In industrial processing, particularly in the chemical and pharmaceutical industries, efficient and precise material screening plays a critical role in ensuring the quality and consistency of products. One such material is Triethylenediamine (TEDA), a versatile organic compound used in a variety of applications, including as a curing agent in plastics, adhesives, and coatings. Screening this material requires specialized equipment, and the Tumbler Vibrating Screen is a key solution for achieving high-quality results.
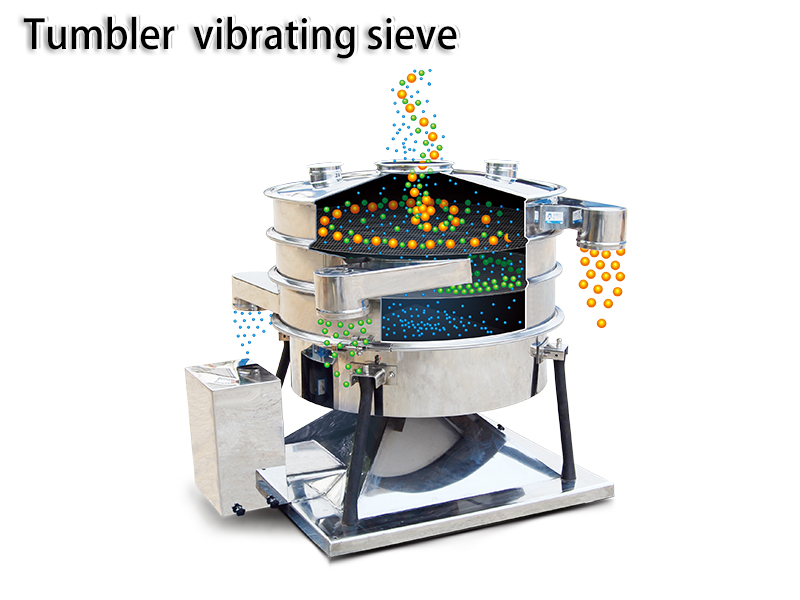
The Importance of Screening Triethylenediamine (TEDA)
Triethylenediamine (TEDA), due to its chemical properties, often comes in the form of fine powders or granules. In industries where consistency and purity are crucial, it is essential to separate unwanted particles and ensure uniform particle size distribution for optimal performance in end applications. A lack of proper screening can lead to the following issues:
- Inconsistent Product Quality – Impurities or variations in size can affect the functionality and performance of TEDA in various chemical processes.
- Clogging of Equipment – Unscreened TEDA may contain larger particles that can cause blockages in production lines or machinery.
- Safety Hazards – The improper handling of TEDA can lead to contamination or dangerous reactions in the manufacturing environment.
This makes screening TEDA a vital step in ensuring that the material meets the required specifications and maintains its intended properties.
Why Choose a Tumbler Vibrating Screen for TEDA Screening?
The Tumbler Vibrating Screen is an ideal choice for screening Triethylenediamine due to its ability to provide efficient, reliable, and consistent results, even for delicate and fine materials. Here’s why it is an excellent option for screening TEDA:
- High Screening Efficiency
The Tumbler Vibrating Screen operates using a unique three-dimensional motion that mimics the manual sieving process. This gentle action ensures that even fine particles like TEDA are effectively separated without causing damage to the material. High efficiency means fewer passes are needed, reducing both time and labor costs. - Precise Particle Size Separation
The machine is equipped with multiple layers of mesh, allowing for precise separation of particles based on size. Whether you’re dealing with coarse TEDA or finer powders, the Tumbler Vibrating Screen can help you achieve the desired particle distribution, ensuring that the material meets the necessary specifications. - Low Vibration and Noise
One of the key advantages of the Tumbler Vibrating Screen is its low vibration levels, which makes it suitable for delicate materials like TEDA. It operates quietly, reducing noise pollution in the workplace and providing a safer and more comfortable working environment. - Scalability and Customization
The Tumbler Vibrating Screen is highly customizable, offering different mesh sizes and screen configurations to suit the specific needs of TEDA screening. Additionally, it can be scaled up or down depending on production capacity, making it a versatile option for both small and large-scale operations.
Key Benefits of Using Tumbler Vibrating Screens for TEDA
- Enhanced Product Quality
Using a Tumbler Vibrating Screen ensures that only properly sized TEDA particles pass through, improving the overall quality and consistency of the material. This is crucial for industries that depend on precise chemical formulations and uniformity, such as plastics or coatings. - Increased Operational Efficiency
The high throughput of the Tumbler Vibrating Screen means that manufacturers can process large quantities of TEDA in a shorter amount of time. This increased efficiency leads to faster production cycles and, consequently, higher output levels. - Reduced Maintenance Costs
The durability of the Tumbler Vibrating Screen minimizes the risk of breakdowns, reducing maintenance costs and downtime. Its simple design also makes it easy to clean and maintain, which is especially important when working with materials like TEDA that require high levels of purity. - Improved Safety Standards
By screening TEDA properly, the likelihood of contamination and reaction hazards in subsequent processing steps is greatly reduced. This contributes to safer working conditions for employees and ensures compliance with safety regulations in industrial environments.