Square swing vibrating screens are widely used in industries such as mining, agriculture, chemicals, and food processing for their ability to handle large volumes of materials with high precision. However, as production demands increase, many operations face challenges in scaling up their screening processes. This article provides practical upgrading solutions to transition from low to high production using square swing vibrating screens.
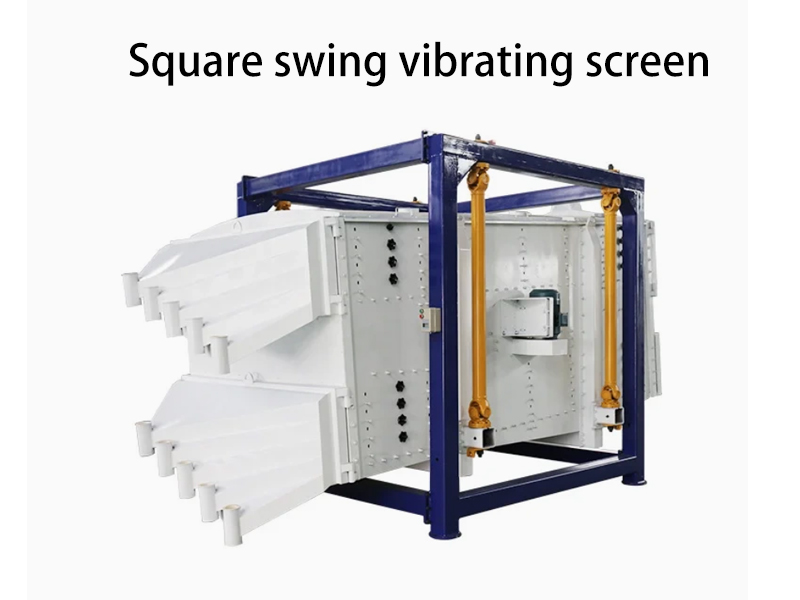
- Assess Current Production Needs
Before upgrading, it’s essential to evaluate your current production requirements and identify bottlenecks. Key considerations include:
- Throughput capacity: Are your screens handling the desired volume of material?
- Screening accuracy: Is the current setup achieving the required particle size separation?
- Downtime frequency: Are frequent breakdowns or maintenance issues slowing production?
Understanding these factors will help you determine the necessary upgrades to meet higher production goals.
2. Upgrade Screen Mesh and Deck Design
The screen mesh and deck design play a critical role in determining screening efficiency. Consider the following upgrades:
- High-performance meshes: Replace standard meshes with high-durability materials like polyurethane or stainless steel, which resist wear and reduce clogging.
- Multi-deck configurations: Adding extra decks allows for simultaneous grading of multiple particle sizes, increasing throughput and efficiency.
- Modular screen panels: These panels are easier to replace and maintain, reducing downtime during mesh changes.
3. Enhance Vibration Mechanisms
The vibration mechanism is the heart of a square swing vibrating screen. Upgrading this component can significantly boost production:
- High-efficiency motors: Install motors with higher power ratings to handle increased material loads and ensure consistent vibration.
- Adjustable amplitude and frequency: Opt for screens with adjustable settings to fine-tune performance for different materials and production rates.
- Balanced vibration systems: Ensure the screen is properly balanced to minimize wear and tear on components, extending equipment life.
4. Optimize Feed and Discharge Systems
Efficient material handling is crucial for high production. Upgrades to consider include:
- Automated feed systems: These systems ensure a consistent and controlled flow of material onto the screen, preventing overloading and improving screening accuracy.
- Enhanced discharge chutes: Redesign chutes to facilitate faster material discharge and reduce bottlenecks.
- Dust containment solutions: Install dust collection systems to improve working conditions and minimize material loss.
5. Implement Advanced Control Systems
Modern control systems can significantly improve the efficiency and reliability of square swing vibrating screens:
- Programmable logic controllers (PLCs): These systems allow for precise control of vibration settings, feed rates, and other parameters.
- Remote monitoring: Use IoT-enabled devices to monitor screen performance in real-time, enabling proactive maintenance and troubleshooting.
- Automated diagnostics: Advanced systems can detect issues such as unbalanced loads or motor failures, reducing downtime.
6. Increase Screen Size and Capacity
For operations requiring a significant boost in production, upgrading to larger screens may be necessary:
- Wider screens: Larger screens provide more surface area for material processing, increasing throughput.
- Heavy-duty frames: Ensure the screen frame is robust enough to handle higher loads and vibrations without compromising stability.
- Custom designs: Work with manufacturers to design screens tailored to your specific production needs.
7. Improve Maintenance Practices
Regular maintenance is critical for sustaining high production levels. Implement the following practices:
- Scheduled inspections: Regularly check screen components for wear and tear, and replace parts as needed.
- Lubrication systems: Install automated lubrication systems to reduce friction and extend the life of moving parts.
- Training programs: Train operators and maintenance staff to identify and address issues quickly, minimizing downtime.
8. Leverage Data and Analytics
Data-driven decision-making can help optimize screen performance and identify areas for improvement:
- Performance tracking: Monitor key metrics such as throughput, screening accuracy, and energy consumption.
- Predictive maintenance: Use data analytics to predict when components are likely to fail, allowing for timely replacements.
- Process optimization: Analyze production data to identify inefficiencies and implement targeted upgrades.