Horizontal Airflow Vibrating Sieve for Screening Magnesium Oxide Powder: A Comprehensive Overview
Magnesium oxide (MgO) is a critical material in various industries, including metallurgy, refractory, environmental protection, and even medicine. It is commonly used as a catalyst, a binder in ceramics, and in the production of insulation materials. As the demand for high-quality magnesium oxide increases, the need for efficient, precise, and high-throughput processing equipment becomes paramount.
One such solution to meet these needs is the horizontal airflow vibrating sieve, an innovative screening machine designed to separate magnesium oxide powder into specific particle sizes for further processing. This article will delve into the workings, benefits, and applications of this equipment, especially in terms of screening magnesium oxide powder at a throughput of 600kg/h.
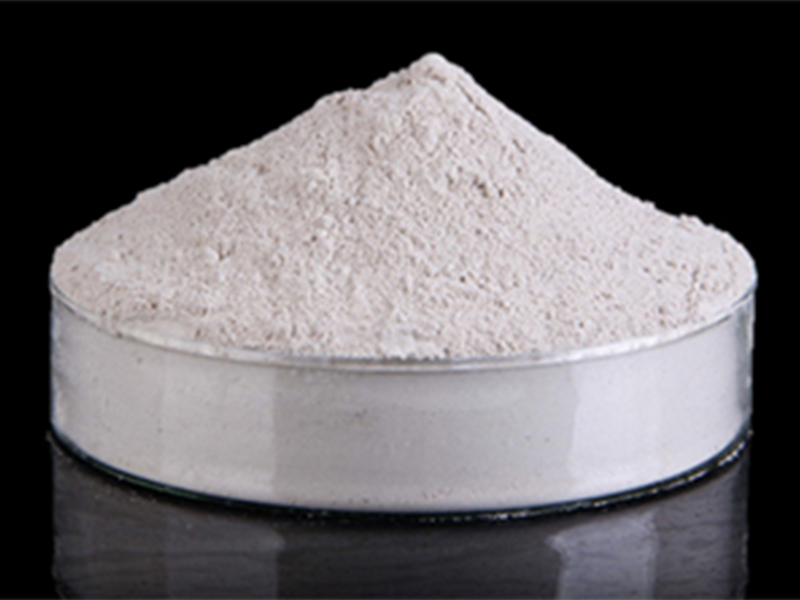
What is a Horizontal Airflow Vibrating Sieve?
A horizontal airflow vibrating sieve is an advanced type of sieving equipment that combines both airflow technology and vibration mechanics. The sieve works by using air currents to help move powder through the mesh while simultaneously vibrating to facilitate the separation of particles based on size. This combination of airflow and vibration ensures that fine powders, such as magnesium oxide, are effectively screened with minimal clogging and maximum efficiency.
Unlike traditional vibrating sieves, which rely solely on vibration to push particles through the screen, the horizontal airflow sieve adds an air-stream function that enhances the separation process. This results in more precise grading and improved performance, especially for light and fine powders like magnesium oxide.
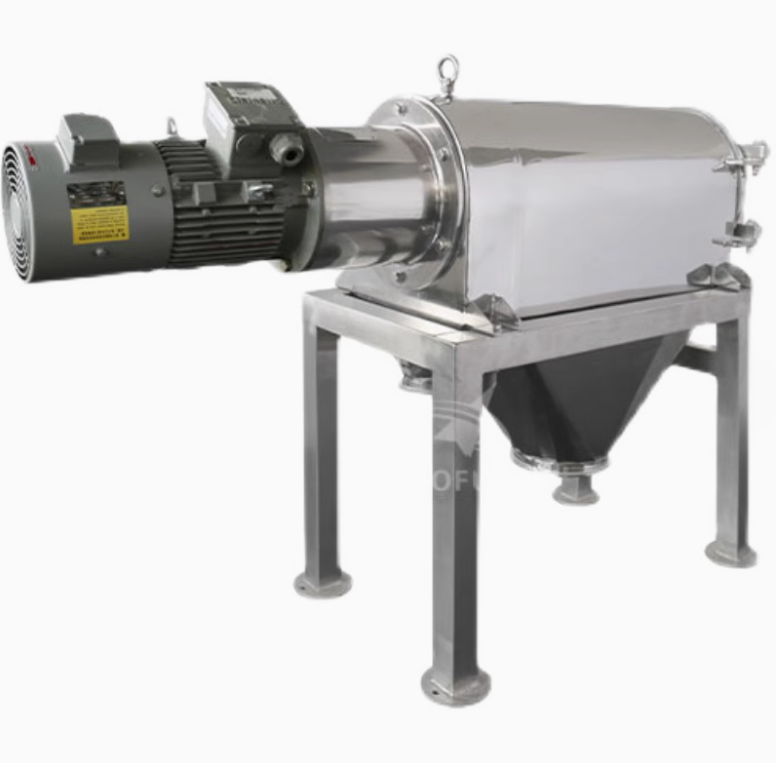
Key Features of Horizontal Airflow Vibrating Sieve
High Throughput: The sieve can process up to 600kg of magnesium oxide powder per hour, making it suitable for medium to large-scale production environments. The combination of airflow and vibration allows the machine to maintain high throughput while ensuring precise classification.
