Antimony oxide (Sb₂O₃) is a fine, powdery material widely used in flame retardants, ceramics, glass, electronics, and chemical industries. Due to its ultra-fine particle size, tendency to agglomerate, and powdery nature, traditional screening methods often struggle with mesh clogging, inconsistent separation, and inefficient throughput.
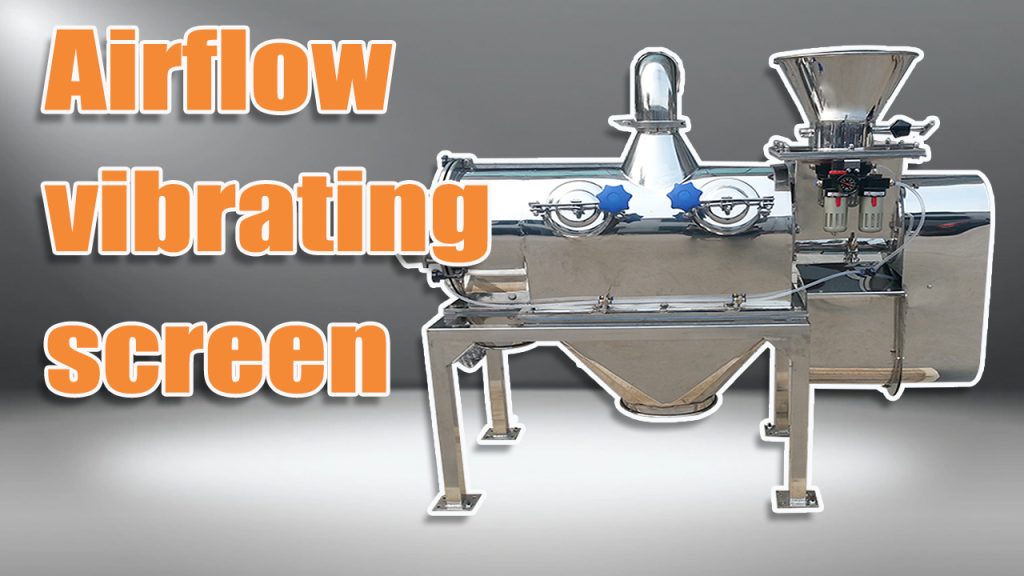
Our Airflow Vibrating Sieve is specifically designed to overcome these challenges, offering a high-efficiency, clog-free, and precision screening solution for antimony oxide powder. Using airflow-assisted separation technology, this sieve ensures that fine and ultra-fine particles are effectively classified, maintaining optimal product quality and production efficiency.
Why Choose Our Airflow Vibrating Sieve for Antimony Oxide Powder?
1. High-Precision Screening for Ultra-Fine Powders
- Traditional vibrating screens often clog when handling ultra-fine powders like antimony oxide, reducing efficiency.
- Our airflow vibrating sieve utilizes cyclone airflow technology, allowing fine particles to pass through the mesh smoothly, preventing blockages and production delays.
- This ensures high-precision classification and consistent particle distribution for various industrial applications.
2. Prevents Agglomeration & Improves Flowability
- Antimony oxide powder tends to clump together, making it difficult to screen with conventional equipment.
- Our sieve’s airflow-assisted dispersion technology breaks apart agglomerated particles, ensuring uniform separation and better material flow.
- This results in higher screening efficiency and improved product consistency.
3. Continuous & Clog-Free Operation for Maximum Productivity
- The self-cleaning system prevents mesh clogging, reducing downtime and maintenance.
- Unlike traditional sieves that require frequent stoppages for cleaning, our airflow sieve ensures continuous, uninterrupted operation.
- This is especially important in high-demand production environments where efficiency is key.
4. High Throughput for Large-Scale Industrial Applications
- Designed for high-capacity screening, our airflow sieve is capable of handling large volumes of antimony oxide powder efficiently.
- It ensures that manufacturers can meet production demands without compromising on quality.
- Whether for small-batch specialized applications or large-scale industrial processing, our sieve adapts to different production needs.
5. Closed-System Design for Dust-Free Operation
- Antimony oxide is a fine powder that can easily become airborne, leading to material loss and workplace contamination.
- Our sealed, enclosed design prevents dust leakage, ensuring a cleaner, safer working environment.
- This is crucial for industries with strict environmental and safety regulations.
Industries That Benefit from Our Airflow Vibrating Sieve for Antimony Oxide Powder
✔ Flame Retardant Industry – Ensuring precise antimony oxide particle classification for high-performance flame-retardant applications.
✔ Ceramics & Glass – Maintaining consistent particle size for improved material properties in glass and ceramics production.
✔ Electronics & Semiconductor Manufacturing – Ensuring high-purity screening for specialized electronic applications.
✔ Chemical Industry – Providing fine particle separation for industrial chemical formulations.
Why Our Airflow Vibrating Sieve Stands Out?
🔹 Designed for Ultra-Fine Powders – Prevents clogging and ensures smooth powder flow.
🔹 Prevents Agglomeration – Uses airflow-assisted dispersion for uniform particle separation.
🔹 Continuous, High-Capacity Operation – Built for large-scale industrial screening.
🔹 Self-Cleaning System – Minimizes maintenance and reduces downtime.
🔹 Dust-Free Enclosed Design – Prevents material loss and workplace contamination.