One of the key materials used in modern battery production, especially for electric vehicles (EVs) and energy storage systems (ESS), is Lithium Iron Phosphate (LFP). LFP is known for its excellent thermal stability, long cycle life, and safety characteristics, making it a preferred material for lithium-ion batteries. However, the performance and reliability of LFP batteries depend heavily on the purity of the raw materials used in production. To ensure the highest level of material purity, manufacturers have increasingly turned to ultrasonic vibrating screens as an effective solution for precise screening and impurity removal.
The Critical Role of High-Purity LFP in Battery Performance
Lithium iron phosphate (LiFePO₄) is widely used in lithium-ion batteries due to its stable chemical structure, high safety profile, and long lifespan. Unlike other lithium-based cathode materials, LFP offers superior thermal stability and resistance to overheating, making it ideal for electric vehicles and large-scale energy storage.
However, the presence of impurities in LFP materials can severely compromise battery performance. Impurities such as metal particles, dust, and agglomerates can lead to several issues, including:
- Reduced conductivity – Impurities can create resistance pathways, reducing the efficiency of ion and electron transport.
- Internal short circuits – Metal particles or other contaminants can cause micro-short circuits within the battery, posing safety risks and shortening battery life.
- Capacity degradation – Impurities can interfere with the electrochemical reactions within the cell, leading to faster capacity fade.
- Poor structural integrity – Inconsistent particle size and contamination can lead to cracks, delamination, and other mechanical issues within the electrode.
To prevent these problems and ensure the highest performance and safety standards, manufacturers must ensure that LFP materials are free from impurities and have a uniform particle size. This is where ultrasonic vibrating screens play a crucial role.
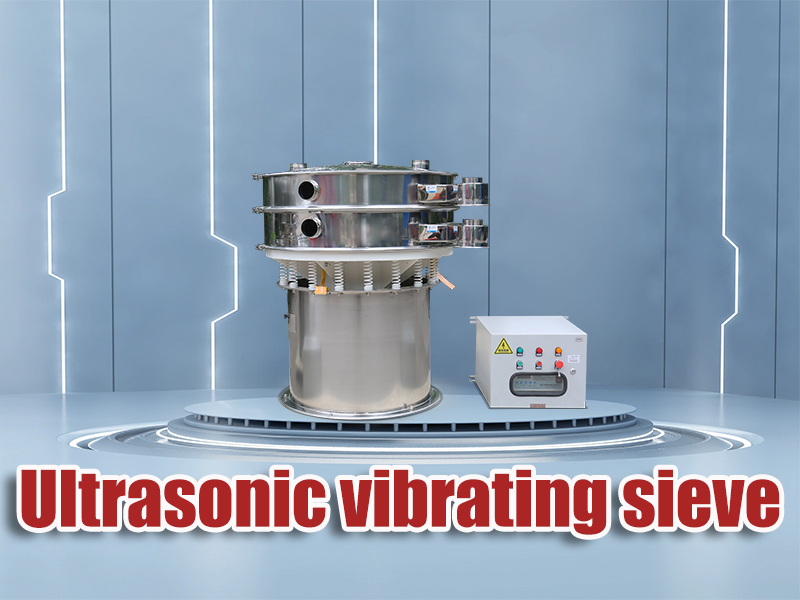
How Ultrasonic Vibrating Screens Work for LFP Screening
Ultrasonic vibrating screens combine traditional mechanical vibration with high-frequency ultrasonic energy to create an advanced screening system capable of processing fine powders and removing impurities with high precision.
Working Principle
- A standard vibrating screen generates mechanical vibration to separate particles based on size.
- An ultrasonic generator introduces high-frequency sound waves (usually in the range of 20–40 kHz) into the screen surface.
- The ultrasonic energy creates micro-vibrations on the screen mesh, which:
- Prevent particles from clogging the mesh (anti-blinding effect).
- Improve the fluidity of fine powders.
- Enhance the separation efficiency, even for very small particles.
- The combination of mechanical and ultrasonic vibrations ensures that only particles of the desired size pass through the mesh, while larger particles and impurities are effectively removed.
Unique Advantages for LFP Screening
- Anti-blinding Effect – LFP materials are typically very fine and prone to clogging traditional screens. Ultrasonic vibrations prevent particle buildup and keep the screen mesh clear.
- High Precision Screening – The ultrasonic energy allows for the separation of even the smallest particles, ensuring consistent particle size distribution and improved conductivity.
- Reduced Agglomeration – Ultrasonic waves help to break down particle clusters, ensuring that individual particles are uniformly processed.
- Minimal Material Loss – The enhanced separation efficiency ensures that valuable LFP material is retained, reducing waste and improving production yield.
Advantages of Using Ultrasonic Vibrating Screens for LFP
1. Higher Purity and Improved Battery Performance
By removing impurities and ensuring uniform particle size, ultrasonic vibrating screens improve the overall quality of LFP materials. This translates to higher battery capacity, better charge retention, and longer cycle life.
2. Enhanced Safety and Reliability
Impurities, especially metal particles, can cause internal short circuits and thermal runaway, leading to battery failure or even fire hazards. Ultrasonic screening ensures that contaminants are effectively removed, improving battery safety and reliability.
3. Increased Production Efficiency
Traditional screening methods often face limitations when handling fine powders like LFP. Ultrasonic vibrating screens increase screening speed and accuracy, reducing processing time and allowing manufacturers to scale up production without compromising quality.
4. Compatibility with Fine and Ultra-Fine Particles
LFP materials are typically processed into fine powders to enhance the surface area and improve ion exchange during battery operation. Ultrasonic screens are capable of handling ultra-fine particles down to the micrometer level, ensuring optimal material performance.
5. Reduced Equipment Wear and Maintenance Costs
The ultrasonic energy reduces friction and material buildup on the screen surface, minimizing wear and tear on the equipment. This extends the lifespan of the screening machine and reduces maintenance requirements, leading to lower operational costs.
Application of Ultrasonic Vibrating Screens in LFP Battery Production
Ultrasonic vibrating screens are used at multiple stages of LFP battery production to ensure material quality and consistency:
✔️ Raw Material Processing
Before LFP materials are introduced into the production line, they undergo ultrasonic screening to remove impurities and ensure consistent particle size.
✔️ Cathode Material Screening
LFP serves as the cathode material in lithium-ion batteries. Ultrasonic screening ensures that the cathode material has the right particle size and purity, improving battery efficiency and charge capacity.
✔️ Electrolyte Powder Screening
Fine electrolyte powders are also processed using ultrasonic vibrating screens to ensure they meet precise particle size requirements.
✔️ Battery Recycling and Reuse
As battery recycling becomes more important for sustainable production, ultrasonic screening is used to separate valuable LFP materials from recycled batteries, allowing them to be reused in new battery cells.
Why Ultrasonic Vibrating Screens Are Essential for LFP Batteries
The battery industry is under constant pressure to improve performance, reduce costs, and enhance safety. High-purity LFP materials are critical to achieving these goals. Ultrasonic vibrating screens provide a reliable and efficient solution for refining LFP materials, ensuring that manufacturers can meet the increasing demand for high-performance batteries.
By combining traditional mechanical vibration with ultrasonic energy, these advanced screening systems offer unmatched precision, efficiency, and consistency in material processing. As the demand for lithium-ion batteries continues to grow, ultrasonic vibrating screens will remain an essential tool for improving the quality and reliability of LFP battery materials.