In the world of industrial processing, precision and efficiency are key factors in ensuring optimal performance and product quality. One often-overlooked yet critical component in achieving this is the screen mesh used for material separation and filtration. Customized screen mesh solutions are becoming increasingly popular in industries where accurate material grading and separation are essential. Whether you're dealing with fine powders, coarse granules, or liquid-solid separation, the ability to tailor the mesh to meet specific operational needs can provide significant advantages in terms of screening precision and overall production efficiency.
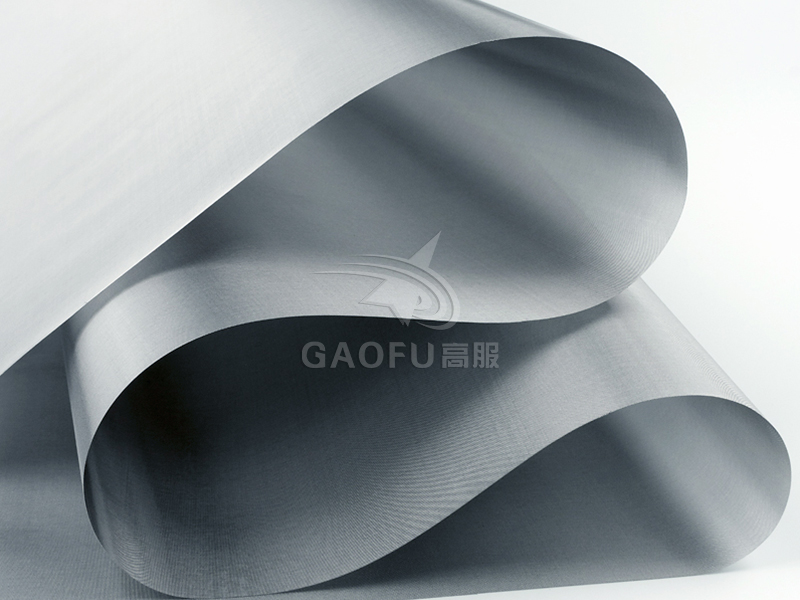
The Importance of Precision in Screening
Screening is an essential process in various industries such as pharmaceuticals, food processing, chemical manufacturing, and mining, where the need for consistent and uniform separation of materials is paramount. Using the right screen mesh ensures that materials are sorted accurately, with the desired particle sizes separated from the rest. Customized screen mesh solutions allow businesses to fine-tune their screening process based on the unique characteristics of the materials they are working with, ensuring that each application is handled with the highest degree of precision.
The customization of screen mesh means that businesses can choose mesh sizes, shapes, and materials that align perfectly with their specific requirements, providing several key benefits that make it an indispensable part of the production process.
Why Customization Matters in Screen Mesh
✅ Tailored for Specific Materials and Applications
One of the major benefits of customized screen mesh is the ability to tailor the mesh according to the unique characteristics of the materials being processed. For example, in industries like food production, the mesh may need to handle a wide variety of materials ranging from powders to larger particles. In these cases, the mesh size and material type can be adjusted to ensure that the screening process is as effective as possible. Whether you're processing fine powder or coarse granules, having a customized screen mesh ensures that your system can handle the material with the right level of precision, minimizing waste and improving overall quality.
✅ Improved Screening Accuracy
With a customized solution, you can choose mesh sizes and configurations that meet specific production goals. This leads to greater accuracy in screening by ensuring that unwanted particles are effectively separated from the desired material. Precise screening ensures that high-quality and uniform products are produced while eliminating potential contamination or inconsistencies. Whether it’s separating small particles from larger ones or filtering out foreign objects, customized screen mesh allows you to achieve the perfect separation with minimal loss of good material.
✅ Enhanced Durability and Performance
Customized screen mesh isn’t just about the right size—it’s also about choosing the right material for the job. Depending on the environment and the materials being processed, a variety of materials such as stainless steel, polyurethane, or nylon can be used. Each material offers different levels of abrasion resistance, corrosion resistance, and flexibility, depending on the specific needs of the application. By selecting the right material for your customized mesh, you enhance the durability and performance of your screening system, ensuring it can handle even the harshest conditions while maintaining accuracy and efficiency.
Key Benefits of Customized Screen Mesh Solutions
✅ Optimized Production Processes
Customized screen mesh can significantly improve the overall efficiency of your production line. By ensuring that your materials are accurately separated and processed, you can avoid costly reprocessing and wastage. With custom solutions, you can achieve better resource utilization, ensuring that every batch is as efficient as possible.
In industries where high throughput and continuous operation are critical, customized screen mesh ensures that the screening process runs smoothly, with fewer interruptions for cleaning, maintenance, or mesh replacement.
✅ Reduced Operational Costs
Although a customized screen mesh solution may come at a slightly higher initial cost, the long-term savings far outweigh the investment. With precise and accurate screening, you reduce the chances of needing to reprocess materials or deal with quality issues, ultimately leading to fewer wasted materials and lower labor costs for rework. Additionally, the enhanced durability of customized mesh reduces the need for frequent replacements and repairs, saving on maintenance costs.
✅ Increased Product Quality
Precision in screening directly leads to better product quality. When materials are accurately separated according to size, the resulting product is of higher quality and consistency. In industries like pharmaceuticals or food processing, where product quality is paramount, having the ability to customize the screen mesh means you can achieve the exact specifications necessary for compliance with industry standards. This helps to improve the reputation of your products and ensures customer satisfaction.
Applications of Customized Screen Mesh in Various Industries
Food and Beverage Industry
In food processing, different ingredients need to be separated based on their size, shape, and density. Customized screen mesh is crucial for ensuring that ingredients such as grains, flour, or spices are accurately graded to the desired specifications. It also plays an essential role in removing contaminants like stones or debris from raw materials.
Pharmaceutical Industry
For pharmaceuticals, where the purity and accuracy of materials are crucial, customized screen mesh ensures that only the desired particle size enters the production process. This is particularly important when dealing with fine powders or sensitive materials that must not be contaminated.
Chemical and Mining Industries
In chemical manufacturing and mining, where large volumes of abrasive materials are processed, customized screen mesh can be used to separate materials based on size, shape, or even material type. This ensures efficient processing and minimizes wear on the equipment, while allowing for precise material sorting.