The manufacturing of screen mesh involves several critical steps, each ensuring the precision, strength, and durability of the final product. From the initial measurement of wire diameter to the final inspection before storage, every phase plays a crucial role in producing a high-quality, reliable mesh. The following outlines the detailed screen mesh production process, highlighting key steps that emphasize quality control and performance.
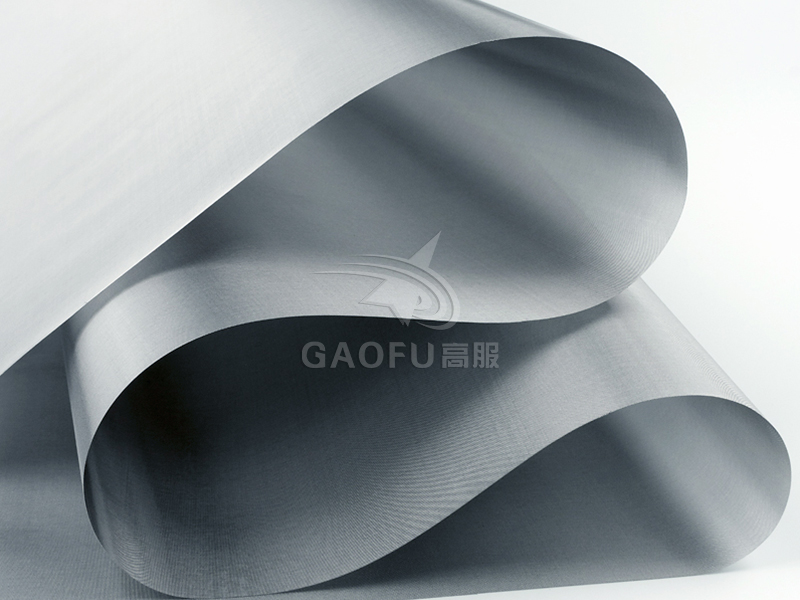
1. Measuring Wire Diameter: Ensuring Precision from the Start
The very first step in the screen mesh production process involves measuring the wire diameter. The wire diameter is essential as it directly influences the mesh’s strength, flexibility, and durability. It must be accurately measured to meet the specific requirements of the application for which the screen mesh is intended. This measurement ensures that the mesh performs optimally under the required operating conditions, whether in screening, filtering, or separating materials.
Using advanced measurement tools and equipment, manufacturers ensure that the wire diameter is consistent throughout production. Variations in wire thickness can lead to weaker or less durable mesh, potentially affecting performance and causing premature wear and tear.
2. Measuring Wire Tensile Strength: Ensuring Durability and Resistance
After measuring the wire diameter, the next step involves measuring the wire tensile strength. Tensile strength is a measure of the material’s ability to resist pulling forces and is critical for ensuring that the screen mesh can withstand the stresses of daily use. A high tensile strength ensures that the mesh will not stretch or break easily under tension, making it ideal for heavy-duty applications that involve harsh environments or large volumes of materials.
The tensile strength measurement provides valuable data about the overall durability of the mesh. It ensures that the wire can endure the operational forces exerted during the screening or filtering process without failing. This step is essential in confirming the quality and reliability of the mesh before moving forward.
3. Warping (Beaming): Preparing the Wire for Weaving
Warping, or beaming, is the process of arranging the wire strands into a parallel formation, preparing them for the weaving process. In this stage, the wire is carefully wound onto a beam, which helps organize the wires and ensures that they remain evenly spaced during weaving.
The warping process is crucial to achieving a uniform, consistent weave throughout the screen mesh. Proper warping prevents issues such as uneven tension or misalignment during the subsequent weaving stage, ensuring the mesh maintains its strength and shape throughout its use.
4. Shedding (Weaving Preparation): Setting Up for the Weaving Process
Next comes the shedding process, where the warp wires are manipulated to create the opening for the weft wires. During this step, the machine is set up to allow the weft wires to pass through the warp wires, forming the mesh structure. This stage ensures that the mesh design meets the specific requirements, whether it’s a simple weave, a twilled weave, or another custom pattern.
By accurately setting up the shedding mechanism, manufacturers ensure that the mesh will be consistent in terms of mesh size, strength, and pattern, all of which are critical for the functionality of the finished product.
5. Perforation: Customizing the Mesh for Specific Applications
Perforation is the process of creating holes or openings in the screen mesh. The size and pattern of the perforations are determined based on the specific application, such as filtering, separating, or screening particular materials. During this stage, the mesh is carefully punched or drilled to ensure the correct pore size for its intended use.
This stage is essential because the size of the holes determines the mesh’s ability to handle specific materials, such as fine powders, liquids, or coarse particles. The precision of the perforation process ensures that the mesh will provide optimal performance while meeting the required standards for filtration and separation.
6. Machine Binding: Securing the Mesh for Durability
After the perforation process, the screen mesh undergoes the machine binding step, where the edges of the mesh are securely fastened. This process prevents the mesh from fraying or unraveling, especially when subjected to tension during use. The binding ensures that the mesh maintains its structural integrity even under heavy stress or during long periods of operation.
Machine binding is crucial for enhancing the durability of the mesh, allowing it to withstand wear and tear while maintaining its shape and functionality. This step ensures that the mesh performs efficiently and lasts longer, reducing the need for frequent repairs or replacements.
7. Weaving the Mesh: Crafting the Final Product
At this stage, the process of weaving the mesh begins. Using the previously prepared warp and weft wires, the machine begins interlacing the wires to form the desired mesh pattern. The weaving process is done with great care to ensure uniformity, precision, and the correct mesh size.
The quality of the weave is crucial for the mesh’s performance. A high-quality weave ensures strength, flexibility, and resistance to wear and tear. Whether the mesh is being used for fine filtration or coarse material separation, the weaving stage is key to achieving a mesh that will serve its purpose effectively over time.
8. Rolling the Finished Mesh: Final Preparation for Storage
Once the mesh is woven, the next step is to roll the finished product onto a spool or drum for easy storage and transportation. Typically, a roll of mesh is approximately 30 meters in length, depending on the specifications.
This final step ensures that the mesh is securely packaged and ready for the next phase, whether it’s distribution, installation, or further processing. The rolled mesh can easily be transported to its next destination or delivered to clients for installation in their specific machinery or systems.
9. Final Inspection and Quality Control: Ensuring Consistency and Compliance
Before the screen mesh is officially stored or shipped, it undergoes a thorough inspection to ensure that it meets the required quality standards. During the final inspection, the mesh is examined for:
- Correct Mesh Size: Ensuring that the holes are the right size for the intended application.
- Even Weaving: Checking that the weave is consistent and free from defects.
- Strength and Durability: Ensuring that the mesh can withstand its intended use without breaking or deforming.
- Perforation Quality: Verifying that the perforations are correctly aligned and precise.
Only mesh that passes this inspection is approved for storage and subsequent distribution. This final check ensures that the mesh will perform optimally in its designated applications and deliver the reliable performance expected from high-quality screen mesh products.