Tip: For materials that are difficult to separate, like sticky or wet materials, increase the amplitude to promote better material flow. For finer materials, adjust the frequency to facilitate efficient passage through the screen.
2. Use Multiple Screen Decks for Multi-Stage Separation
A linear vibrating screen with multiple screen decks allows for multi-stage separation, increasing the overall efficiency of the screening process. Each deck can be configured to target different particle sizes, which ensures that the materials are separated in finer and more accurate increments.
- The upper deck might handle coarser material, while the lower decks can separate smaller particles.
- Multi-deck screens can improve screening efficiency by reducing the need for multiple screening machines, thereby optimizing space and energy consumption.
Optimization Tip: Use a multi-deck linear vibrating screen when processing materials that require multiple stages of separation. This not only saves space but also reduces the need for additional equipment, improving overall system efficiency.
3. Ensure Proper Material Feed and Distribution
One of the most common reasons for low screening efficiency is improper material distribution across the screen surface. Uneven material feed leads to clogging and poor separation. It is essential to ensure that the material is evenly distributed across the entire width of the screen.
- Feeding Mechanisms: Install a suitable feeder that ensures a constant, uniform flow of material onto the vibrating screen. Overloading or underloading the screen will reduce its effectiveness.
- Material Distribution: Use a distribution system, such as a distributing plate or conveyor, to spread the material evenly over the screen surface. This ensures that each portion of the screen is used efficiently, improving throughput.
Optimization Tip: Use a uniform distribution system, such as a vibrating feeder, to evenly distribute material across the screen. This ensures the best screening performance and prevents clogging or material buildup in certain areas.
4. Maintain Optimal Screen Mesh Size
The size of the screen mesh (the openings through which materials pass) is crucial to the efficiency of the screening process. If the mesh is too large, fine materials may pass through without being separated, while smaller particles can get stuck if the mesh is too fine.
- Mesh Size: Choose the appropriate mesh size based on the material’s particle size distribution. Generally, finer materials require smaller mesh sizes, while coarser materials need larger openings.
- Mesh Material: The choice of mesh material can also impact efficiency. For example, stainless steel mesh is more durable and resistant to wear, while polyurethane mesh offers higher wear resistance and self-cleaning properties.
Optimization Tip: Regularly monitor and adjust the screen mesh size based on the material being processed. Select mesh sizes that match the material's particle distribution to achieve better separation.
5. Regular Maintenance and Cleaning
To keep the linear vibrating screen working at peak efficiency, it’s essential to perform regular maintenance and cleaning. Over time, the screen may become clogged with fine materials, reducing its effectiveness.
- Screen Surface Cleaning: Clean the screen periodically to prevent blockages and maintain optimal material flow. This can be achieved through automatic cleaning systems or manual cleaning.
- Vibration Motor Maintenance: Inspect the vibration motors regularly to ensure they are operating at the correct frequency and amplitude. Any malfunction or wear on the motors can reduce screening performance.
Optimization Tip: Implement a preventive maintenance schedule to clean and inspect the screen regularly. This ensures continuous, efficient operation and minimizes unplanned downtime.
6. Improve Material Characteristics
Sometimes, the problem with low screening efficiency lies in the material itself rather than the screening equipment. By improving the material characteristics, the efficiency of the linear vibrating screen can be significantly enhanced.
- Moisture Content: High moisture content can cause clumping, clogging, or inefficient separation. Reducing moisture content or adding drying equipment can improve material flow.
- Particle Shape: Irregularly shaped particles are more likely to cause blockages or poor separation. If possible, modify the material to create more uniform particle shapes.
Optimization Tip: Control material characteristics such as moisture content and particle shape to improve screening performance. For example, reducing moisture content can help avoid clogging, while uniform particle size allows for more efficient separation.