Ultrasonic vibrating screens represent a significant advancement in screening technology, offering a highly effective solution for handling fine powders, sticky materials, and other challenging substances. By integrating ultrasonic technology with traditional vibrating screen systems, these machines deliver superior performance, precision, and efficiency. This article provides an in-depth analysis of the working principle and technical characteristics of ultrasonic vibrating screens, highlighting their unique advantages and applications.
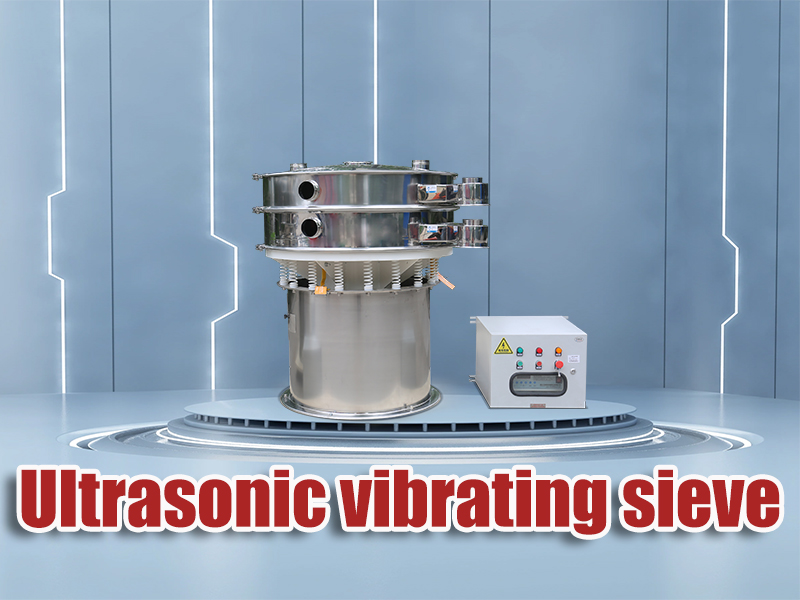
Working Principle of Ultrasonic Vibrating Screens
The ultrasonic vibrating screen combines two distinct mechanisms to achieve optimal screening performance: mechanical vibration and ultrasonic vibration. Here’s how it works:
- Mechanical Vibration
Like traditional vibrating screens, ultrasonic vibrating screens use a motor with eccentric weights to generate mechanical vibrations. These vibrations create a three-dimensional motion (horizontal, vertical, and inclined) that moves the material across the screen surface, allowing particles to pass through the mesh based on their size.
2. Ultrasonic Vibration
The key differentiator of ultrasonic vibrating screens is the addition of an ultrasonic system. An ultrasonic transducer is attached to the screen mesh, which generates high-frequency ultrasonic vibrations (typically in the range of 20 kHz to 40 kHz). These vibrations are transmitted directly to the screen surface, creating a secondary vibration that acts on the particles.
- Dislodging Trapped Particles: The ultrasonic vibrations break up agglomerates and dislodge particles that may have become trapped in the mesh openings.
- Preventing Adhesion: The high-frequency vibrations prevent sticky or moist materials from adhering to the screen mesh.
- Enhancing Particle Movement: The ultrasonic energy ensures that even fine powders and irregularly shaped particles move freely across the screen surface, improving screening efficiency.
The combination of mechanical and ultrasonic vibrations ensures that the screen operates at peak efficiency, even when handling materials that are prone to clogging or difficult to screen.
Technical Characteristics of Ultrasonic Vibrating Screens
Ultrasonic vibrating screens are designed with several advanced technical features that set them apart from traditional screening equipment. These characteristics contribute to their superior performance and versatility:
- High-Frequency Ultrasonic System
The ultrasonic system operates at frequencies ranging from 20 kHz to 40 kHz, generating vibrations that are imperceptible to the human ear but highly effective in preventing screen clogging. This system is powered by an ultrasonic generator, which converts electrical energy into mechanical vibrations.
2. Precision Screening
Ultrasonic vibrating screens offer exceptional precision in particle separation. The ultrasonic vibrations ensure that particles are screened according to their exact size, reducing the likelihood of oversized particles passing through the mesh. This is particularly important for industries that require strict quality control, such as pharmaceuticals and food processing.
3. Self-Cleaning Screen Mesh
The ultrasonic vibrations act as a self-cleaning mechanism, preventing material buildup on the screen mesh. This reduces the need for frequent manual cleaning and minimizes downtime, improving overall productivity.
4. Energy Efficiency
Despite their advanced technology, ultrasonic vibrating screens are designed to be energy-efficient. The ultrasonic system consumes minimal power, and the overall energy consumption is comparable to or lower than that of traditional vibrating screens.
5. Durable and Hygienic Construction
Ultrasonic vibrating screens are typically constructed from high-quality stainless steel, making them durable, corrosion-resistant, and easy to clean. This makes them ideal for industries with strict hygiene requirements, such as food, pharmaceuticals, and cosmetics.
6. Adjustable Vibration Parameters
The frequency and amplitude of both the mechanical and ultrasonic vibrations can be adjusted to suit different materials and screening requirements. This flexibility allows operators to optimize the screening process for maximum efficiency and accuracy.
7. Wide Range of Applications
Ultrasonic vibrating screens are highly versatile and can be used to screen a wide variety of materials, including fine powders, granules, and liquids. They are particularly effective for materials that are difficult to screen using traditional methods, such as sticky, moist, or hygroscopic substances.
Applications of Ultrasonic Vibrating Screens
Ultrasonic vibrating screens are widely used in industries where precision, efficiency, and hygiene are critical. Some common applications include:
- Food Industry: Screening flour, sugar, starch, and other food additives.
- Pharmaceuticals: Separating active pharmaceutical ingredients (APIs) and excipients.
- Chemicals: Screening pigments, resins, and other fine or sticky materials.
- Metallurgy: Separating metal powders and other fine particles.
- Cosmetics: Screening talc, mica, and other cosmetic powders.
- Ceramics: Separating ceramic powders and glazes.