Efficient Screening: The sieve ensures uniform distribution of the material across the mesh, preventing blockages and achieving accurate separation. The air currents help to keep the powder in motion, reducing the chance of clogging, a common issue in traditional sieving methods.
Fine and Coarse Particle Separation: The sieve is capable of classifying magnesium oxide powder into multiple grades, helping to ensure that only the desired particle sizes proceed to the next stage in production. This is particularly important when uniform particle size is crucial for the end product's quality.
Low Energy Consumption: Compared to other screening methods, the horizontal airflow vibrating sieve operates with relatively low energy consumption due to the efficient use of airflow technology in tandem with vibration.
Compact and Space-Saving Design: The horizontal design ensures that the sieve takes up less vertical space, making it ideal for facilities with limited space. The compact footprint allows for easy integration into existing production lines.
High Screening Precision: The precise control over the airflow allows for excellent accuracy in separating fine and coarse particles, ensuring high-quality magnesium oxide powder.
Working Principle
The horizontal airflow vibrating sieve consists of a mesh screen that is slightly inclined in a horizontal orientation. Air is drawn into the sieve through the air intake system, creating a gentle airflow that passes through the powder. This airflow pushes the powder particles across the screen, where they are subjected to vibratory motion.
As the powder moves across the screen, larger particles are retained while smaller particles pass through the mesh. The airflow ensures that particles are evenly distributed on the screen, preventing any blockages that could hinder the sieving process. This dual-action method helps achieve high-efficiency screening with minimal downtime.
Applications for Magnesium Oxide Powder
Magnesium oxide powder is widely used across industries such as:
- Metallurgical Industry: For producing refractory materials, MgO is often required in specific particle sizes. The horizontal airflow vibrating sieve ensures that only the desired grades are used in production.
- Environmental Protection: Magnesium oxide is used in air purification, wastewater treatment, and flue gas desulfurization. Consistent powder quality and precise particle size are essential to meet regulatory standards.
- Ceramics and Construction: Magnesium oxide is used as a binder in the production of cement, tiles, and bricks. In these applications, the powder must be finely and uniformly screened to achieve optimal results.
- Pharmaceuticals and Food Processing: In industries where purity and consistency are critical, such as pharmaceuticals or food production, a vibrating sieve ensures the magnesium oxide powder is free from contaminants and properly screened for safe use.
Benefits of Using Horizontal Airflow Vibrating Sieves
- Improved Process Efficiency: The horizontal airflow vibrating sieve provides a high throughput of up to 600kg/h, enabling businesses to meet production demands without compromising on quality.
- Enhanced Product Quality: With its ability to effectively separate fine and coarse particles, the sieve ensures that only the finest, most consistent magnesium oxide powder moves forward in the production process, resulting in better-quality end products.
- Reduced Maintenance Costs: The sieve’s design minimizes wear and tear, leading to longer service life and lower maintenance costs. The mesh doesn’t easily clog, reducing downtime associated with cleaning or replacing screens.
- Energy Savings: The efficient use of airflow in combination with vibration technology results in lower energy consumption compared to traditional sieving methods. This makes the horizontal airflow vibrating sieve a more environmentally friendly and cost-effective option.
- Flexible Operation: With adjustable parameters for both airflow and vibration, the sieve can be fine-tuned to suit different types of powders and various production requirements, making it adaptable to a wide range of industrial applications.
The horizontal airflow vibrating sieve for screening magnesium oxide powder at 600kg/h represents a significant leap forward in powder processing technology. By combining the benefits of airflow and vibration, this sieve offers high efficiency, precise separation, and minimal maintenance, making it an ideal solution for industries relying on high-quality magnesium oxide.
In industries where uniform particle size is crucial, such as metallurgy, ceramics, and environmental protection, this equipment provides the necessary precision and throughput to meet production goals. If you’re looking to improve the quality, efficiency, and cost-effectiveness of your magnesium oxide screening process, a horizontal airflow vibrating sieve is a smart investment.