This guide provides a comprehensive overview of common motor issues, their potential causes, and recommended solutions. The information is organized into a table format for easy reference.
1. Power Socket (Motor Fails to Start)
- Possible Causes:
- Stator winding short circuit, open circuit, or grounding.
- Incorrect stator winding connection.
- Overload or rotor blockage.
- Solutions:
- Inspect and repair the short circuit, open circuit, or grounding.
- Check and correct the wiring connections.
- Reduce the load or remove the obstruction.
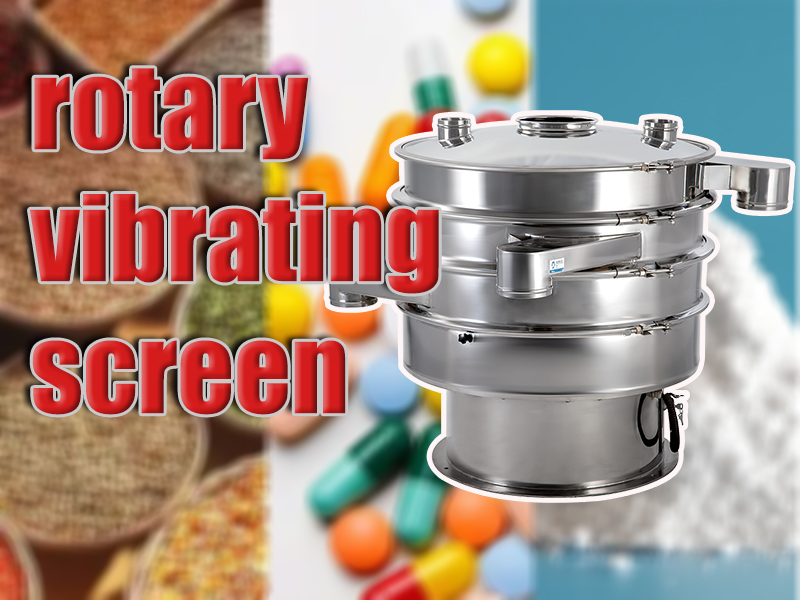
2. Motor Overheating or Noise
- Possible Causes:
- Overload.
- Winding short circuit.
- Incorrect winding connection.
- Wiring or circuit issues.
- Rotor bar breakage.
- Stator issues during operation.
- Low power supply voltage.
- Solutions:
- Reduce the load or replace damaged parts.
- Locate and repair the short circuit.
- Check and correct the winding connections.
- Avoid faults and repair the circuit.
- Replace the rotor.
- Measure internal motor and bearing clearances for repairs.
- Ensure adequate power supply voltage.
3. Bearing Overheating
- Possible Causes:
- Bearing wear or oil leakage.
- Improper lubrication or poor-quality bearings.
- Loose or tight fit between the bearing inner ring and the shaft.
- Loose or tight fit between the bearing outer ring and the housing.
- Improper installation or wear of the housing bearing.
- Solutions:
- Replace the bearing.
- Adjust the lubrication.
- For a loose fit, add a shim; for a tight fit, re-machine the shaft.
- For a loose fit, expand the housing; for a tight fit, re-machine the bearing housing.
- Reinstall the bearing to ensure even distribution.
4. Motor Case Electrification
- Possible Causes:
- Winding insulation damage.
- Winding moisture.
- Damaged leads or excessive dirt.
- Solutions:
- Repair the insulation and clean/dry the motor.
- Dry or clean and dry the motor.
- Replace the leads and clean the dirt.
5. Screw Breakage
- Possible Causes:
- Resonance due to improper bolt installation.
- Uneven installation surface.
- Solutions:
- Install the bolts correctly.
- Re-machine the installation surface.
6. Motor Operation Issues
- Possible Causes:
- Power supply issues.
- Insufficient cable length causing poor contact.
- Burnt cable.
- Single-phase operation with loose coils.
- Excessive lubrication.
- Insufficient lubrication.
- Solutions:
- Turn on the switch.
- Replace the cable.
- Replace the burnt cable.
- Replace the motor.
- Maintain continuous operation.
- Add appropriate lubrication.
7. Abnormal Noises
- Possible Causes:
- Damaged epoxy bolts.
- Incomplete epoxy embedding.
- Misaligned ball plate.
- Cracked ball plate.
- Unstable motor base.
- Broken spring.
- Contact between motor and other hardware.
- Loose motor and pulley contact.
- Contact between discharge port and objective lens.
- Unremoved motion gaps or bolts.
- Solutions:
- Replace the damaged bolts.
- Use pliers to assist embedding.
- Align the ball plate correctly.
- Replace the ball plate.
- Stabilize the motor base.
- Replace the spring.
- Create a 10cm space.
- Ensure proper sealing.
- Prevent contact.
- Remove motion gaps or bolts.
8. Irregular Material Discharge
- Possible Causes:
- Incorrect motor rotation direction.
- Excessive angle between upper and lower surfaces.
- Incorrect surface alignment.
- Solutions:
- Correct the motor rotation direction.
- Adjust the angle.
- Correct the surface alignment.
9. Slow Discharge
- Possible Causes:
- Direct extraction of two items.
- Loose belt.
- Damaged belt.
- Loose or rotten seal.
- Solutions:
- Adjust the extraction method.
- Tighten the belt.
- Replace the belt.
- Tighten or replace the seal.
10. Discharge Port Misalignment
- Possible Causes:
- Excessive bending moment from heavy loads.
- Damaged epoxy.
- Solutions:
- Isolate the discharge port.
- Tighten the ring.