In the chemical industry, the purity of raw materials and finished products plays a critical role in ensuring the quality, safety, and performance of the products. This is particularly true in the case of flame retardants, where precise material screening is necessary to meet industry standards. One of the most effective tools for achieving this is the rotary vibrating screen. This article explores how rotary vibrating screens facilitate impurity removal and streamline flame retardant production processes.
What is a Rotary Vibrating Screen?
A rotary vibrating screen is a high-precision screening device that separates materials by size using a circular or elliptical motion. It consists of a screen mesh, a motor, and a vibration source, which work together to classify and remove impurities from materials. The screen's design allows it to handle a wide range of materials, including powders, granules, and liquids.
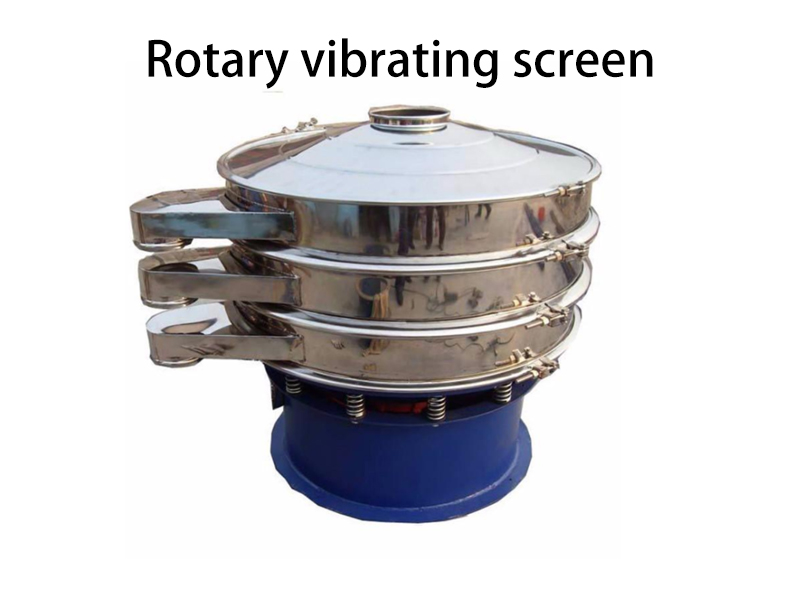
The Importance of Screening Flame Retardants
Flame retardants are widely used in various applications, such as electronics, construction materials, textiles, and automotive components, to reduce the risk of fire. The quality of these flame retardants is critical, as even small impurities can compromise their effectiveness or alter their chemical properties.
Key Benefits of Using Rotary Vibrating Screens for Flame Retardants
1、Precision Screening
Rotary vibrating screens are designed to provide high-accuracy particle separation. Their multi-layer design allows for simultaneous screening of materials into different size fractions, ensuring that only particles of the desired size pass through.
2、Efficient Impurity Removal
By separating unwanted particles such as dust, debris, or oversized granules, rotary vibrating screens ensure the purity of the flame retardant material. This improves the performance of the final product and minimizes the risk of defects.
3、High Screening Efficiency
The vibrating motion of the screen facilitates faster material flow and better contact with the mesh, resulting in a higher screening rate. This efficiency is essential for large-scale production processes.
4、Versatility and Customization
Rotary vibrating screens can be tailored to meet specific requirements. The mesh size, vibration frequency, and screen deck configuration can be adjusted to handle different types of flame retardants and achieve optimal results.
5、Low Maintenance and Durability
With robust construction and simple operation, rotary vibrating screens require minimal maintenance. Their durable design ensures a long operational life, reducing downtime and increasing productivity.
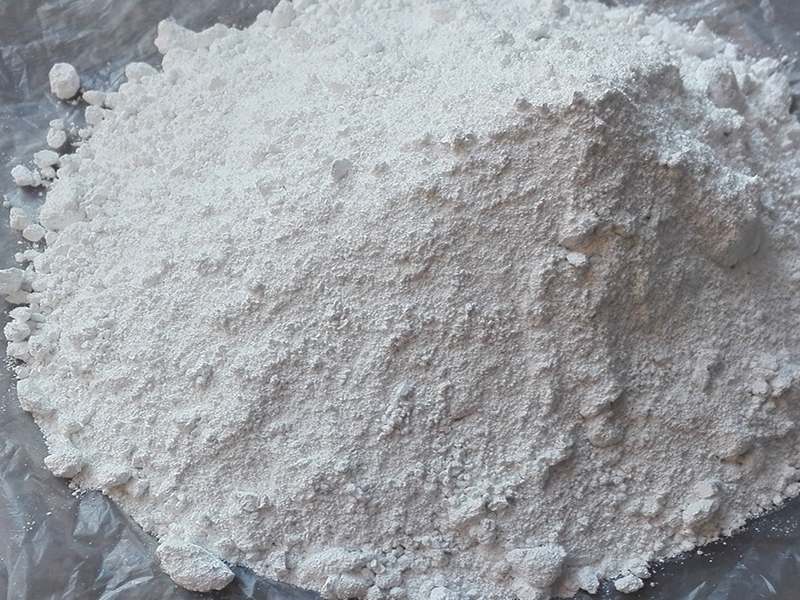
Applications of Rotary Vibrating Screens in Flame Retardant Production
1、Powder Screening
Rotary screens are highly effective in screening flame retardant powders, ensuring uniform particle size and removing impurities.
2、Granule Classification
In the case of granular flame retardants, the screens separate materials based on size, ensuring consistency in production.
3、Liquid-Solid Separation
For flame retardants in liquid form, rotary vibrating screens can separate solid impurities from the liquid mixture, enhancing the quality of the end product.
For an introduction to the rotary vibrating screen, please refer to the rubber additives page, which introduces the process flow of material screening.
Choosing the Right Rotary Vibrating Screen
Selecting the right rotary vibrating screen depends on several factors, including the material's properties, desired particle size, production capacity, and environmental considerations. It is essential to work with a trusted manufacturer to ensure the equipment meets the specific needs of flame retardant production.