In industrial screening processes, maintaining equipment efficiency and minimizing downtime are critical factors for productivity. One innovative solution that significantly enhances performance and reduces equipment failure rates is the ultrasonic vibrating screen. By incorporating high-frequency ultrasonic vibrations, this advanced screening technology prevents common issues that lead to operational failures, such as clogging, excessive wear, and mechanical stress. This article explores how ultrasonic vibrating screens improve reliability and longevity in screening applications.
Understanding Ultrasonic Vibrating Screens
An ultrasonic vibrating screen integrates a high-frequency ultrasonic transducer into a traditional vibrating screen. The transducer applies ultrasonic frequency vibrations (typically around 36 kHz to 40 kHz) to the screen mesh, effectively preventing material blockages and enhancing the screening process. This additional vibration layer breaks down agglomerated particles and keeps the mesh free from clogging.
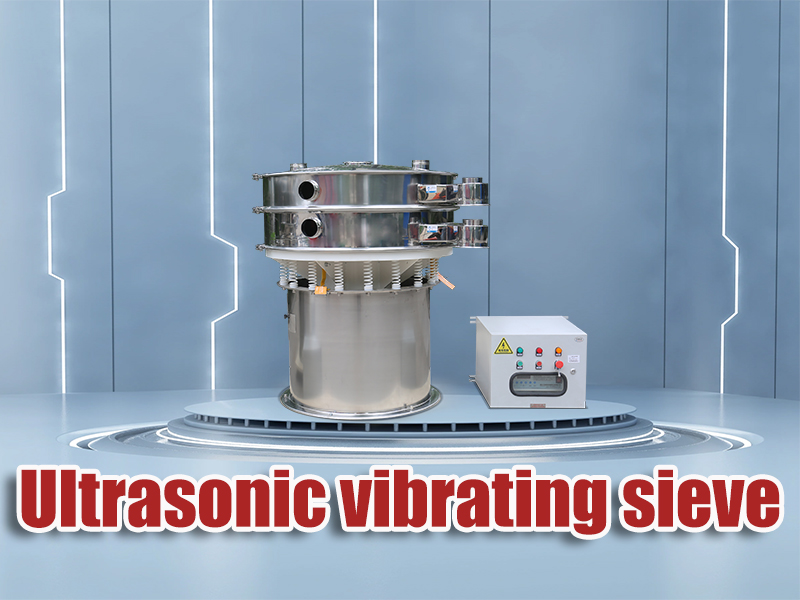
How Ultrasonic Vibrating Screens Reduce Equipment Failure Rate
1. Prevention of Mesh Clogging and Blockages
One of the primary reasons for equipment failure in traditional vibrating screens is mesh clogging, which occurs when fine powders or sticky materials accumulate on the mesh surface. This leads to:
- Reduced screening efficiency
- Increased mechanical load on the equipment
- Frequent maintenance and downtime
The ultrasonic vibration technology continuously agitates the screen mesh at a high frequency, effectively preventing clogging and keeping the material flowing smoothly. This reduces the strain on the equipment and prolongs its lifespan.
2. Reduction of Wear and Tear on Mechanical Components
Traditional vibrating screens often experience high mechanical stress due to repeated forceful vibrations. This results in wear and tear on key components such as:
- Screen mesh
- Springs
- Motor bearings
Ultrasonic vibrating screens reduce the need for intense mechanical motion by introducing high-frequency ultrasonic waves. These waves enhance the screening process without excessive mechanical force, leading to lower wear and a longer operational life for the equipment.
3. Enhanced Screening Efficiency and Reduced Overloading
When a vibrating screen is inefficient, it can lead to overloading, which stresses the motor and supporting structure. Over time, this can cause:
- Motor overheating and failure
- Structural fatigue and cracks
- Increased power consumption
Ultrasonic vibrating screens enhance screening efficiency by breaking down fine or difficult-to-screen materials, ensuring a steady flow of material and preventing overloading. This results in reduced energy consumption and a lower likelihood of motor burnout.
4. Minimized Downtime Due to Maintenance and Repairs
Frequent breakdowns and maintenance can lead to significant production losses. Traditional screens require frequent cleaning and part replacements due to:
- Mesh clogging
- Worn-out screen panels
- Loose or broken mechanical parts
With ultrasonic screening technology, maintenance requirements are significantly reduced as the system keeps the mesh clean and reduces mechanical strain. Less frequent maintenance means lower costs and increased production uptime.
5. Improved Accuracy in Screening Operations
Material inconsistencies and incorrect particle separation can lead to rework, quality issues, and product rejection. An ultrasonic vibrating screen improves accuracy by:
- Ensuring uniform material distribution across the screen
- Reducing fine particle adhesion and agglomeration
- Providing precise separation of materials without excessive force
By maintaining consistent screening performance, the risk of equipment stress due to incorrect material flow is minimized, contributing to a more reliable and failure-resistant operation.