The production of high-quality silicon negative electrode materials is essential for the performance of modern lithium-ion batteries. As the demand for batteries continues to rise, especially in electric vehicles and renewable energy storage systems, the need for efficient screening and purification of raw materials becomes increasingly important. Ultrasonic vibrating screens are at the forefront of achieving this, offering an efficient method for removing impurities from silicon negative electrode materials during the production process.
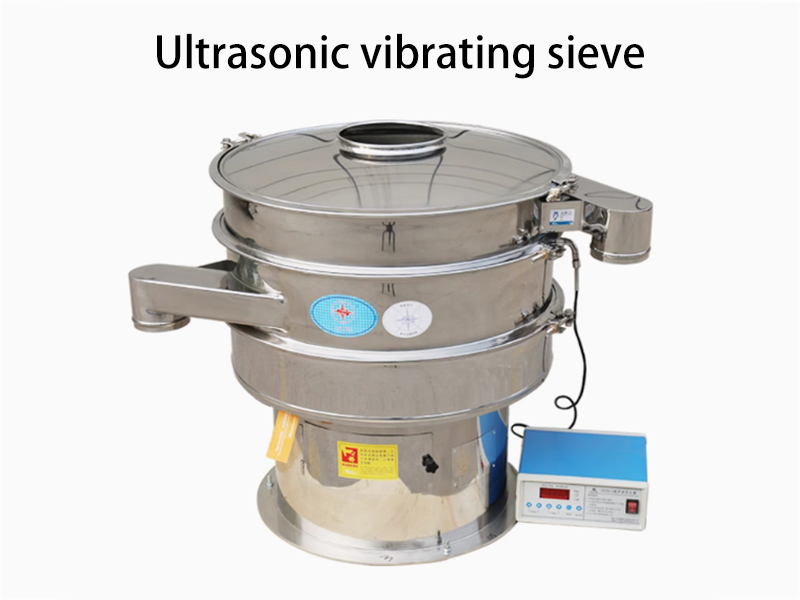
This article explores how ultrasonic vibrating screens are used to remove impurities from silicon negative electrode materials, ensuring high-quality, impurity-free components for battery manufacturing. We will highlight the key benefits and applications of ultrasonic screening technology in the production of silicon-based electrode materials.
What is an Ultrasonic Vibrating Screen?
An ultrasonic vibrating screen is an advanced sieving technology that combines traditional vibration with high-frequency ultrasonic waves to achieve superior screening efficiency. The ultrasonic waves generate high-frequency vibrations on the screen mesh, preventing material from clogging and ensuring finer separation and higher precision.
In industries like battery manufacturing, where the purity of raw materials is critical to the performance of the final product, the ultrasonic vibrating screen provides a reliable solution for effective screening of fine powders like silicon negative electrode materials. The technology's ability to remove microscopic impurities from these powders ensures that only high-quality materials are used in the manufacturing of batteries.
Importance of Impurity Removal in Silicon Negative Electrode Materials
Silicon is becoming an increasingly important material for negative electrodes in lithium-ion batteries due to its high energy density compared to traditional graphite electrodes. However, impurities in silicon powders can significantly degrade the performance and safety of lithium-ion batteries. Common issues caused by impurities include:
- Reduced battery capacity: Impurities can interfere with the charge/discharge efficiency, leading to lower energy storage capacity.
- Decreased cycle life: The presence of foreign particles may cause mechanical stresses and structural damage during the charging cycles, reducing the battery's lifespan.
- Inconsistent performance: Impurities can lead to inconsistent charge/discharge behavior, affecting the reliability and safety of the battery.
Therefore, removing impurities from silicon negative electrode materials is vital to ensuring that the materials perform optimally and meet the stringent requirements of the battery industry.
How the Ultrasonic Vibrating Screen Helps
The ultrasonic vibrating screen is specifically designed to address the challenges of screening and purification in industries like battery manufacturing. Here's how this advanced technology improves the quality and consistency of silicon negative electrode materials:
1. High Screening Efficiency
By combining ultrasonic waves with mechanical vibration, the ultrasonic vibrating screen delivers superior screening efficiency compared to traditional methods. The ultrasonic waves reduce the tendency for particles to clump together or stick to the mesh, ensuring continuous and smooth material flow. This allows for a more thorough separation of fine silicon particles from impurities and results in a cleaner, higher-quality product.
2. Effective Removal of Fine Impurities
One of the key benefits of using an ultrasonic vibrating screen is its ability to remove fine impurities that are often difficult to capture with traditional screening methods. The ultrasonic waves create high-frequency vibrations that help dislodge and separate microscopic particles and contaminants from the main material, ensuring that only pure silicon remains. This is crucial for producing high-performance silicon-based electrodes for batteries.
3. Prevention of Clogging and Mesh Blockage
Silicon powders, especially fine particles, can be prone to clogging or mesh blockage during screening. Traditional sieving methods often struggle with fine powders, leading to inefficient material flow and incomplete impurity removal. However, the ultrasonic vibrations prevent this issue by keeping the mesh surface clean and free from blockages, allowing for continuous and efficient screening.
4. Increased Product Consistency and Quality
By ensuring that only impurity-free silicon is used in the production of negative electrodes, the ultrasonic vibrating screen plays a key role in enhancing the consistency and quality of the final product. This consistency is critical in the manufacturing of lithium-ion batteries, where performance is directly tied to the purity of the materials used.
5. Improved Battery Performance
When impurities are removed from the silicon material, the final silicon negative electrode exhibits enhanced energy density, cycle stability, and charge/discharge efficiency. By using the ultrasonic vibrating screen for impurity removal, manufacturers can ensure that their silicon-based electrodes meet the strict quality standards required for high-performance lithium-ion batteries.
Key Applications in the Battery Industry
The ultrasonic vibrating screen is essential in the production of silicon negative electrode materials for lithium-ion batteries. During the screening and purification stages, the ultrasonic vibrating screen ensures that the silicon powder is free from any contaminants that could negatively impact the performance of the final product.
For battery manufacturers, the purity of the silicon material is critical for creating high-capacity, long-lasting batteries. Any impurity in the silicon material could result in reduced battery lifespan, less efficient energy storage, and inconsistent performance. Using ultrasonic vibrating screens helps ensure that only the best quality silicon is used in the production process.