In the food and pharmaceutical industries, lactose powder plays a critical role as both a functional ingredient and a carrier in numerous formulations. However, the quality and consistency of lactose powder directly influence product safety, performance, and consumer acceptance. To meet stringent quality standards, manufacturers must remove impurities and ensure uniform particle size during processing. This is where the airflow vibrating screen proves to be an essential tool—especially designed for continuous, efficient, and clean screening of fine powders like lactose.
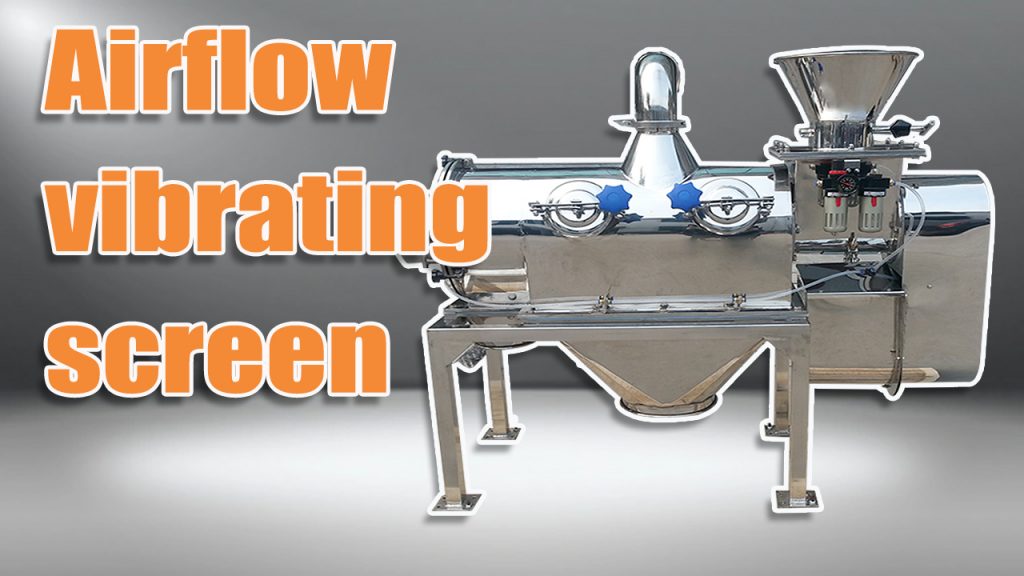
Why Airflow Vibrating Screens Are Ideal for Lactose Powder
Airflow vibrating screens are not conventional sieving devices. They are engineered to combine high-speed airflow with vibratory motion within a cylindrical screening chamber. This dual mechanism allows for high-throughput, low-resistance screening that minimizes product degradation and operational downtime.
When applied to lactose powder screening, the airflow vibrating screen offers a number of clear advantages:
1. Reliable and Continuous Operation
One of the standout features of airflow vibrating screens is their ability to run continuously for extended periods without interruption. In lactose powder processing, where consistency is key and downtime can be costly, this feature ensures uninterrupted production flow, reducing delays and maximizing efficiency. The robust structure and optimized design support long hours of operation while maintaining stable performance.
2. Effective Impurity Removal for High Purity Standards
Lactose, often used in infant formula, tablets, and nutritional powders, requires the highest levels of purity. Even small amounts of foreign matter can compromise product integrity. The airflow vibrating screen excels in removing oversized particles, fibers, and other contaminants, delivering a refined product that meets strict food and pharmaceutical grade specifications.
3. Automatic Mesh Cleaning by Cyclonic Airflow
Another key advantage is the equipment’s automatic mesh cleaning function. During the screening process, the cyclonic airflow continuously scours the screen mesh, preventing material buildup and clogging. This self-cleaning action extends the lifespan of the mesh, reduces manual maintenance, and ensures consistent throughput and screening accuracy, even during prolonged operation.
4. Safe and Hygienic Design
The system is fully enclosed, minimizing the risk of contamination and exposure to airborne dust—an especially important feature in the handling of lactose powder, which can be sensitive to moisture and contamination. The sealed structure also enhances operator safety and simplifies cleaning between production runs.
5. Energy-Efficient and Space-Saving
Despite its high functionality, the airflow vibrating screen is energy-efficient and features a compact footprint, making it ideal for integration into existing lactose powder production lines without requiring significant layout changes or excessive power consumption.
Applications and Industry Relevance
Airflow vibrating screens are now widely adopted in:
- Dairy product processing plants
- Pharmaceutical ingredient manufacturing
- Infant formula production lines
- Nutraceutical and supplement factories
For all these sectors, lactose powder must be handled with precision, and the airflow vibrating screen meets this demand by delivering clean, uniform, and high-quality powder ready for downstream use.