In the processing of metal powders, maintaining high purity and consistent quality is a top priority. Whether in additive manufacturing, metallurgy, electronics, or aerospace applications, even the slightest impurities in metal powders can lead to defects, inefficiencies, and compromised performance in final products. One highly effective solution to ensure metal powder purity is the use of ultrasonic vibrating screen—an advanced screening technology that goes beyond traditional sieving methods.
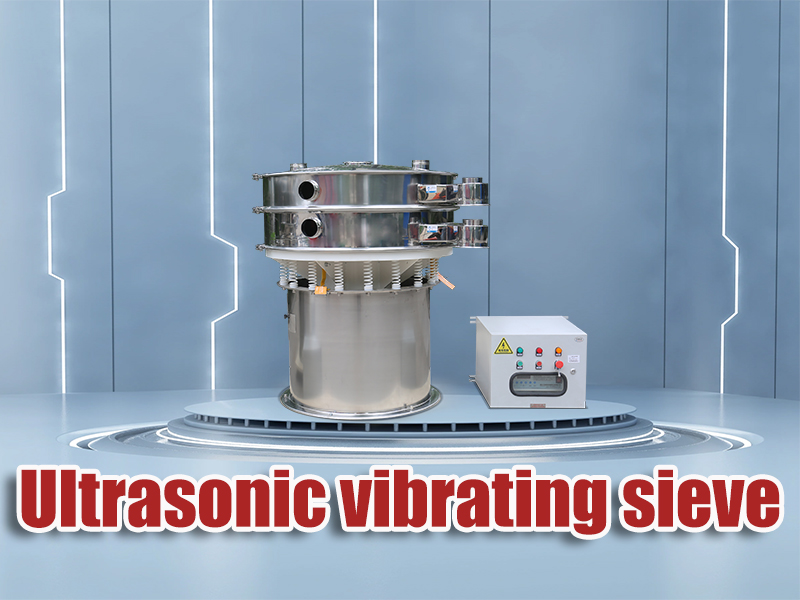
Enhancing Purity by Removing Impurities
The primary function of ultrasonic vibrating screens is to remove contaminants and unwanted particles from metal powders. This process significantly improves the overall purity and quality of the material, ensuring that only particles of the desired size and composition pass through. By eliminating oversized particles, debris, and other impurities, ultrasonic screening contributes to higher product integrity and better downstream performance.
Solving the Challenge of Difficult-to-Screen Materials
Metal powders often exhibit challenging physical properties that make traditional screening methods ineffective. These materials may be:
- Highly adhesive
- Strongly cohesive or prone to agglomeration
- High in electrostatic charge
- Ultra-fine in size (micron or sub-micron scale)
- High in density
- Sticky or moisture-sensitive
Conventional vibratory screens often clog when processing such materials, leading to downtime, inconsistent screening results, and material loss. In contrast, ultrasonic vibrating screens utilize high-frequency ultrasonic waves (typically around 20 kHz) to introduce micro-vibrations on the screen surface. These vibrations effectively prevent mesh blockage, breaking apart agglomerated particles and allowing ultra-fine powders to pass through the mesh freely.
Increasing Efficiency and Throughput
Another key advantage of ultrasonic vibrating screens is their ability to dramatically increase screening efficiency and production output. Compared to standard screening systems, the use of ultrasonic technology can boost throughput by 2 to 5 times. This is achieved not only by preventing screen blinding but also by improving the flow rate of powders through the mesh.
For manufacturers, this means:
- Less downtime for cleaning or screen replacement
- Greater consistency in particle size distribution
- Higher production rates without compromising quality
- Reduced material waste and improved yield
Enabling Advanced Manufacturing Needs
As industries move toward more demanding production standards, especially in 3D printing, battery manufacturing, pharmaceuticals, and advanced electronics, the quality of raw materials becomes increasingly critical. Ultrasonic vibrating screens support these high standards by offering precision screening of materials that would otherwise be difficult or impossible to process effectively.