In modern mineral processing operations, the management of tailings—particularly their moisture content—has become increasingly important for both environmental and operational reasons. One of the most effective technologies for reducing the moisture content of tailings is the high-frequency dewatering screen, also commonly referred to as a dewatering vibrating screen.
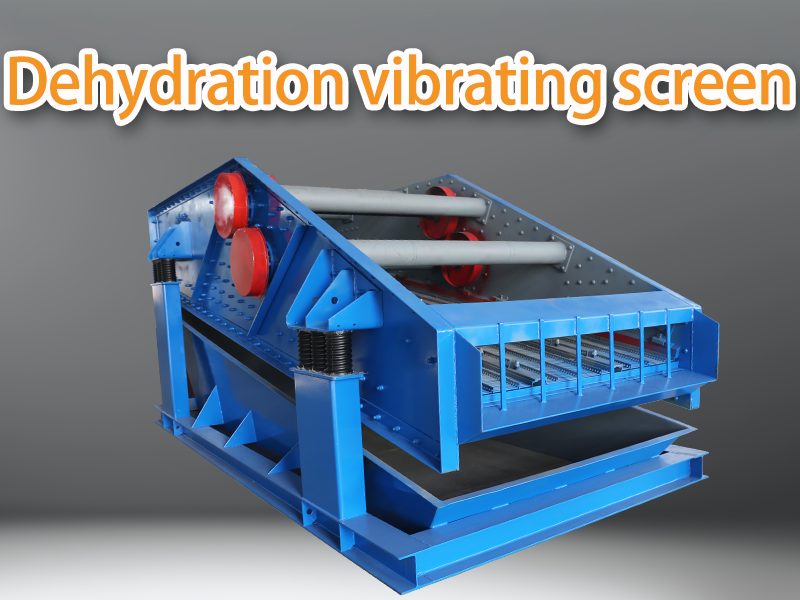
What is a High-Frequency Dewatering Screen?
A high-frequency dewatering screen is a specialized piece of equipment designed to separate liquids from solid materials through vibration and screening. It operates by applying high-frequency vibration to the screen deck, which alters the surface tension of the slurry. This vibratory action breaks the cohesive force of water molecules at the surface of the slurry, allowing water to pass through the screen mesh while retaining fine solid particles on the surface.
How It Works
When tailings slurry is fed onto the screen surface, the vibration forces cause the water to separate quickly from the solid particles. The liquid component (water) penetrates through the screen and is collected as underflow, while the fine materials, unable to pass through the screen mesh, begin to accumulate and form a cake-like layer. This filter cake is continuously moved forward by the combined effect of vibration and the screen’s inclination until it is discharged at the end of the deck.
This unique design allows for a highly efficient separation process, significantly reducing the water content in the discharged solids. The result is a much drier material, often referred to as “dry tailings,” which is easier to handle, store, or transport.
Advantages in Tailings Management
The use of high-frequency dewatering screens in tailings dewatering offers several notable advantages:
- Low Moisture Content: The primary benefit is the ability to reduce the water content of tailings to a very low level, which facilitates dry stacking and minimizes the need for large tailings ponds.
- Environmental Compliance: By reducing the volume of slurry and improving solid-liquid separation, operators can better meet environmental regulations and minimize potential ecological risks.
- Improved Water Recovery: The water that is separated from the tailings can be recovered and reused in the processing plant, improving water efficiency and reducing operational costs.
- Space and Cost Savings: Dry tailings reduce the footprint and infrastructure required for tailings storage, lowering both capital and maintenance expenses.