In industries that rely on precise material separation, such as pharmaceuticals, chemicals, food processing, and mining, effective screening is critical for ensuring product quality and process efficiency. However, many materials present unique challenges when it comes to traditional screening methods. Problems like strong viscosity, adsorption, and easy agglomeration can significantly affect the accuracy and efficiency of conventional vibrating screens.
One solution that has emerged to address these challenges is the ultrasonic vibrating sieve. This technology combines the benefits of traditional screening with the power of high-frequency sound waves to effectively handle difficult-to-screen materials. Here’s how ultrasonic vibrating sieves can solve common material screening problems.
The Challenges of Traditional Screening
Before we dive into the benefits of ultrasonic vibrating sieves, it’s important to understand the material screening problems they address:
. Strong Viscosity
Some materials, especially liquids, slurries, or highly viscous powders, have a tendency to stick to the screen mesh. This leads to blockages, reduced throughput, and inconsistent separation. Traditional vibrating screens struggle with these materials because the increased viscosity slows down the flow of material through the screen.
- Adsorption
Materials like activated carbon, fine chemicals, or powdered metals tend to adhere to the mesh due to their sticky or electrostatic properties. This can result in poor separation, as particles aggregate on the mesh, reducing the efficiency of the screening process. - Easy Agglomeration
Certain powders and granular materials are prone to clumping together, creating agglomerates that are much larger than the desired particle size. This results in inaccurate separation and can block the mesh, further reducing the screening efficiency.
How Ultrasonic Vibrating Sieves Work
An ultrasonic vibrating sieve utilizes high-frequency sound waves, typically in the range of 20 to 40 kHz, which are applied to the screen mesh. These ultrasonic waves create a rapid, high-frequency vibration on the mesh surface, preventing material particles from sticking together or adhering to the screen.
The ultrasonic system works in conjunction with the standard vibratory motion of the screen, enhancing the separation process by:
- Reducing friction between the particles and the mesh
- Breaking up agglomerates to allow for better flow and separation
- Reducing adhesion of fine particles or powders to the screen surface
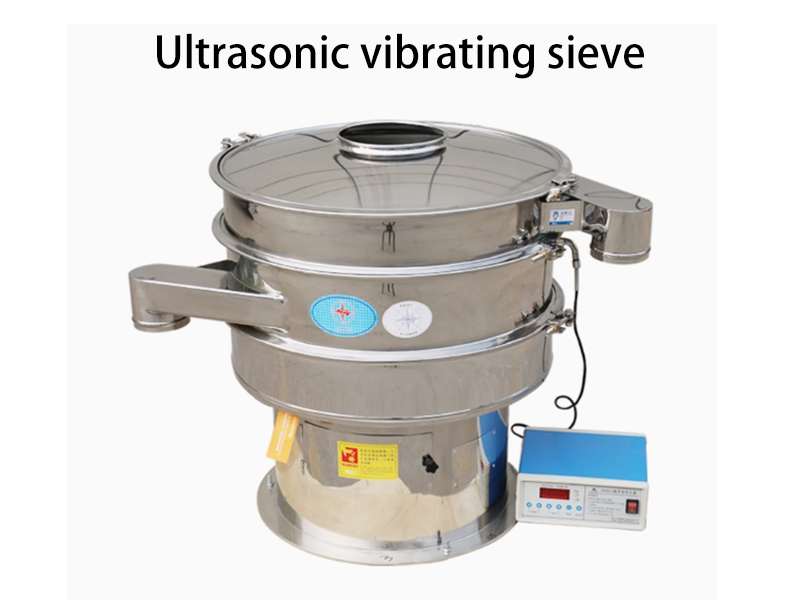
How Ultrasonic Vibrating Sieves Solve Screening Problems
- Eliminating Material Blockage from High Viscosity
In materials with strong viscosity, such as wet powders, slurries, or pastes, the ultrasonic vibrating sieve provides a significant advantage. The high-frequency vibrations reduce the surface tension and make it easier for viscous materials to flow through the mesh. This results in uninterrupted screening and higher throughput, even when handling sticky, thick, or slurry-based materials. - Preventing Adsorption and Aggregation
For materials that are prone to adsorption, like activated carbon, fine chemicals, and pharmaceuticals, ultrasonic waves effectively break the adhesion forces. The high-frequency vibrations help dislodge particles that would otherwise stick to the mesh, ensuring a smoother screening process. This reduces the likelihood of particles sticking to the mesh and ensures consistent separation for accurate product quality. - Reducing Agglomeration and Clumping
Materials that are prone to clumping, such as fine powders or granular substances, can be effectively screened using ultrasonic vibrating sieves. The ultrasonic waves prevent particle agglomeration, keeping the material in its desired particle size range and facilitating easier flow through the screen. This reduces the need for manual intervention, ensuring a more efficient and automated screening process. - Enhanced Screening Efficiency for Fine Particles
Ultrasonic vibrating sieves are especially effective when working with fine materials, which are typically more prone to clogging, aggregation, or sticking. The ultrasonic vibration prevents the fine particles from clustering together, allowing the screen to operate with a high level of accuracy and throughput. This makes ultrasonic vibrating sieves ideal for industries like pharmaceuticals, chemicals, and food processing, where fine and consistent material separation is essential.
Key Benefits of Ultrasonic Vibrating Sieves
- Increased Screening Efficiency: Ultrasonic vibrations enhance the screening process, allowing for higher throughput even with challenging materials.
- Reduced Downtime: By preventing blockages and reducing the need for manual cleaning, ultrasonic vibrating sieve minimize downtime and ensure a continuous production flow.
- Enhanced Product Quality: The ability to accurately separate particles of varying sizes ensures that only high-quality material reaches the next stage of production.
- Cost-Effective: Reduced maintenance, fewer interruptions, and higher throughput result in a more cost-efficient screening process.
- Versatility: Ultrasonic vibrating sieves can be customized to handle a wide range of materials, including powders, granules, slurries, and liquids.
Applications of Ultrasonic Vibrating Sieve
Ultrasonic vibrating sieves have become indispensable in industries that deal with fine, sticky, or viscous materials. Some common applications include:
- Activated Carbon Screening: For ensuring uniform particle size and preventing dust emissions.
- Pharmaceuticals: For sifting active ingredients, powders, and granules to ensure the correct particle size.
- Food and Beverage: For screening spices, powdered ingredients, and other fine materials.
- Chemicals: For separating chemicals, pigments, and fine powders used in manufacturing.
- Mining and Minerals: For sifting fine mineral particles or processing materials that are prone to sticking.
For an introduction to ultrasonic vibrating sieves, please refer to the battery material page, which introduces the characteristics of ultrasonic vibrating sieves and material characteristics.