This article delves into the crucial role of the tumbler vibrating screen in the classification of xylitol. It explores how this screening equipment enhances the efficiency and precision of xylitol production processes, ensuring the quality of the final product. By analyzing its working principles, advantages, and practical applications, a comprehensive understanding of its significance in the xylitol industry will be achieved.
1. Introduction
Xylitol, a polyol with a wide range of applications in the food, pharmaceutical, and dental industries, demands strict quality control during its production. Particle size distribution is a key factor influencing its properties, such as solubility, flowability, and tabletability. The tumbler vibrating screen emerges as an essential tool for accurately classifying xylitol particles.
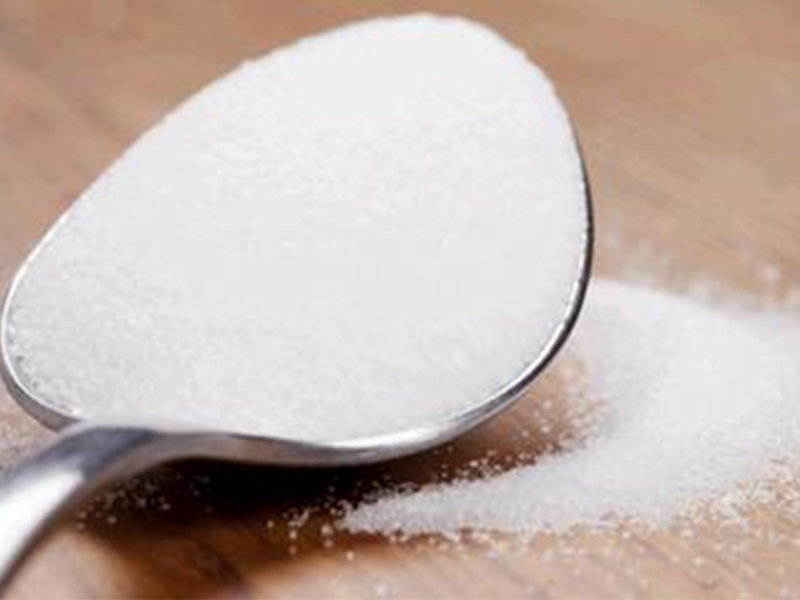
2. Working Principles of the Tumbler Vibrating Screen
- Vibrational Motion: The tumbler vibrating screen operates based on a carefully calibrated vibrational mechanism. Electric motors generate high-frequency vibrations, which are transmitted to the screening surface. These vibrations cause the xylitol particles to move in a complex, three-dimensional motion. As the screen deck shakes, particles smaller than the apertures of the screen mesh start to pass through, while larger ones are retained.
- Tumbler Design: The unique tumbling action is a defining feature. The screen body is designed in a way that encourages the particles to roll and flip continuously. This tumbling effect not only aids in the separation process but also prevents the clogging of the screen mesh. The particles are constantly reoriented, maximizing the probability of accurate classification.
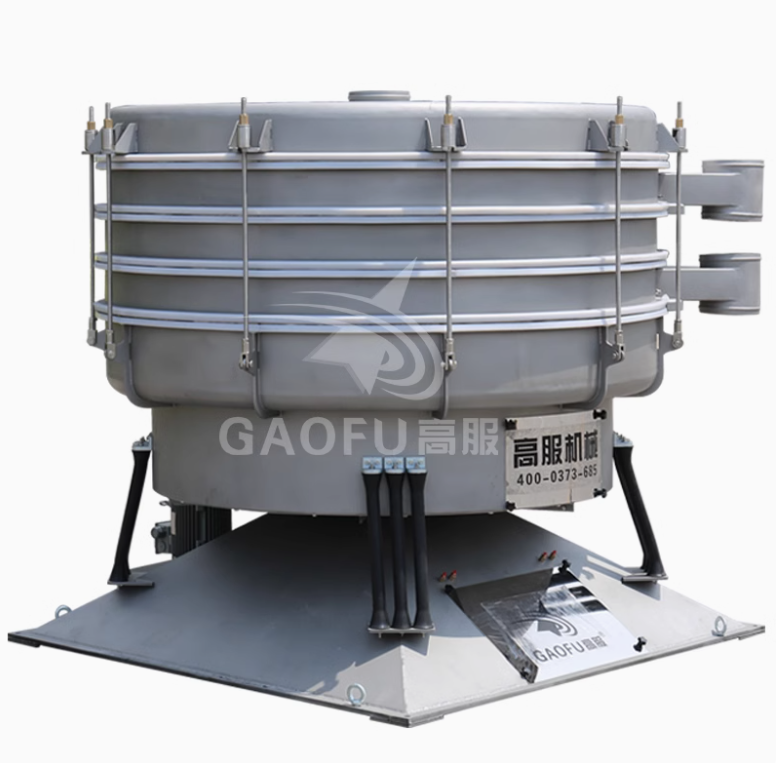
3. Advantages of Using Tumbler Vibrating Screen for Xylitol Classification
3.1 High Precision
- The adjustable vibration frequency and amplitude allow for precise control over the screening process. Manufacturers can customize the operation parameters according to the required xylitol particle size fractions. This precision ensures that each batch of xylitol meets the strict particle size specifications, which is vital for products like sugar-free candies or pharmaceutical tablets where consistent texture and dissolution rates are key.
3.2 High Efficiency
- Compared to traditional static sieves, the tumbler vibrating screen can process large volumes of xylitol in a relatively short time. The continuous vibration and tumbling motion keep the particles in constant flux, enabling rapid separation. This increased throughput is highly beneficial for large-scale xylitol production plants, reducing production time and costs.
3.3 Low Maintenance
- The robust construction of the tumbler vibrating screen minimizes the need for frequent repairs. The components are designed to withstand the abrasive nature of xylitol particles and the continuous vibrations. Additionally, the anti-clogging feature reduces the downtime required for manual mesh cleaning, further contributing to seamless production operations.
4. Practical Applications in Xylitol Production
4.1 Pre-packaging Classification
- Before xylitol is packaged for retail sale, it needs to be sorted into different grades based on particle size. The tumbler vibrating screen effectively separates the fine, medium, and coarse particles. Fine xylitol is often preferred for instant dissolving products, while coarser particles may be used in chewing gums. By accurately classifying the particles, manufacturers can meet the diverse needs of consumers.
4.2 Pharmaceutical Formulation
- In the pharmaceutical industry, xylitol is used as an excipient in tablet formulations. The tumbler vibrating screen ensures that the xylitol particles are of a uniform size, which is crucial for consistent tablet compression. Uniform particle size promotes even drug distribution within the tablet matrix, improving the efficacy and stability of the final pharmaceutical product.
4.3 Quality Control
- Throughout the xylitol production process, the tumbler vibrating screen serves as a key component in quality control. By regularly sampling and screening the product at different stages, manufacturers can detect any irregularities in particle size early on. This allows for timely adjustments to the production parameters, preventing the production of substandard xylitol batches.